複合パッケージングバッグの基本的な準備プロセスは、印刷、ラミネート、スライト、バッグ作成の4つのステップに分かれています。これは、ラミネートとバッグ作成の2つのプロセスが、最終製品のパフォーマンスに影響を与える重要なプロセスです。
複合プロセス
デザイン製品パッケージプロセスは、さまざまな基質の正しい選択に加えて、製品、組成、後処理条件、品質選択の品質要件の使用に応じて、複合接着剤の選択も重要です。複合加工技術がどれほど完璧であっても、間違った接着剤を選択すると、複合力、漏れ、壊れたバッグ、その他の障害の下で、力を減らすための後処理を引き起こします。
接着剤を備えた毎日の化学柔軟性パッケージの選択は、一般的に、複合接着剤として次の条件を満たす必要があるため、さまざまな要因を考慮してください:
無毒
液体の包装後に有害な抽出物は現れません。
食品貯蔵の温度要件に適用できます。
天気の良い抵抗、黄色と猛烈な、チョークや剥離なし。
オイル、フレーバー、酢、アルコールに対する耐性。
印刷パターンインクの侵食はありません。インクに対する親和性が高いと予想されます。
さらに、侵食に対する耐性において、コンテンツには多数のスパイス、アルコール、水、砂糖、脂肪酸などが含まれており、その特性は異なります。複合膜の内層を介して接着層に浸透し、腐食損傷を引き起こし、パッケージバッグの剥離を引き起こす可能性が非常に高くなります。その結果、接着剤は、上記の物質の侵食に抵抗する能力を持つ必要があり、常に十分な接着剤の強度を維持する必要があります。
