കമ്പോസിറ്റ് പാക്കേജിംഗ് ബാഗുകളുടെ അടിസ്ഥാന തയ്യാറെടുപ്പ് പ്രക്രിയ നാല് ഘട്ടങ്ങളായി തിരിച്ചിരിക്കുന്നു: അച്ചടി, ലമിനിംഗ്, സ്ലിറ്റിംഗ്, ബാഗ് നിർമ്മാണം, അതിൽ അന്തിമ ഉൽപ്പന്നത്തിന്റെ പ്രകടനത്തെ ബാധിക്കുന്ന പ്രധാന പ്രക്രിയകളാണ്.
കോമ്പൗണ്ടിംഗ് പ്രക്രിയ
ഉൽപ്പന്ന പാക്കേജിംഗ് പ്രക്രിയ രൂപകൽപ്പന ചെയ്യുക, വിവിധതരം കെ.എസ്. കമ്പോസിറ്റ് പ്രോസസ്സിംഗ് സാങ്കേതികവിദ്യ എത്ര തികഞ്ഞതാണെങ്കിലും, തെറ്റായ പശ തിരഞ്ഞെടുക്കുക, കൂടാതെ, ശക്തികൂർന്ന ശക്തി, ചോർച്ച, പൊള്ളാരുകൾ, മറ്റ് പരാജയങ്ങൾ എന്നിവ കുറയ്ക്കുന്നതിന് പ്രതികൂല പ്രത്യാഘാതങ്ങൾക്കും പോസ്റ്റ് പ്രോസസ്സിംഗ് കാരണമാകും.
പൊതുവേ വിവിധ ഘടകങ്ങളെ പരിഗണിക്കാൻ എല്ലാതരം ഘടകങ്ങളും പരിഗണിക്കുക, പൊതുവേ, ഒരു സംയോജിത പശ ഇനിപ്പറയുന്ന നിബന്ധനകൾ പാലിക്കണം:
വിഷാംശം
പാക്കേജിംഗ് ദ്രാവകങ്ങൾക്ക് ശേഷം ദോഷകരമായ എക്സ്ട്രാക്റ്റുകളൊന്നും ദൃശ്യമാകില്ല.
ഭക്ഷണ സംഭരണത്തിന്റെ താപനില ആവശ്യകതകൾക്ക് ബാധകമാണ്.
നല്ല കാലാവസ്ഥാ പ്രതിരോധം, മഞ്ഞ, പൊള്ളൽ, ചോക്ക്ലിംഗും പൊളിറ്റലും ഇല്ല.
എണ്ണകൾ, സുഗന്ധങ്ങൾ, വിനാഗിരികൾ, മദ്യം എന്നിവയ്ക്കുള്ള പ്രതിരോധം.
അച്ചടി പാറ്റേൺ മഷിയുടെ മണ്ണൊലിപ്പ് ഇല്ല, മഷിക്ക് ഉയർന്ന ബന്ധമുണ്ടെന്ന് പ്രതീക്ഷിക്കുന്നു.
കൂടാതെ, മണ്ണൊലിപ്പിനെതിരായ പ്രതിരോധം, ഉള്ളടക്കത്തിൽ ധാരാളം സുഗന്ധവ്യഞ്ജനങ്ങൾ, മദ്യം, വെള്ളം, കൊഴുപ്പ്, ഫാറ്റി ആസിഡുകൾ മുതലായവയിൽ, അവയുടെ സവിശേഷതകൾ വ്യത്യാസപ്പെട്ടിരിക്കുന്നു, ഇത് പാക്കേജിംഗ് ബാഗിൽ നിന്ന് തകരാറിലാകും, പരാജയത്തിന് കേടുപാടുകൾ സംഭവിക്കുന്നു. തൽഫലമായി, മുകളിലുള്ള പദാർത്ഥങ്ങളുടെ മണ്ണൊലിപ്പിനെ ചെറുക്കാനുള്ള കഴിവ് പശ ഉണ്ടായിരിക്കണം, എല്ലായ്പ്പോഴും മതിയായ പശ തൊലി ശക്തി നിലനിർത്തുക.
ഉണങ്ങിയ സംയോജന രീതി, നനഞ്ഞ സംയോജിത രീതി, എക്സ്ട്രാറ്റ് പ്രോജോസിറ്റ് രീതി, ചൂടുള്ള ഉരുകുന്നത് സംയോജിത രീതി, കോ-എക്സ്ട്രാഡു സംയോജനം, മറ്റ് നിരവധി കാര്യങ്ങൾ എന്നിവയാണ് പ്ലാസ്റ്റിക് ഫിലിം കമ്പോസിറ്റ് രീതികൾ..
