ຂະບວນການກະກຽມຂັ້ນພື້ນຖານຂອງຖົງການຫຸ້ມຫໍ່ປະສົມໄດ້ຖືກແບ່ງອອກເປັນສີ່ຂັ້ນຕອນ: ການພິມ, ການເຮັດວຽກ, ເຊິ່ງສອງຂະບວນການຂອງການເຮັດແລະກະເປົາສໍາຄັນທີ່ສົ່ງຜົນກະທົບຕໍ່ຜົນງານສຸດທ້າຍຂອງຜະລິດຕະພັນສຸດທ້າຍ.
ຂະບວນການປະສົມ
ຂະບວນການຫຸ້ມຫໍ່ຜະລິດຕະພັນອອກແບບ, ນອກເຫນືອໄປຈາກການເລືອກຊັ້ນໃຕ້ດິນທີ່ຖືກຕ້ອງ, ການເລືອກກາວທີ່ສໍາຄັນ, ອີງໃສ່ການນໍາໃຊ້ຜະລິດຕະພັນ, ເງື່ອນໄຂ, ຄວາມຕ້ອງການດ້ານຄຸນນະພາບສໍາລັບການຄັດເລືອກທີ່ມີຄຸນນະພາບ. ເລືອກກາວທີ່ບໍ່ຖືກຕ້ອງ, ບໍ່ວ່າເຕັກໂນໂລຍີປະມວນຜົນທີ່ສົມບູນແບບ, ພ້ອມທັງການປຸງແຕ່ງທີ່ບໍ່ດີເພື່ອຫຼຸດຜ່ອນແຮງ, ການຮົ່ວໄຫຼ, ກະເປົາທີ່ແຕກຫັກແລະຄວາມລົ້ມເຫລວອື່ນໆ.
ການເລືອກຂອງການຫຸ້ມຫໍ່ທີ່ມີຄວາມຍືດຫຍຸ່ນໃນປະຈໍາວັນພ້ອມກັບກາວທີ່ຈະພິຈາລະນາປັດໃຈທີ່ຫຼາກຫຼາຍ, ໂດຍທົ່ວໄປ, ເປັນກາວປະກອບແລ້ວຈະຕອບສະຫນອງເງື່ອນໄຂດັ່ງຕໍ່ໄປນີ້:
ບໍ່ແມ່ນສານພິດ
ບໍ່ມີສານສະກັດຈາກທີ່ເປັນອັນຕະລາຍປະກົດຕົວຫຼັງຈາກທາດແຫຼວທີ່ຫຸ້ມຫໍ່.
ໃຊ້ໄດ້ກັບຄວາມຮຽກຮ້ອງຕ້ອງການອຸນຫະພູມຂອງການເກັບຮັກສາອາຫານ.
ສະພາບອາກາດທີ່ດີ, ບໍ່ມີສີເຫຼືອງແລະໂພງ, ບໍ່ມີການຂຸດຄົ້ນແລະການຊັກຊ້າ.
ການຕໍ່ຕ້ານກັບນໍ້າມັນ, ລົດຊາດ, ລົດຊາດ, ເສັ້ນລ້ອນແລະເຫຼົ້າ.
ບໍ່ມີການເຊາະເຈື່ອນຂອງຫມຶກຮູບແບບການພິມ, ຄາດວ່າຈະມີຄວາມເປັນເອກະພາບສູງສໍາລັບຫມຶກ.
ນອກຈາກນັ້ນ, ການຕໍ່ຕ້ານກັບການເຊາະເຈື່ອນ, ເນື້ອຫາມີບັນຈຸເຄື່ອງເທດ, ນ້ໍາມັນແຕກຕ່າງກັນ, ມັນກໍ່ໃຫ້ເກີດຄວາມເສຍຫາຍດ້ານໃນ, ດ້ວຍເຫດນັ້ນ, ກາວຈໍາເປັນຕ້ອງມີຄວາມສາມາດທີ່ຈະຕ້ານທານກັບການເຊາະເຈື່ອນຂອງສານຂ້າງເທິງ, ສະເຫມີຮັກສາຄວາມເຂັ້ມແຂງຂອງ Peel ທີ່ພຽງພໍ.
ວິທີການປຸງແຕ່ງຮູບເງົາແບບພລາສຕິກແມ່ນວິທີການປະສົມທີ່ຊຸ່ມ, ວິທີການທີ່ຊຸ່ມ.
1, ການປະສົມແຫ້ງ
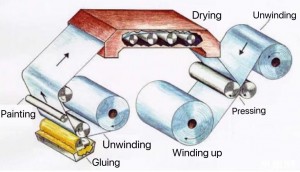
ວິທີການທີ່ມີນ້ໍາທີ່ແຫ້ງແມ່ນວິທີການທົ່ວໄປທີ່ສຸດຂອງການຫຸ້ມຫໍ່ຖົງຢາງ. ພາຍໃຕ້ເງື່ອນໄຂທີ່ແນ່ນອນຂອງອຸນຫະພູມ, ຄວາມໄວ, ເຂດທີ່ມີຄວາມປະທັບໃຈກັບສາມເຂດ State State Hot ແລະ substrate ອັນທີສອງ (ຮູບເງົາພາດສະຕິກ, ເຈ້ຍຫຼືອາລູມີນຽມ foil) ຜູກພັນກັບຮູບເງົາທີ່ມີຮູບເງົາ.