プラスチックフィルムコンポジット処理方法は、ドライコンポジット法、ウェットコンポジット法、押し出し複合法、ホットメルト複合法、共排除複合法、その他。
1、乾燥複合
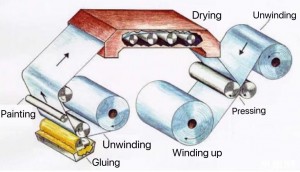
乾燥積層法は、プラスチック包装積層の最も一般的な方法です。特定の温度、張力、速度の下で、最初の基質は、ラミネートマシンのベーキングチャネル(蒸発ゾーン、硬化ゾーン、硬化ゾーン、補償ゾーンの除外)の3つの領域に分割された3つの領域に分割された3つの領域に分割された3つの領域に分割された3つの領域に分割された3つの領域に溶けた状態で、ホットエバポレートとドライズのドライズとドライズのドライズとドライズ、ドライズ、ドライズ、ドライズ、ドライズ、ドライズ、ドライズ、ドライズ、ドライズ、ドライズ、ドライズ、ドライズ、ドライズ、ドライズ、ドライズ、ドライズ、ドライズ、ドライズ、ドライズの層が均一に満たされています。基板(プラスチックフィルム、紙またはアルミホイル)が複合膜に結合しました。
ドライラミネーションは、あらゆる種類のフィルムをラミネートすることができ、目的の要件に応じて高性能包装材料を合成する機能を置き換えることができます。したがって、パッケージングでは、特に毎日の化学物質包装が開発されました。
2、湿った複合
ウェット複合法は、接着剤の層でコーティングされた複合基板(プラスチックフィルム、アルミニウムホイル)であり、接着剤の場合、圧力ローラーおよびその他の材料(紙、セロハン)複合材料を介して乾燥していない場合、オーブンの後に複合膜に乾燥させます。