1, ഉണങ്ങിയ കോമ്പൗണ്ടിംഗ്
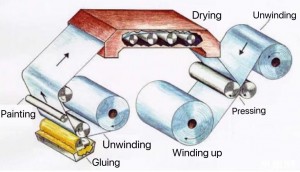
പ്ലാസ്റ്റിക് പാക്കേജിംഗ് ലാമിനേഷന്റെ ഏറ്റവും സാധാരണമായ രീതിയാണ് വരണ്ട ലാമിനേഷൻ രീതി. താപനില, പിരിമുറുക്കം, വേഗത എന്നിവയിൽ, ലാമിനേറ്റിംഗ് മെഷീൻ ബേക്കിംഗ് ചാനലിന്റെ ഒരു പാളി (ഒറ്റ-ഘടക മേഖല, ദുർഗന്ധം, ദുർഗന്ധം വമിക്കുന്നു), അതിനാൽ ലോവന്റ് ബാഷ്പീകരിക്കപ്പെടുകയും പിന്നീട് ചൂടുള്ള മാധ്യമങ്ങൾ നടത്തുകയും ചെയ്യുന്നു റോളറുകൾ, ഹോട്ട് പ്രസ് സ്റ്റേഷനിൽ, രണ്ടാമത്തെ കെ.ഇ.യിൽ (പ്ലാസ്റ്റിക് ഫിലിം, പേപ്പർ അല്ലെങ്കിൽ അലുമിനിയം ഫോയിൽ) ഒരു സംയോജിത ചിത്രമായി ബന്ധിപ്പിച്ചിരിക്കുന്നു.
വരണ്ട ലാമിനേഷന് ഏതെങ്കിലും തരത്തിലുള്ള ഒരു സിനിമയെ ലാമിനേറ്റ് ചെയ്യാൻ കഴിയും, മാത്രമല്ല ഉള്ളടക്കങ്ങളെ ആശ്രയിച്ച് ഉയർന്ന പ്രകടന പാക്കേജിംഗ് മെറ്റീരിയലുകൾ സമന്വയിപ്പിക്കാനുള്ള കഴിവ്. അതിനാൽ, പാക്കേജിംഗിൽ, പ്രത്യേകിച്ച് പ്രതിദിന രാസ പാക്കേജിംഗിൽ വികസനം പരിഹരിച്ചു.
2,നനഞ്ഞ കോമ്പൗണ്ടിംഗ്
വെറ്റ് കോമ്പോസിറ്റ് രീതി ഉപരിതലത്തിൽ പശ ഒരു ഒരു സംയോജനത്തിന്റെ ഒരു പാളി (പ്ലാസ്റ്റിക് ഫിലിം, അലുമിനിയം ലോയിൽ) കോട്ടിയാണ്, പശ, പ്രഷർ റോളർ, മറ്റ് വസ്തുക്കൾ എന്നിവയിലൂടെ (പേപ്പർ, സെലോഫെയ്ൻ) സംയോജിത സംയോജിത സംയോജനമാണ്, തുടർന്ന് അടുപ്പത്തുവെച്ചു വറ്റിച്ച ശേഷം.
നനഞ്ഞ സംയോജന പ്രക്രിയ ലളിതമാണ്, പശ, കുറഞ്ഞ ചെലവ്, ഉയർന്ന സംയോജിത കാര്യക്ഷമത, അവശേഷിക്കുന്ന ലായകത്തെ ഒഴിവാക്കുക.
നനഞ്ഞ സംയോജിത ജനിമിംഗ് മെഷീനും വർക്കിംഗ് തത്വവും ഉപയോഗിച്ചതും വരണ്ട സംയോജിത രീതിയും അടിസ്ഥാനപരമായി ഒരുപോലെയാണ്, ഈ പശയിൽ പൂശുന്ന ആദ്യ കെ.ഇ. ലളിതവും കുറഞ്ഞതുമായ പശ അളവ്, സംയുക്ത വേഗത, സംയോജിത ഉൽപ്പന്നങ്ങൾ എന്നിവ ശേഷിക്കുന്ന പരിഹാരങ്ങളിൽ അടങ്ങിയിട്ടില്ല, മലിനീകരണ ബദൽ.