ການຫລູຫລາແຫ້ງສາມາດລອກຮູບເງົາໄດ້, ແລະສາມາດທົດແທນຄວາມສາມາດໃນການສັງເຄາະເອກະສານຫຸ້ມຫໍ່ທີ່ມີປະສິດຕິພາບສູງຕາມຄວາມຕ້ອງການຈຸດປະສົງອີງຕາມເນື້ອໃນ. ເພາະສະນັ້ນ, ໃນການຫຸ້ມຫໍ່, ໂດຍສະເພາະໃນການຫຸ້ມຫໍ່ສານເຄມີປະຈໍາວັນໄດ້ຖືກແກ້ໄຂການພັດທະນາແລ້ວ.
2,ການປະສົມທີ່ຊຸ່ມ
ວິທີການຂອງ Commitite ປຽກແມ່ນຊັ້ນປະກອບທີ່ປະກອບດ້ວຍຊັ້ນປະສົມ (ຮູບເງົາອາລູມິນຽມ) ເຄືອບ, ໂດຍຜ່ານການລີດ, ແລະຫຼັງຈາກນັ້ນຕາກແດດໃຫ້ແຫ້ງ.
ຂະບວນການຂອງອົງປະດາຊຸ່ມແມ່ນງ່າຍດາຍ, ມີໃບປະດັບປະດາຫນ້ອຍ, ມີປະສິດຕິພາບສູງ, ແລະຍົກເວັ້ນສານລະລາຍທີ່ເຫລືອຢູ່.
ເຄື່ອງຊັກຜ້າປຽກຊຸ່ມແລະວິທີການທີ່ໃຊ້ແລ້ວແລະຫຼັກສູດທີ່ໃຊ້ແລ້ວແມ່ນພື້ນຖານທີ່ເຄືອບ, ທໍາອິດດ້ວຍໃບປະສົມ laminate ທີສອງ, ແລະແຫ້ງໂດຍເຕົາອົບ. ປະລິມານທີ່ລຽບງ່າຍ, ຫນຽວຫນ້ອຍ, ຄວາມໄວປະສົມ, ຜະລິດຕະພັນປະສົມບໍ່ມີສານລະລາຍທີ່ຍັງເຫຼືອບໍ່ມີທາງເລືອກທີ່ຍັງເຫຼືອ, ເປັນທາງເລືອກມົນທົນຕໍ່ສິ່ງແວດລ້ອມ.
3, ສະກັດກັ້ນການປະສົມ
ການປະສົມປະສານທີ່ບໍ່ມີປະໂຫຍດຫຼາຍທີ່ສຸດຂອງຂະບວນການປະສົມ, ມັນແມ່ນການນໍາໃຊ້ນ້ໍາຢາງ, ທັນທີ ການຄອບງໍາແບບສະແດງຄວາມຫລາກຫລາຍແມ່ນຫຼາກຫຼາຍຂອງຄຸນລັກສະນະທີ່ແຕກຕ່າງກັນຂອງຢາງພລາສຕິກໂດຍຜ່ານການສະແດງນ້ໍາຢາງທີ່ມີຄວາມຕື່ນເຕັ້ນ, ເຂົ້າໄປໃນບ່ອນຫຼົບຫນີທີ່ມີຄວາມເສຍຫາຍເຂົ້າໄປໃນຮູບເງົາ.
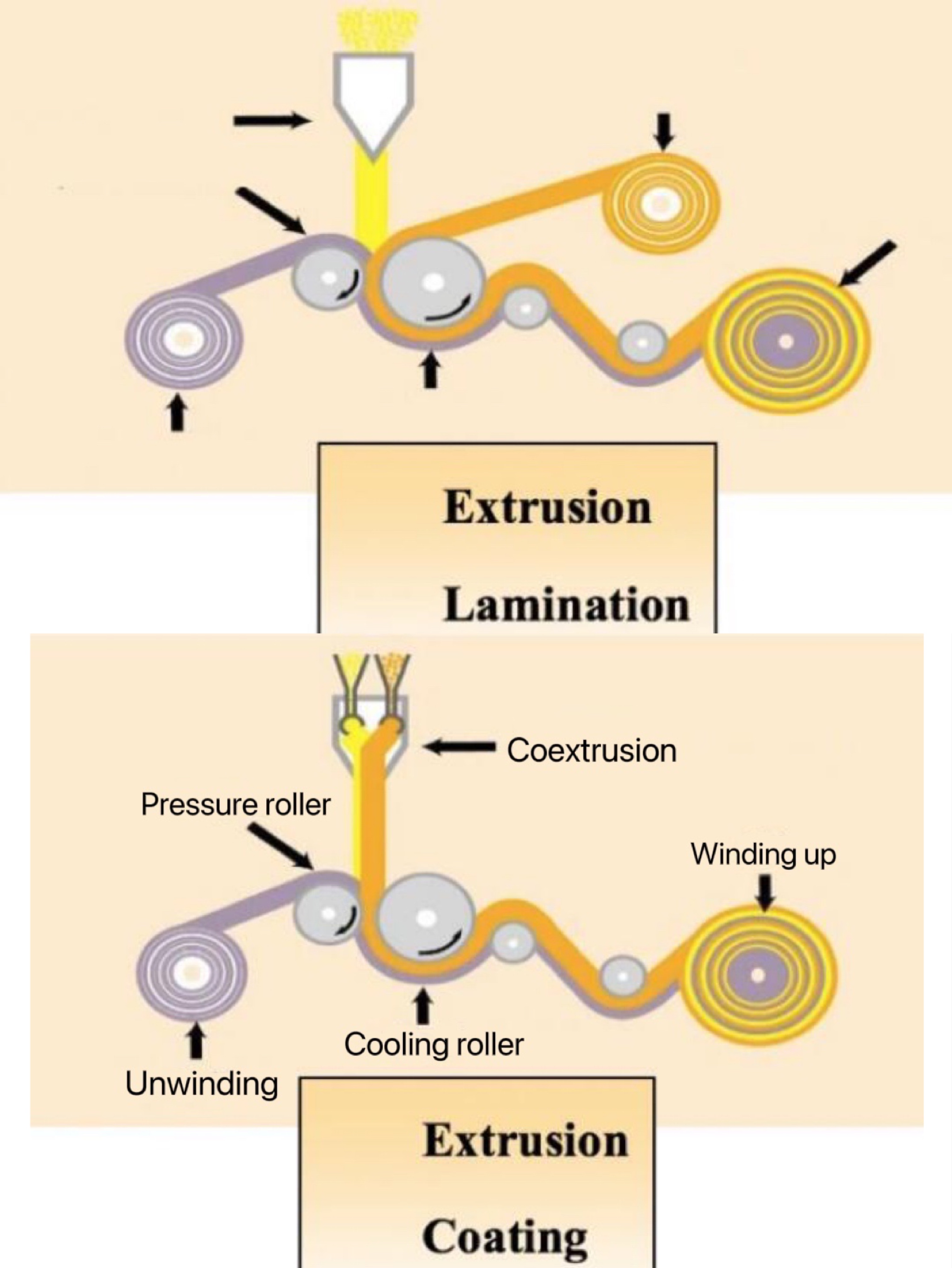
ວັດສະດຸປະສົມແມ່ນມັກຈະມີບັນຫາແລະວິທີແກ້ໄຂທີ່ມີຄຸນນະພາບ