ウェットコンポジットプロセスはシンプルで、接着性が低く、コストが低く、高効率が高く、残留溶媒を除外します。
ウェットコンポジットラミネートマシンと使用された作動原理と乾燥複合法は基本的に同じです。違いは接着剤でコーティングされた最初の基質であり、最初に2番目の基質ラミネート複合材で、次にオーブンで乾燥させます。シンプルで、粘着性の低い投与量、複合速度、複合製品には、環境に代わる汚染、汚染が含まれていません。
3、押出複利
押し出しの調合は、複合プロセスの最も一般的な方法であり、それは原材料としての熱可塑性樹脂の使用であり、樹脂はフィルムのシート硬化の代わりに死ぬ口によって型に加熱されて溶けます。多層共排除ラミネーションは、押出機の共発現よりも、フィルムへのダイラミネーションに加えて、プラスチック樹脂のさまざまな異なる特性です。
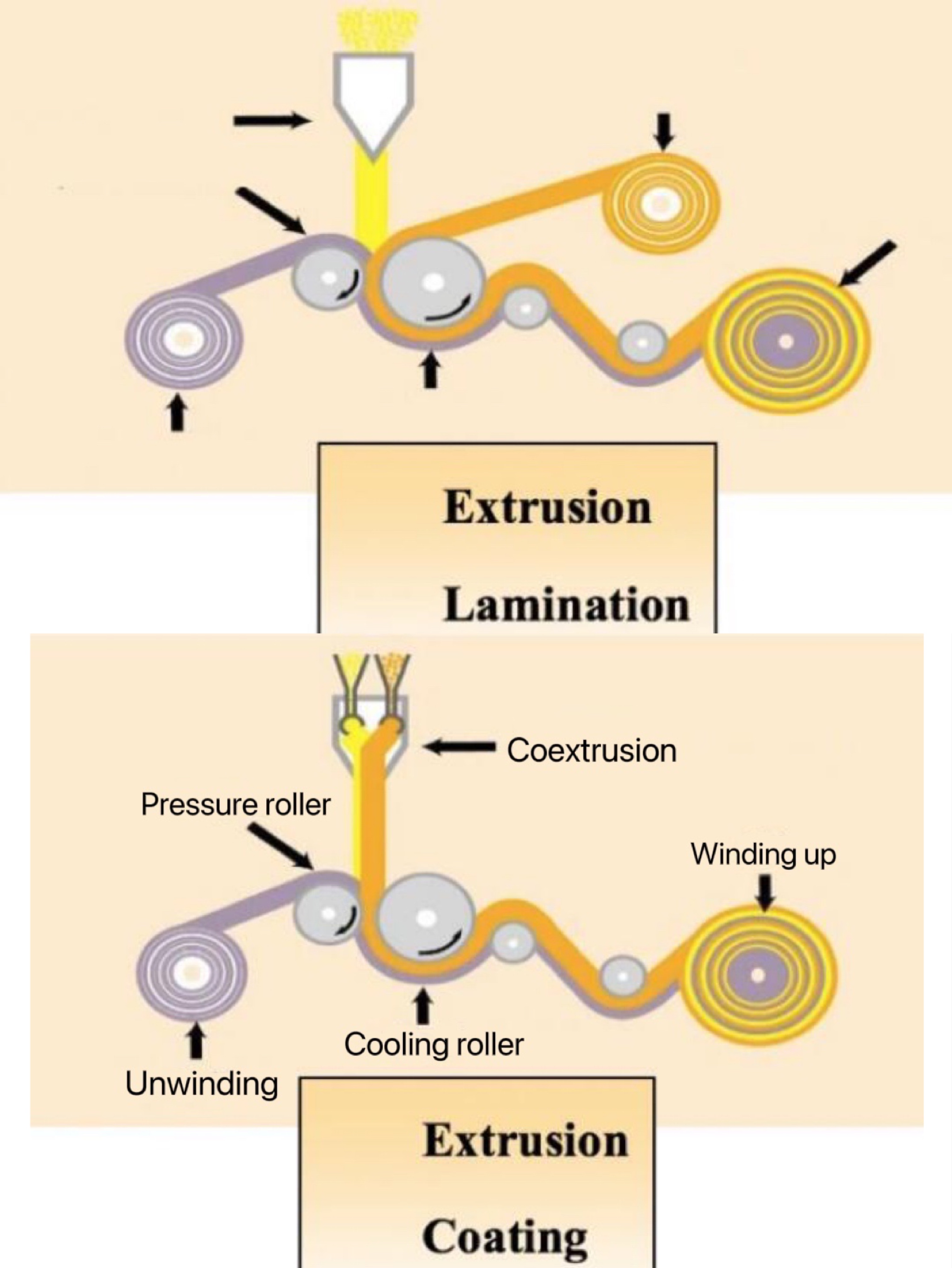
複合材料は、質の高い問題やソリューションが発生しやすいです
配合は、柔軟な包装の生産と処理における重要なプロセスであり、その一般的な障害は、気泡の生産、複合体への低い耐久性、しわに包まれたエッジと巻き上げのエッジの伸びまたは収縮などです。
1、波線現象
この現象の乾燥複合障害では、故障の大部分が占有され、完成品のバッグメイキングの品質に直接影響します。
この失敗の主な理由は次のとおりです。