3, എക്സ്ട്രാക്കേഷൻ കോമ്പൗണ്ടിംഗ്
എക്സ്ട്രൂമാവ് കോമ്പൗണ്ടിംഗ് പ്രോസസ്സിംഗ് പ്രക്രിയയുടെ ഏറ്റവും സാധാരണമായ രീതിയാണ്, അത് അസംസ്കൃത വസ്തുക്കളായി തെർമോപ്ലാസ്റ്റിക് റെയിൻ ഉപയോഗിച്ചാണ്, ഇത് മറ്റൊരു തരത്തിലുള്ള അല്ലെങ്കിൽ രണ്ട് ചിത്രങ്ങളുമായി ചേർന്ന് മയാൽ ചൂടാക്കി, തുടർന്ന് തണുപ്പിക്കുകയും സുഖപ്പെടുത്തുകയും ചെയ്യുന്നു. മൾട്ടി-ലെയർ കോ-എക്സ്ട്രൂഷൻ ലാമിനേഷൻ പലതരം പ്ലാസ്റ്റിക് റെസിൻ റിസോർഡർ ആണ്, അന്ത്യനായ കോ-എക്സ്ട്രൂഷൻ, ഡൈ ലാമിനലിലേക്ക്, സിനിമയിലേക്ക്.
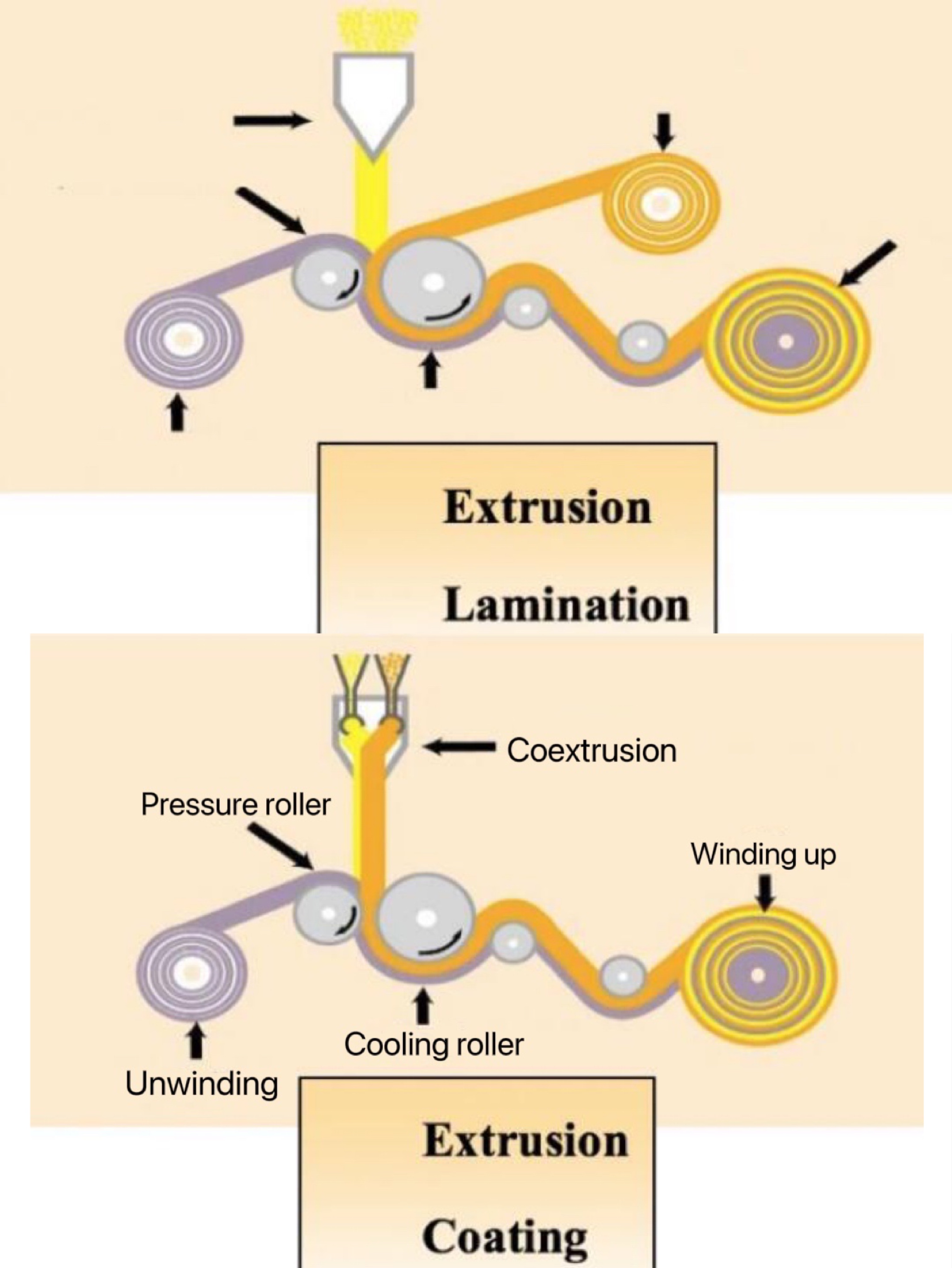
കോമ്പോസൈറ്റ് മെറ്റീരിയലുകൾ ഗുണനിലവാര പ്രശ്നങ്ങൾക്കും പരിഹാരങ്ങൾക്കും സാധ്യതയുണ്ട്
ഫ്ലെക്സിബിൾ പാക്കേജിംഗിന്റെ ഉൽപാദനത്തിനും പ്രോസസ്സിംഗിലെയും ഒരു പ്രധാന പ്രക്രിയയാണ് കോമ്പൗണ്ടിംഗ്, അതിന്റെ പൊതുവായ പരാജയങ്ങൾ, കുറഞ്ഞ വേഗത്തിൽ, വർദ്ധിച്ചതോ ചുരുങ്ങിയതോ ആയ അരികുകൾ, സംയോജിത ഉൽപ്പന്നങ്ങൾ, ഉൽപാദനത്തിന്റെ വിശകലനത്തിലും ഉൽപാദനത്തിന്റെ വിശകലനത്തിലും.
1, ചുളുക്കം പ്രതിഭാസം
ഈ പ്രതിഭാസത്തിന്റെ വരണ്ട സംയോജിത പരാജയത്തിൽ പരാജയപ്പെട്ടതിന്റെ ഒരു വലിയ അനുപാതം നേരിട്ട് പൂർത്തിയാക്കിയ ഉൽപ്പന്ന ബാഗ് നിർമ്മാണത്തിന്റെ ഗുണനിലവാരത്തെ നേരിട്ട് ബാധിക്കുന്നു.