ການປະສົມແມ່ນຂະບວນການທີ່ສໍາຄັນໃນການຜະລິດແລະການປຸງແຕ່ງຟອງທີ່ມີຄວາມຍືດຍຸ່ນ, ສ່ວນຜະລິດຕະພັນ, ສ່ວນປະສົມຂອງຄວາມຫຍຸ້ງຍາກໃນການວິເຄາະຂອງສາເຫດແລະວິທີການລົບລ້າງ.
1, ປະກົດການ wrinkle
ໃນຄວາມລົ້ມເຫຼວຂອງປະກອບທີ່ແຫ້ງຂອງປະກົດການນີ້ຍຶດເອົາອັດຕາສ່ວນໃຫຍ່ຂອງຄວາມລົ້ມເຫຼວໂດຍກົງສົ່ງຜົນກະທົບຕໍ່ຄຸນນະພາບຂອງຜະລິດຕະພັນສໍາເລັດຮູບ.
ເຫດຜົນຕົ້ນຕໍຂອງຄວາມລົ້ມເຫຼວນີ້ແມ່ນດັ່ງຕໍ່ໄປນີ້.
ຄຸນນະພາບທີ່ບໍ່ດີຂອງວັດສະດຸຫຼື substrate ການພິມຕົວມັນເອງ, deviation ໃນຄວາມຫນາ, ມ້ວນຮູບເງົາແມ່ນວ່າງຢູ່ທັງສອງສົ້ນແລະແຫນ້ນໃນຄວາມເຄັ່ງຕຶງທີ່ບໍ່ສົມດຸນ. ຖ້າປະລິມານຮູບເງົາຖືກແຍກອອກຈາກຄວາມຍືດຍຸ່ນຂອງໂຕໃຫຍ່, ໃນເຄື່ອງຈັກ, ມັນບໍ່ສາມາດບີບອັດໄດ້, ເຊິ່ງມັນບໍ່ສາມາດບີບອັດໄດ້, ເຊິ່ງມັນບໍ່ສາມາດບີບອັດໄດ້, ເຊິ່ງມັນຈະບໍ່ສາມາດບີບຕົວໄດ້, ເຊິ່ງມັນຈະບໍ່ສາມາດບີບຕົວໄດ້, ເຊິ່ງມັນຈະບໍ່ສາມາດບີບອັດໄດ້, ເຊິ່ງມັນຈະບໍ່ສາມາດບີບອັດປາກ, ເສັ້ນລວດລາຍ, ເສັ້ນລວດລາຍ, ເຊິ່ງເປັນຜົນກະທົບຂອງຜະລິດຕະພັນ. ໃນເວລາທີ່ວັດສະດຸປະກອບແມ່ນ PE ຫຼື CPP, ຖ້າມີຄວາມຫນາແຫນ້ນຫຼາຍກ່ວາ20μm, ໃນເວລານີ້, ແລະເຄື່ອງກົດທີ່ກົດຮ້ອນສາມາດກາຍເປັນສະພາບທີ່ນອນຢູ່ໃນແນວນອນສໍາລັບ Extrusion. ເຖິງຢ່າງໃດກໍ່ຕາມ, ມັນຄວນຈະໄດ້ຮັບຍົກໃຫ້ເຫັນວ່າຄວາມກົດດັນຄວນເຫມາະສົມ, ຄວາມເຄັ່ງຕຶງຫຼາຍເກີນໄປຈະເຮັດໃຫ້ວັດສະດຸປະກອບຍາວ, ສົ່ງຜົນໃຫ້ປາກພາຍໃນ. ຖ້າຄວາມບ່ຽງເບນຄວາມຫນາຂອງວັດສະດຸອົງປະກອບແມ່ນໃຫຍ່ເກີນໄປ, ມັນກໍ່ບໍ່ສາມາດໃຊ້ໄດ້, ຄວນຈະຖືກຈັດການກັບ.