複合材料の品質が低いまたは印刷基板自体、厚さの偏差、フィルムロールは両端が緩んでおり、片方が不均衡な曲がりくねった張力のために狭くなります。フィルムのボリュームがマシン上の大型の弾力性から分離されている場合、フィルムの上下と左右のプレースメント振幅も比較的大きくなります。これは、材料がホットドラムとホットプレスローラーの間に入ると、ホットプレスローラーで水平になることができないため、平らに絞ることができないため、完成したコンポジットラインにつながり、斜めのラインになります。複合材料がPEまたはCPPの場合、厚さ偏差が10μmを超える場合、しわもしやすく、現時点では複合材料の張力を適切に増やすことができ、ホットプレスローラーは押し出しのための水平状態になります。ただし、緊張が適切であるべきであることに注意する必要があります。張力が多すぎると、複合材料を伸ばすのは簡単で、バッグの口が内側に傾いています。複合材料の厚さの偏差が大きすぎる場合、実際には使用できません。対処する必要があります。
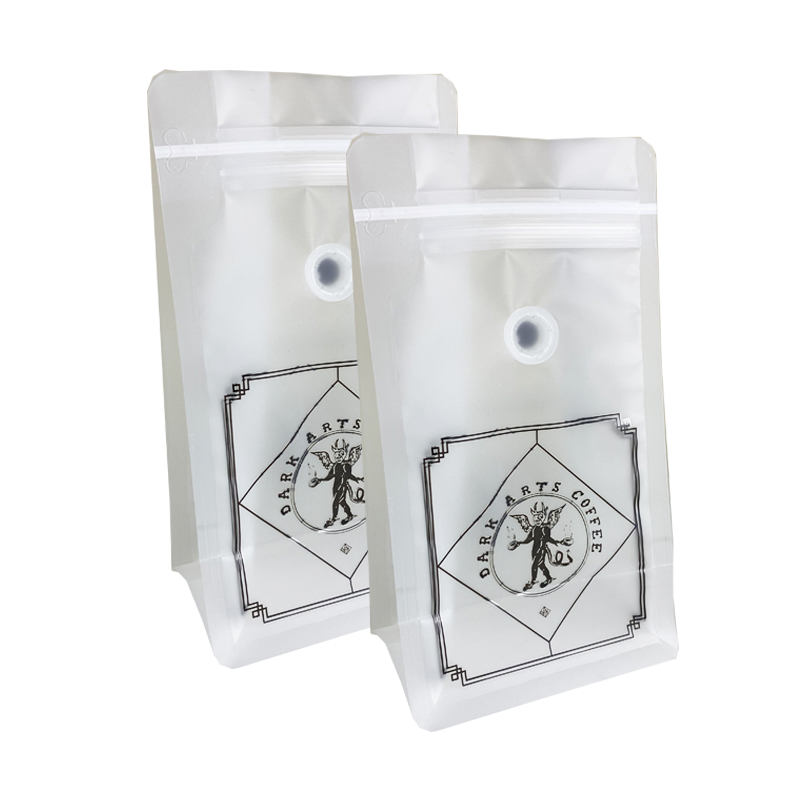
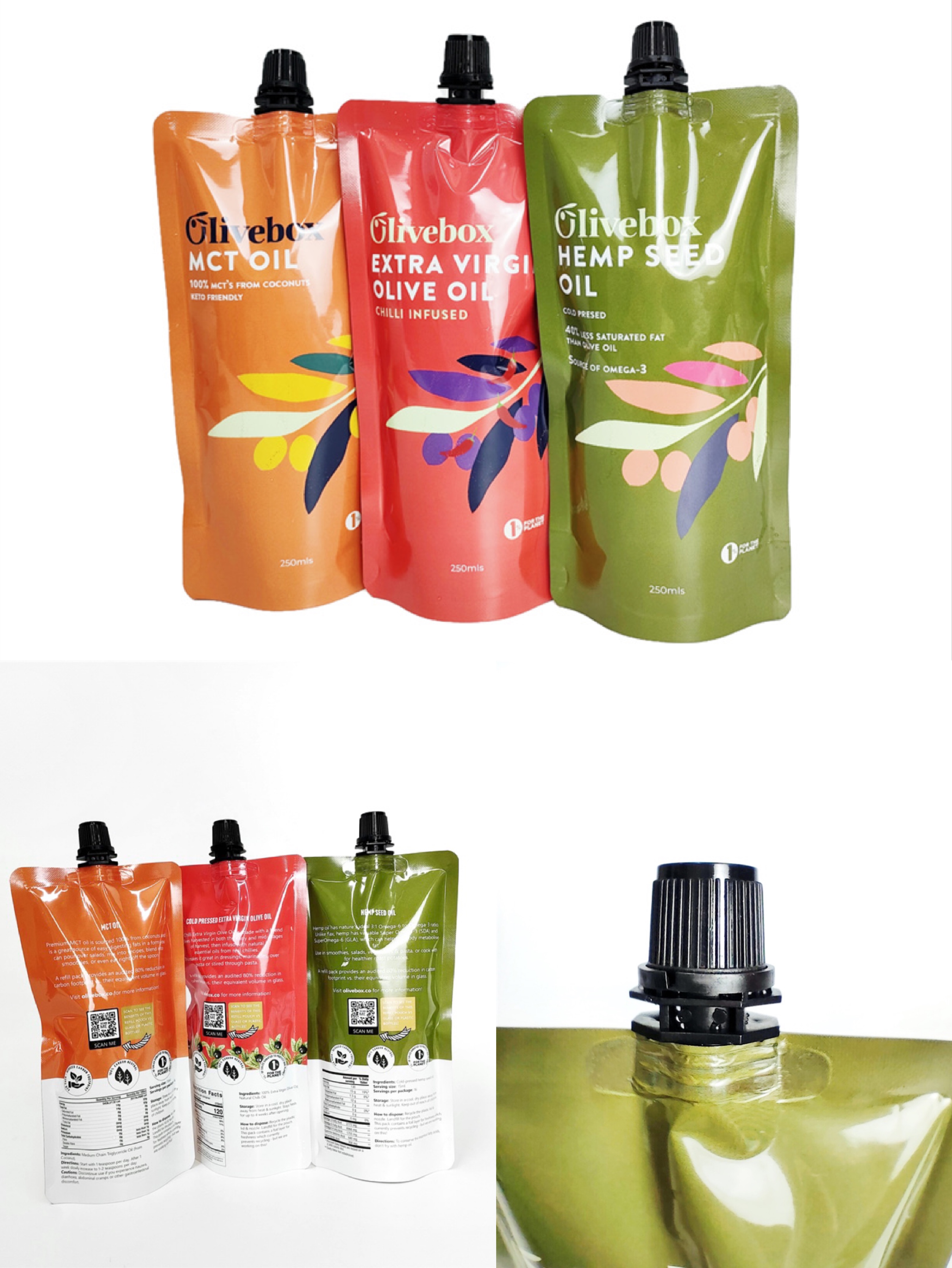
2、複合ホワイトスポット
インクのカバレッジ率が低い結果、白い斑点:複合白インクの場合、インクの吸収揮発は、白い斑点によって引き起こされる揮発ではなく、メソッドの乾燥能力を改善するために利用可能な場合。まだ白い斑点がある場合、一般的な解決策は、優れたインクカバレッジ速度の粉砕の細かさが強いため、白インクの細かさをチェックするなど、白いインクのカバレッジを改善することです。