ഈ പരാജയത്തിനുള്ള പ്രധാന കാരണങ്ങൾ ഇനിപ്പറയുന്നവയാണ്.
കമ്പോപീറ്റ് മെറ്റീരിയലിന്റെ മോശം ഗുണനിലവാരം അല്ലെങ്കിൽ അച്ചടിക്കൽ കെ.ഇ. ഫിലിം വോളിയം വലിയ അളവിൽ മെഷീനിൽ നിന്ന് വേർതിരിക്കുകയാണെങ്കിൽ, ഫിലിം അപ്പ്, ഡ down ൺ, ഇടത്, വലത് പ്ലെയ്സ്മെന്റ് ആംപ്ലിറ്റ്യൂഡ് എന്നിവയും താരതമ്യേന വലുതാണ്, കാരണം ഇത് ചൂടുള്ള പത്ര റോളറുകൾക്കിടയിൽ പ്രവേശിക്കാൻ കഴിയില്ല, കാരണം ഇത് ചൂടുള്ള പ്രസ് റോളറുകളും, ഫലമായി ഉൽപ്പന്ന സ്ക്രാപ്പ് ചെയ്യും, ഫലമായി ഉൽപ്പന്ന സ്ക്രാപ്പ്. കോമ്പോസിറ്റ് മെറ്റീരിയൽ PE അല്ലെങ്കിൽ CPP ആണെങ്കിൽ, കനം വ്യതിചലനമാണെങ്കിൽ, ഈ സമയത്ത്, സംയോജിത വസ്തുക്കളുടെ പിരിമുറുക്കം ഉചിതമായി വർദ്ധിപ്പിക്കും, ഒപ്പം ചൂടുള്ള അമർത്തുന്ന റോളർ എക്സ്ട്രൂഷനായി ഒരു തിരശ്ചീന അവസ്ഥയായി വർദ്ധിപ്പിക്കാൻ കഴിയും. എന്നിരുന്നാലും, പിരിമുറുക്കം ഉചിതമായിരിക്കണമെന്ന കാര്യം ശ്രദ്ധിക്കേണ്ടതാണ്, കൂടുതൽ പിരിമുറുക്കം സംയോജിത വസ്തുക്കൾ നീളമുണ്ടാക്കാൻ എളുപ്പമാണ്, അതിന്റെ ഫലമായി ബാഗ് വായ അതിൻറെ ചരിവ്. സംയോജിത മെറ്റീരിയലിന്റെ കനം വളരെ വലുതാണെങ്കിൽ, ഇത് ശരിക്കും ഉപയോഗിക്കാൻ കഴിയില്ല, കൈകാര്യം ചെയ്യണം.