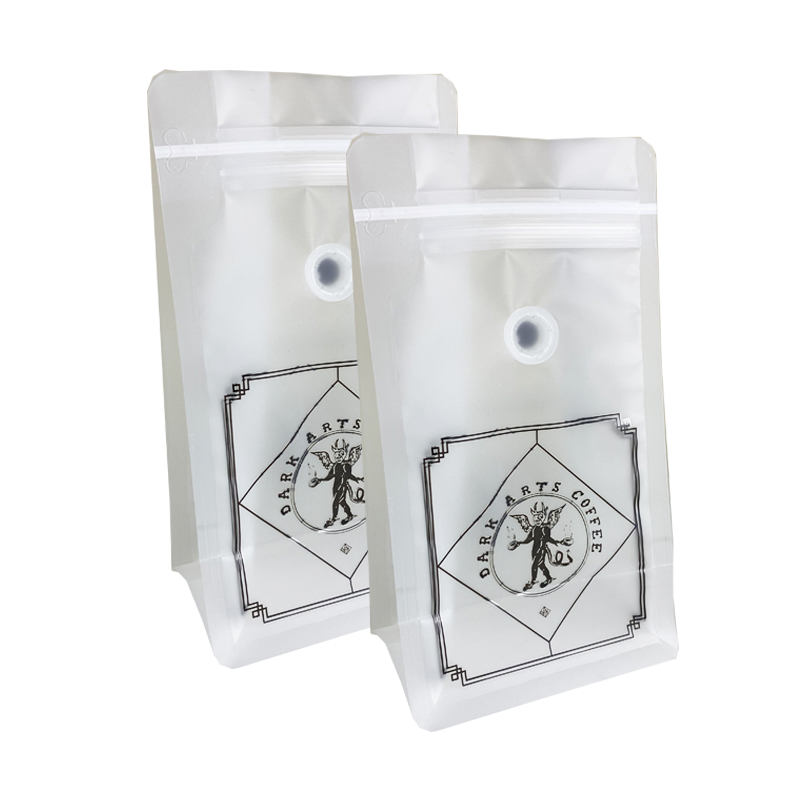
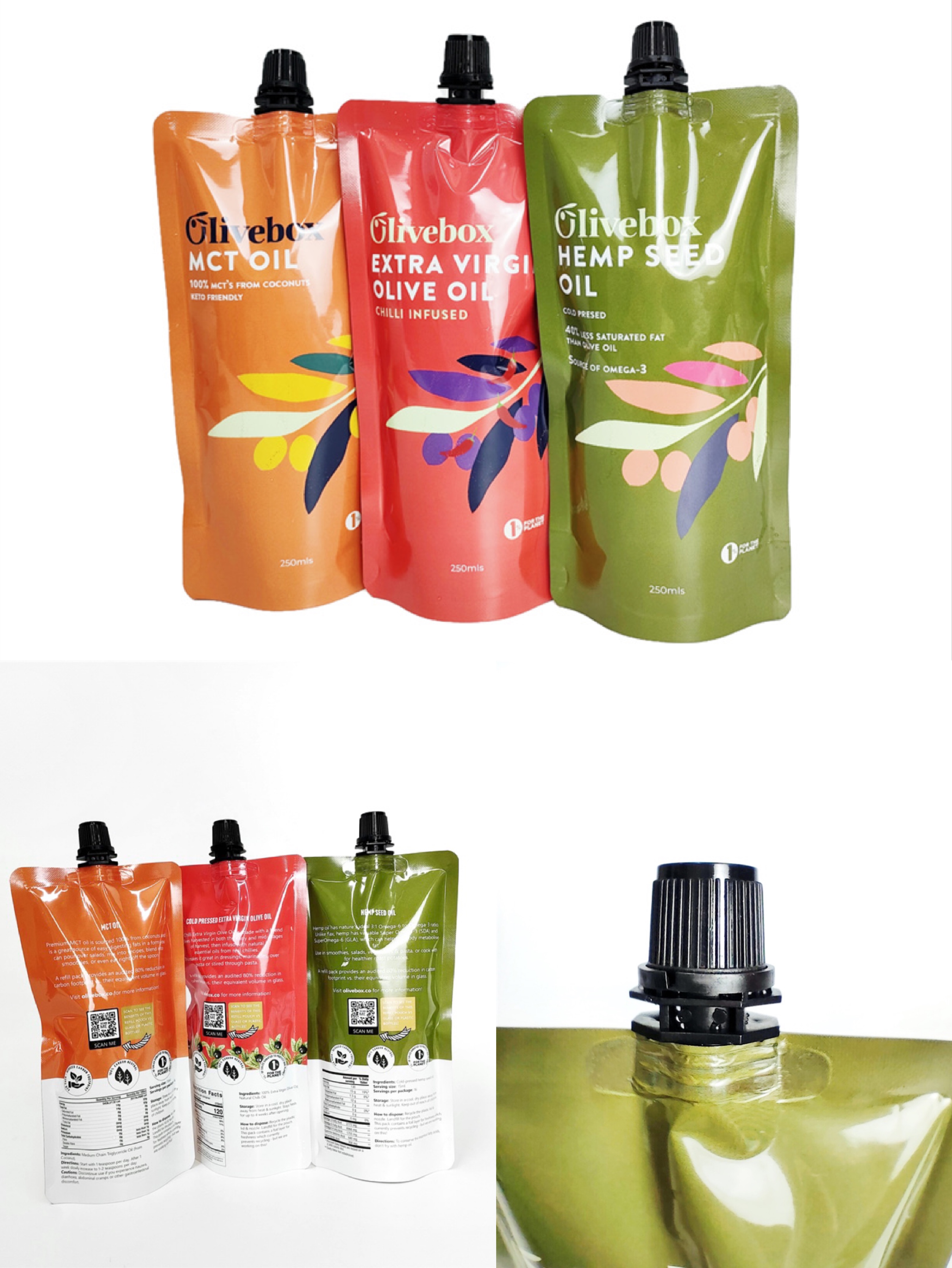
2, ປະສົມຈຸດສີຂາວ
ເປັນຜົນມາຈາກອັດຕາການຄຸ້ມຄອງຫມຶກທີ່ບໍ່ດີສີຂາວ: ສໍາລັບດັດແກ້ສີຂາວ, ໃນເວລາທີ່ບໍ່ໄດ້ຮັບການຍົກຍ້ອງຂອງຫມຶກແຕ່ວ່າມີໃຫ້ປັບປຸງຄວາມສາມາດໃນການແຫ້ງຂອງວິທີການແຫ້ງ; ຖ້າຍັງມີຈຸດດ່າງດໍາ, ການແກ້ໄຂທົ່ວໄປແມ່ນເພື່ອປັບປຸງການຄຸ້ມຄອງຫມຶກຂາວເຊັ່ນ: ການກວດສອບທີ່ດີຂອງຫມຶກສີຂາວ, ເພາະວ່າອັດຕາການຄ້ໍາປະກັນທີ່ດີ.
ກາວທີ່ຜະລິດອອກມາຢ່າງບໍ່ເທົ່າທຽມກັນ ຂອງຈຸດສີຂາວ. ການແກ້ໄຂສາມາດໃຊ້ເພື່ອເຮັດໃຫ້ມີການເຄືອບດ້ວຍຢາງທີ່ເປັນເອກະພາບ, ຫຼືເພີ່ມຈໍານວນເງິນທົດແທນ.
3, ຟອງປະສົມກັນ