不均一に生成された白い斑点の代わりに接着剤:接着剤でコーティングされたインク層では、インクに入るために溶媒、表面張力、および基質よりも小さいインク層では、レベリングは、接着剤、接着剤、アルミニウム沈着の表面またはアルミニウムの箔でコーティングされた照明フィルムほど良くありません。白い斑点の形成。この溶液を使用して、均一なゴムローラーでコーティングを滑らかにするか、交換量を増やすことができます。
3、複合バブル
複合バブルは、次の状況と対応する方法で生成されます。
現象の複合気泡
1. 悪いフィルムは、接着剤の濃度と交換の量を改善するはずです。MST、KPT表面は濡れが容易ではなく、特に冬には泡を簡単に生成できます。インクの空気の泡、できる接着剤の量を増やす方法を使用して除去します。
2、インク表面の隆起と泡は、温度を複合し、増加するための圧縮圧力を複合したものでなければなりません。
3、インクの表面に接着剤を追加する量は低く、配合ローラーの圧力ペースト時間と滑らかなローラーの使用が増加するはずです。フィルム予熱して、調合速度を低下させるのに十分なフィルムを予熱し、適切な湿潤接着剤を選択し、インクの正しい選択を選択します。
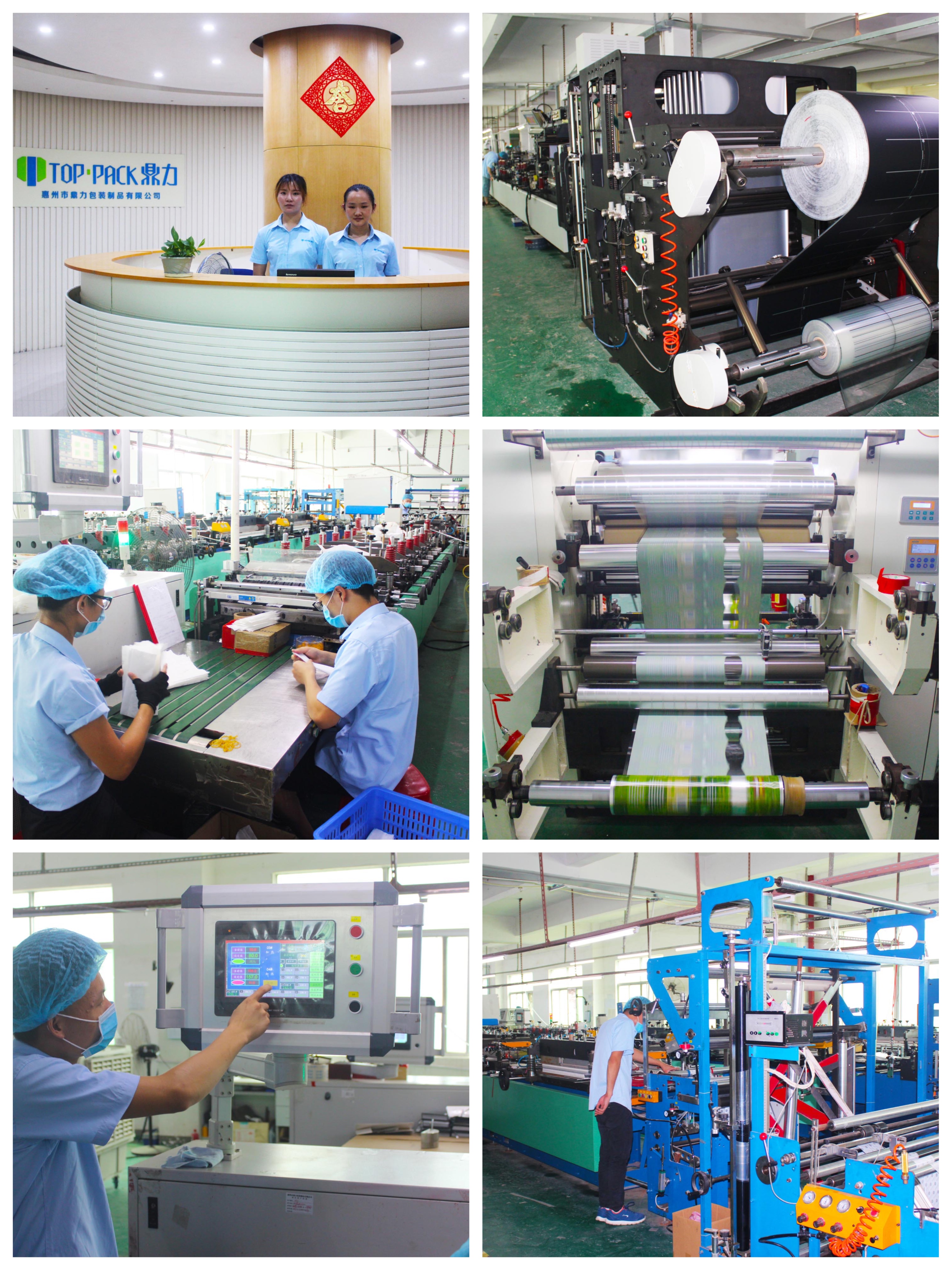
4.フィルムの添加物(潤滑剤、抗抗剤)は接着剤によって浸透しているため、高分子量と速い硬化で接着剤を選択し、接着剤の濃度を上げ、接着剤を完全に乾燥させ、3か月以上の配置期間でフィルムを使用しないようにする必要があります。
5、冬の温度は低く、フィルムとインクの移動へのジョイント、リセットアライメント効果は良くないため、操作場所は一定の温度を保ちます。