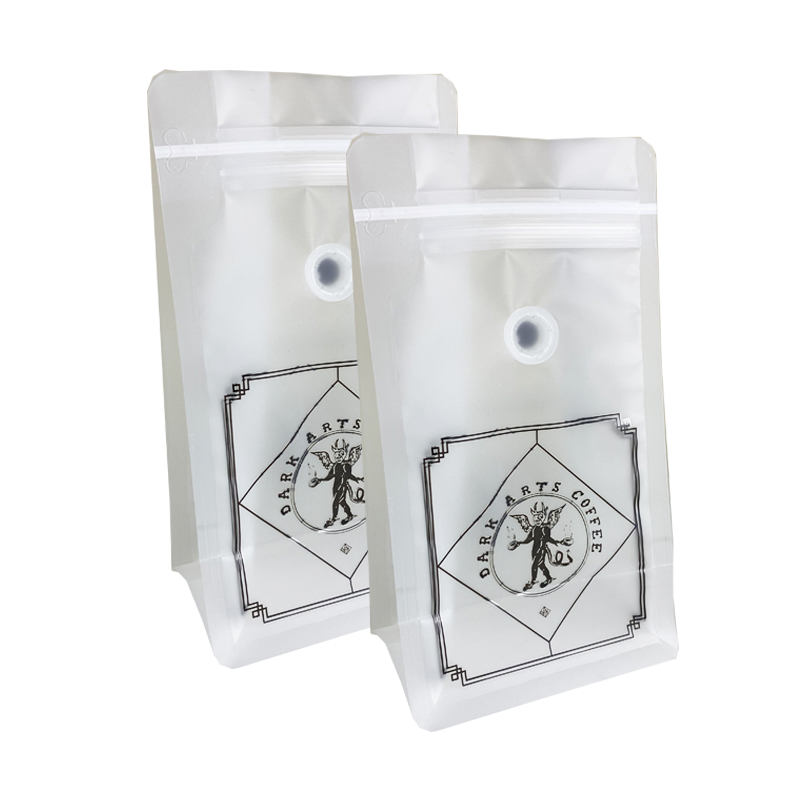
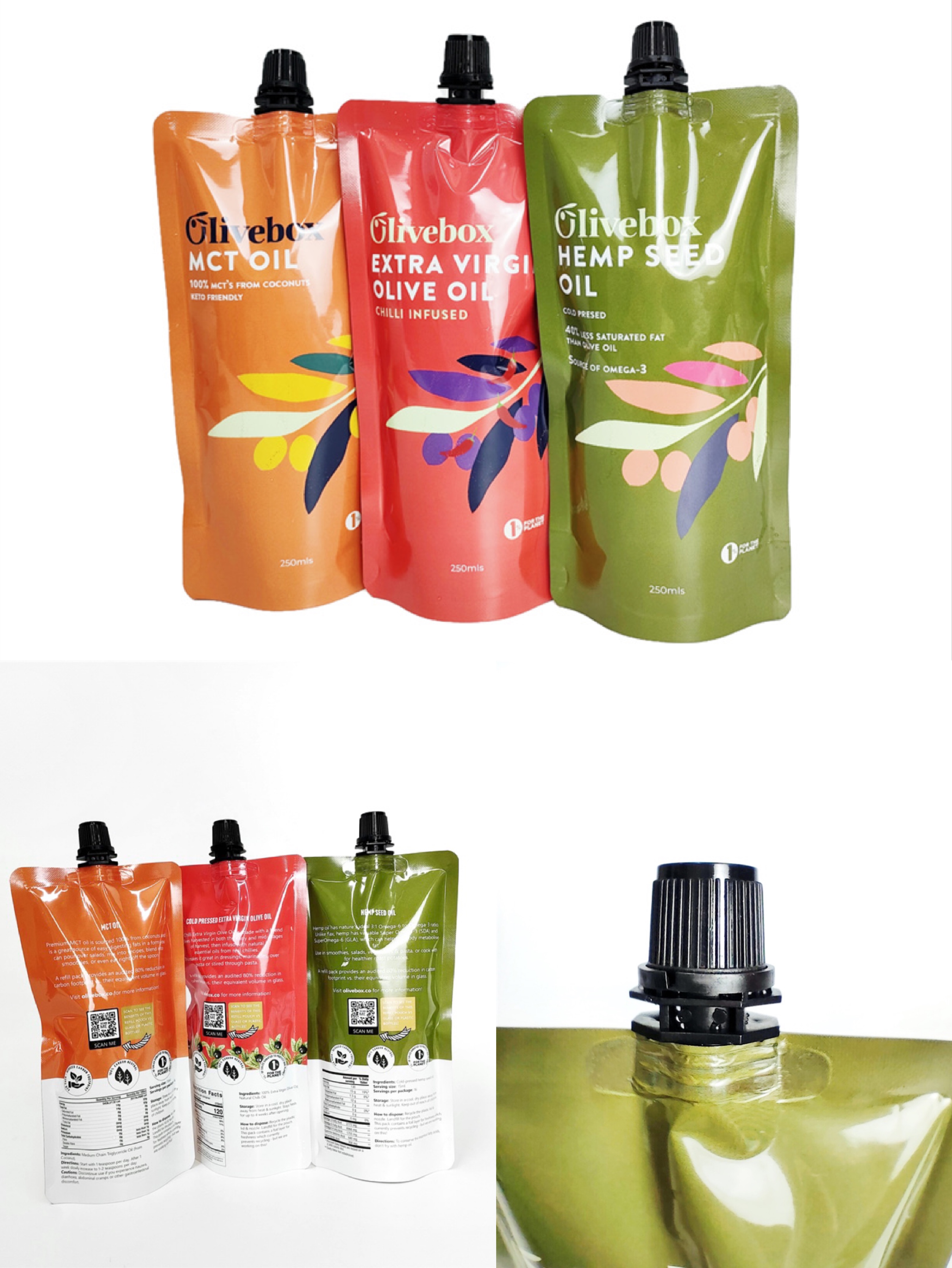
2, സംയോജിത വൈറ്റ് പാടുകൾ
മോശം മഷി കവറേജ് നിരക്ക് നിരക്ക്: കമ്പോസിറ്റ് വൈറ്റ് മഷിക്ക്, മഷി ആഗിരണം അസ്ഥിരീകരണം എന്നാൽ വെളുത്ത പാടുകൾ മൂലമുണ്ടാകുന്ന അസ്ഥിരതയല്ല, ഈ രീതിയുടെ ഉണക്കപ്പെടുന്ന ശേഷി മെച്ചപ്പെടുത്തുന്നതിന് ലഭ്യമാണ്; ഇപ്പോഴും വെളുത്ത പാടുകൾ ഉണ്ടെങ്കിൽ, വൈറ്റ് മഷി കവറേജ് മെച്ചപ്പെടുത്തുക എന്നതാണ് പൊതുവായ പരിഹാരം, കാരണം വെളുത്ത മഷിയുടെ ഞരക്കം പരിശോധിക്കുന്നു, കാരണം നല്ല മഷിയുടെ നിരക്ക് പൊടിക്കുന്നത് ശക്തമാണ്.