ຟອງປະສົມແມ່ນສ້າງຂື້ນໃນສະຖານະການຕໍ່ໄປນີ້ແລະວິທີການທີ່ສອດຄ້ອງກັນ.
ຟອງປະສົມໃນປະກົດການດັ່ງກ່າວ
1. ຮູບເງົາທີ່ບໍ່ດີ, ຄວນປັບປຸງຄວາມເຂັ້ມຂົ້ນຂອງກາວແລະຈໍານວນເງິນ, MTT, Surface ບໍ່ແມ່ນເລື່ອງງ່າຍທີ່ຈະຊຸ່ມ, ໂດຍສະເພາະໃນລະດູຫນາວ. ຟອງອາກາດຢູ່ເທິງຫມຶກ,ໄດ້ໃຊ້ວິທີການທີ່ຈະເພີ່ມປະລິມານຂອງກາວທີ່ຈະເອົາອອກ.
2,ພື້ນຜິວຂອງຫມຶກແລະຟອງ, ຄວນຈະເປັນຮູບເງົາທີ່ປະສົມກົມກຽວອຸນຫະພູມແລະຄວາມກົດດັນຂອງການປະສົມທີ່ຈະເພີ່ມຂື້ນ.
3, ຈໍານວນເງິນຂອງການເພີ່ມກາວຢູ່ດ້ານຂອງຫມຶກແມ່ນຕ່ໍາ, ຄວນຈະເພີ່ມເວລາຂອງ roller ທີ່ສົມບູນແລະການໃຊ້ຄວາມໄວທີ່ສົມບູນເພື່ອຫຼຸດກາວທີ່ປຽກແລະເລືອກທີ່ຖືກຕ້ອງຂອງຫມຶກ.