6、乾燥温度が高すぎるため、接着剤の膨張または表面皮膚の皮が発生し、内側が乾燥していないため、接着剤の乾燥温度を調整する必要があります。
7.コンポジットローラーフィルムの間に空気が同行され、複合ローラーの温度を上げ、複合角を分解する必要があります(フィルムは厚く、硬いときに泡を簡単に生成できます)。
8、フィルムの障壁が高いため、泡に印刷されていない複合フィルムに残っている接着剤硬化によって生成されるCO2ガスは、硬化剤の量を改善して、乾燥した接着剤硬化を改善するはずです。
9.ゴムのグリコール酸は、インクフィラーに適した溶媒であり、ゴムはインクを溶解し、インクに泡のみがあり、ゴムへの水の浸透を避け、ゴムの乾燥温度を改善してインクの溶解を減らします。
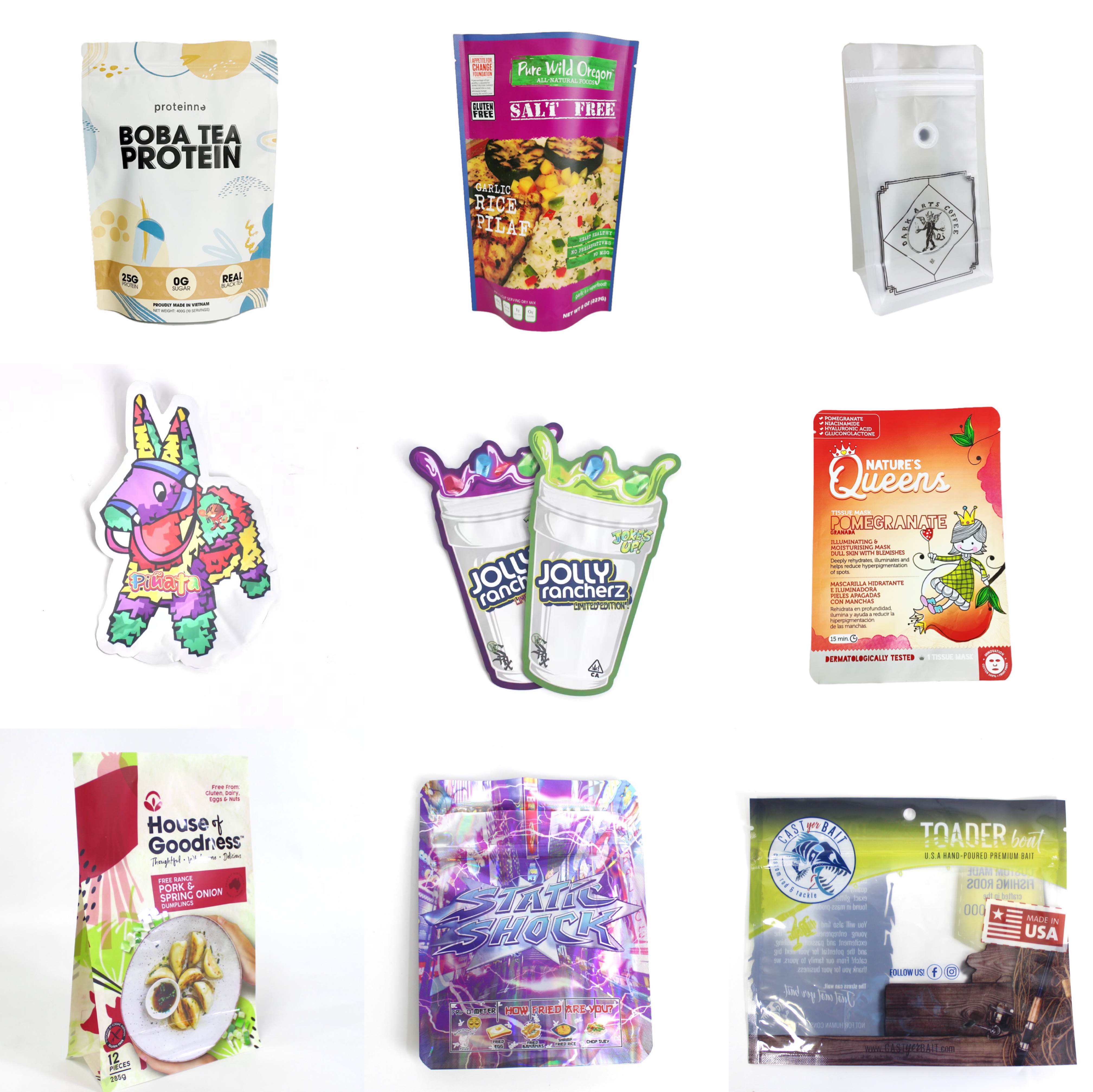
4、皮の強度が悪い
皮の強度は貧弱で、硬化が不完全であるか、接着剤の量が少なすぎるか、使用されたインクと接着剤が状況と一致しませんが、硬化は完了していますが、長さの欠如による複合フィルムの2つの層の間で、力の減少が減少しています。
接着剤の注入量は小さすぎ、接着剤の比率が低下し、貯蔵で接着剤が劣化し、接着剤で水とアルコールが混合され、フィルムの補助剤が沈殿し、乾燥または成熟プロセスは沈着しません。