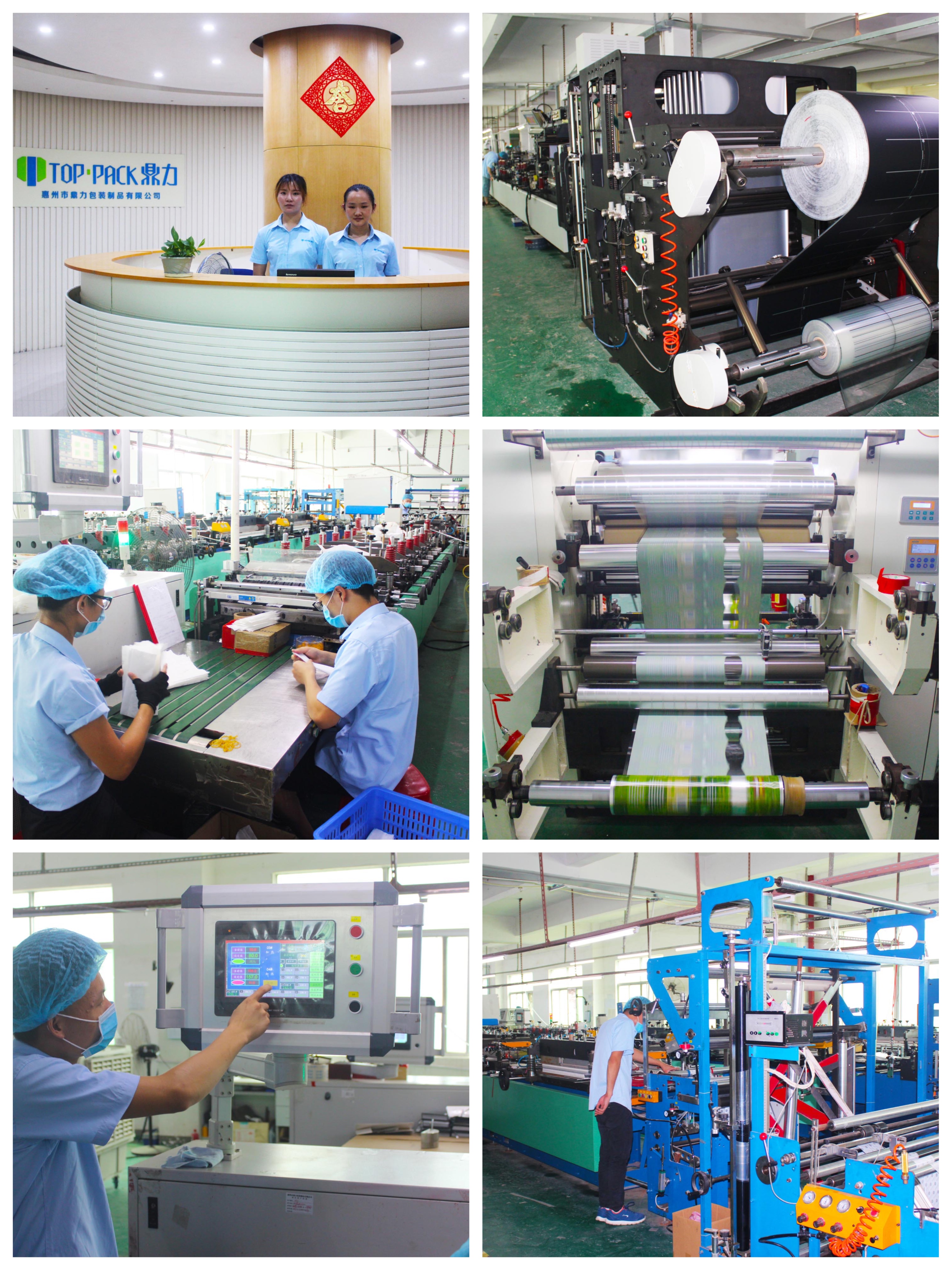
4. ສິ່ງເສບຕິດ (ທາດນ້ໍາມັນຫລໍ່ລື່ນ, ຕົວແທນ Antisticatic)
5,ອຸນຫະພູມໃນລະດູຫນາວແມ່ນຕໍ່າ, ການຮ່ວມມືກັບຮູບເງົາແລະການໂອນເງິນ, ໃຫ້ຄືນໃຫມ່ຜົນກະທົບບໍ່ດີ, ສະນັ້ນສະຖານທີ່ສັກສິດຮັກສາອຸນຫະພູມຢູ່.
6,ອຸນຫະພູມທີ່ແຫ້ງແລ້ງສູງເກີນໄປ, ຄວາມຫນາແຫນ້ນຂອງກາວຫລືເນື້ອເຍື່ອຂອງຜິວຫນັງທີ່ເກີດຂື້ນ, ແລະພາຍໃນກໍ່ບໍ່ແຫ້ງ, ສະນັ້ນອຸນຫະພູມແຫ້ງຂອງກາວຄວນປັບ.
7. .
8,ເນື່ອງຈາກວ່າສິ່ງກີດຂວາງຮູບເງົາສູງ, ນ້ໍາມັນ CO2 ທີ່ຜະລິດໂດຍກາວ, ບໍ່ໄດ້ພິມຈໍານວນຕົວແທນຮັກສາ, ເພື່ອໃຫ້ມີການຮັກສາທີ່ຫນຽວໃນເວລາແຫ້ງ.
9. ອາຊິດ glycolic ໃນຢາງແມ່ນສານເຕີມນ້ໍາໂນ, ຢາງຈະລະລາຍເຈາະນ້ໍາແລະປັບປຸງອຸນຫະພູມແຫ້ງຂອງຢາງເພື່ອຫຼຸດຜ່ອນການລະລາຍຂອງຫມຶກ.
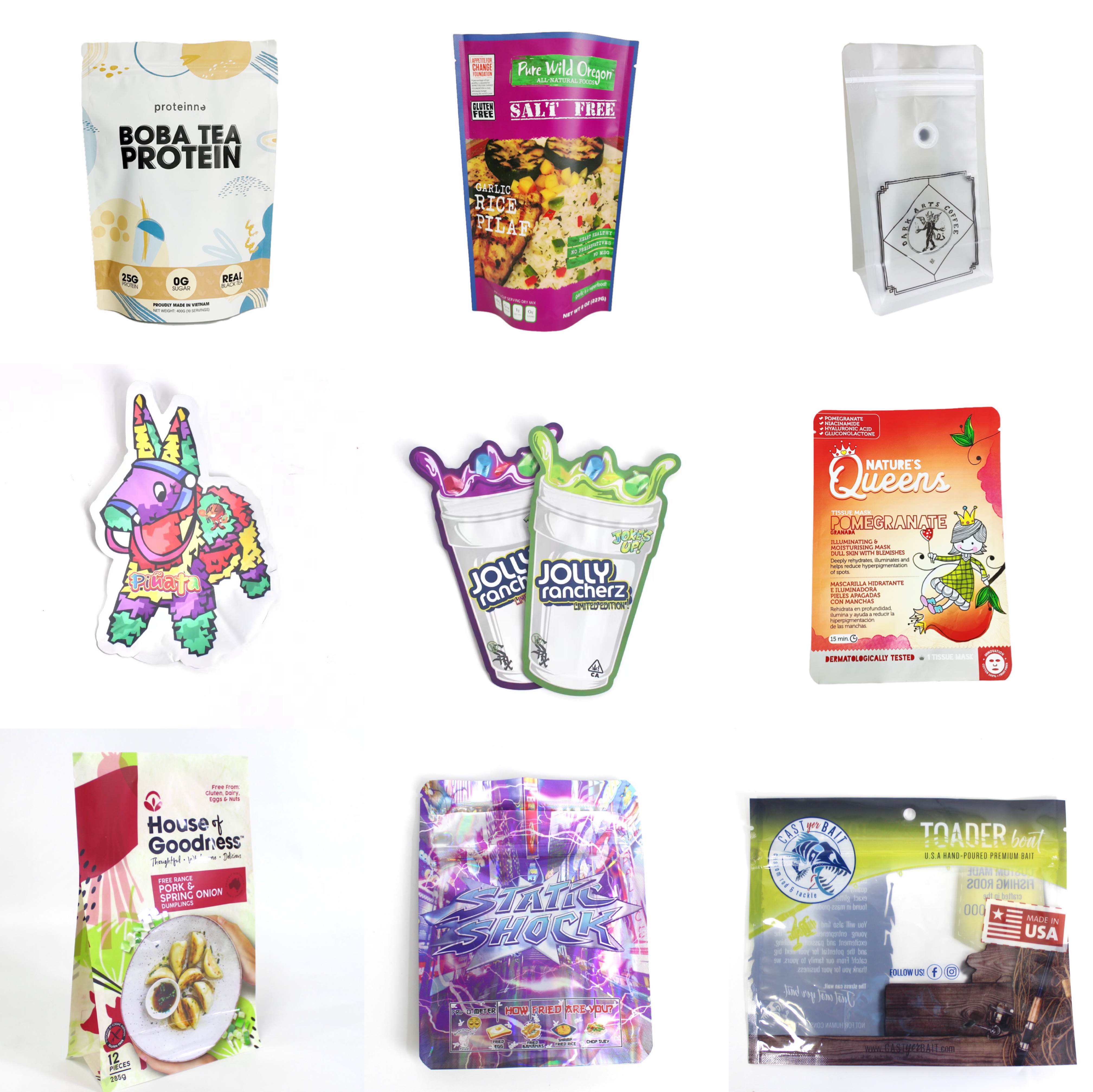
4, peel ທີ່ບໍ່ດີກໍາລັງແຮງ
ຄວາມເຂັ້ມແຂງຂອງ Peel ແມ່ນຄົນທຸກຍາກ, ແມ່ນຍ້ອນການຮັກສາທີ່ບໍ່ຄົບຖ້ວນ, ຫຼືຈໍານວນກາວບໍ່ກົງກັນ, ແຕ່ວ່າລະຫວ່າງສອງຊັ້ນຂອງຮູບເງົາສ່ວນປະສົມເນື່ອງຈາກການຂາດຄວາມຍາວໄດ້ຫຼຸດຜ່ອນຜົນບັງຄັບໃຊ້ຫຼຸດລົງ.
ປະລິມານຂອງກາວສັກມີຂະຫນາດນ້ອຍເກີນໄປ, ອັດຕາສ່ວນຂອງກາວແມ່ນຖືກຕັດອອກໃນຮູບເງົາ, ເວລາແຫ້ງແລະອື່ນໆ, ເຊິ່ງຈະເຮັດໃຫ້ປັດໃຈການຫຼຸດຜ່ອນການຫຼຸດຜ່ອນຄວາມເຂັ້ມແຂງຂອງ Peel ປະສົມສຸດທ້າຍ.