接着剤の適切な貯蔵に注意してください。最長は1年以内です(スズは密封できます)。接着剤、アルコールなど、接着剤、アルコールなどに異質な物質が入るのを防ぎます。接着剤コーティングの量を改善するのに適したフィルム。乾燥温度の空気体積を改善し、複利の速度を減らします。表面張力を改善するためのフィルム表面の2番目の処理。フィルム調合表面での添加物の使用を減らします。これらすべての方法は、複合材料の剥離強度の貧弱な問題を改善するのに役立ちます。
5。シールは悪い
コンパウンドバッグヒートシールの悪いパフォーマンスとその原因は、基本的に次の状況です。
熱シーリング強度は貧弱です。現象の主な理由は完全に硬化していないか、熱の密閉温度が低すぎることです。硬化プロセスを最適化するか、シーリングナイフの温度を適切に増加させると、問題が改善されます。
ヒートシールカバーの剥離と屈折率。この現象の主な原因は、結合が治癒しないことです。硬化時間を調整するか、硬化エージェントのコンテンツを調整すると、この問題を改善できます。
不十分な開放性 /内層フィルムのオープン性が悪い。この現象の原因は、オープニングエージェントが少なすぎるため、材料(修飾子)が多すぎて粘着性または脂っこいフィルム表面になります。この問題は、オープニングエージェントの量を増やし、修飾子の量を調整し、フィルム表面での二次汚染を回避することで改善できます。
終わり
あなたの読書をありがとう、私たちはあなたのパートナーになる機会があることを願っています。
質問がある場合は、お問い合わせください。お気軽にお知らせください。お知らせください。
接触:
電子メールアドレス :fannie@toppackhk.com
WhatsApp:0086 134 10678885
投稿時間:4月1日 - 2022年