ເອົາໃຈໃສ່ກັບການເກັບກາວທີ່ເຫມາະສົມ, ຍາວທີ່ສຸດແມ່ນບໍ່ເກີນ 1 ປີ (ກົ່ວສາມາດປະທັບຕາ); ປ້ອງກັນບໍ່ໃຫ້ສານຕ່າງປະເທດເຂົ້າໄປໃນກາວ, ໂດຍສະເພາະນ້ໍາ, ເຫຼົ້າ, ແລະອື່ນໆ, ເຊິ່ງສາມາດເຮັດໃຫ້ເກີດຄວາມລົ້ມເຫຼວຂອງກາວ. ຮູບເງົາທີ່ເຫມາະສົມເພື່ອປັບປຸງປະລິມານການເຄືອບກາວ; ປັບປຸງປະລິມານອຸນຫະພູມແຫ້ງ, ຫຼຸດຜ່ອນຄວາມໄວຂອງການປະສົມ. ການປິ່ນປົວຄັ້ງທີສອງຂອງພື້ນຮູບເງົາເພື່ອປັບປຸງຄວາມກົດດັນດ້ານ; ຫຼຸດຜ່ອນການນໍາໃຊ້ຂອງສິ່ງເສບຕິດໃນຮູບເງົາທີ່ປະສົມຫນ້າ. ວິທີການທັງຫມົດເຫຼົ່ານີ້ສາມາດຊ່ວຍພວກເຮົາໃຫ້ປັບປຸງບັນຫາຂອງ Peel ທີ່ບໍ່ດີແຮງຂອງອົງປະກອບຂອງອົງປະກອບທີ່ບໍ່ດີ.
5. ຄວາມຮ້ອນປະທັບຕາບໍ່ດີ
ກະເປົາປະສົມຄວາມຮ້ອນເຮັດໃຫ້ປະທັບຕາປະຕິບັດງານບໍ່ດີແລະສາເຫດຂອງມັນແມ່ນພື້ນຖານໃນສະຖານະການຕໍ່ໄປນີ້.
ຄວາມເຂັ້ມແຂງຂອງການປະທັບຕາຄວາມຮ້ອນແມ່ນທຸກຍາກ. ເຫດຜົນຕົ້ນຕໍຂອງປະກົດການແມ່ນບໍ່ໄດ້ຮັບການປິ່ນປົວຢ່າງສົມບູນຫຼືອຸນຫະພູມຂອງການປະທັບຕາຄວາມຮ້ອນແມ່ນຕໍ່າເກີນໄປ. ເພີ່ມປະສິດທິພາບຂະບວນການຮັກສາຫຼືເພີ່ມປະທັບໃຫ້ເຫັນອຸນຫະພູມມີດປະທັບຕາສາມາດປັບປຸງບັນຫາໄດ້.
ຄວາມຮ້ອນປະທັບຕາກວມເອົາດັດສະນີການຫຼຸດຜ່ອນແລະດັດສະນີສະລັບສັບຊ້ອນ. ສາເຫດຕົ້ນຕໍຂອງປະກົດການນີ້ແມ່ນພັນທະບັດບໍ່ໄດ້ຮັບການປິ່ນປົວ. ປັບເວລາຮັກສາຫຼືປັບເນື້ອຫາຂອງຕົວແທນການຮັກສາສາມາດປັບປຸງບັນຫານີ້ໄດ້.
ການເປີດໃຈທີ່ບໍ່ດີ / ການເປີດທີ່ບໍ່ດີຂອງຮູບເງົາຊັ້ນໃນ. ສາເຫດຂອງປະກົດການດັ່ງກ່າວແມ່ນຕົວແທນເປີດຫນ້ອຍເກີນໄປ, ເຊິ່ງກໍ່ໃຫ້ເກີດອຸປະກອນການໃຫຍ່ເກີນໄປ (ຕົວປ່ຽນແປງ) ແລະຫນ້າດິນທີ່ຫນຽວ. ບັນຫານີ້ສາມາດໄດ້ຮັບການປັບປຸງໄດ້ຮັບການປັບປຸງໂດຍການເພີ່ມປະລິມານຂອງຕົວແທນເປີດ, ປັບຈໍານວນຕົວປ່ຽນ, ແລະຫລີກລ້ຽງການປົນເປື້ອນມັດທະຍົມໃນຮູບເງົາ.
ທີ່ສິ້ນສຸດລົງ
ຂອບໃຈສໍາລັບການອ່ານຂອງທ່ານ, ພວກເຮົາຫວັງວ່າພວກເຮົາຈະມີໂອກາດເປັນຄູ່ຮ່ວມງານຂອງທ່ານ.
ຖ້າທ່ານມີຄໍາຖາມຫຍັງທີ່ຕ້ອງການຖາມ, ກະລຸນາແຈ້ງໃຫ້ພວກເຮົາຮູ້ແລະຕິດຕໍ່ພວກເຮົາ.
ຕິດຕໍ່:
ທີ່ຢູ່ອີເມວ:fannie@toppackhk.com
WhatsApp: 0086 134 10678885
ເວລາໄປສະນີ: APR-01-2022