ഉൽപാദിപ്പിക്കുന്ന വെളുത്ത പാടുകളുടെ ഉപരിയായി: മഷി കാരണം പശ കൊണ്ട് പൂശുന്നു, മഷി കാരണം, പശയിൽ പൂശുന്നു, വിഭാഗം കണ്ടുമുട്ടുമ്പോൾ, പ്രകാശത്തെ പ്രതിഫലിപ്പിക്കുന്നത് പോലെ മികച്ചതല്ല, പ്രകാശം പ്രതിഫലനം, വെളുത്ത പാടുകളുടെ രൂപീകരണം. ഏകീകൃത റബ്ബർ റോളർ ഉപയോഗിച്ച് കോട്ടിംഗ് മിനുസപ്പെടുത്താൻ പരിഹാരം ഉപയോഗിക്കാം, അല്ലെങ്കിൽ മാറ്റിസ്ഥാപിക്കാനുള്ള തുക വർദ്ധിപ്പിക്കുക.
3, സംയുക്ത ബബിൾ
ഇനിപ്പറയുന്ന സാഹചര്യങ്ങളിലും അനുബന്ധ രീതികളിലും സംയോജിത കുമിളകൾ സൃഷ്ടിക്കുന്നു.
പ്രതിഭാസത്തിൽ സംയുക്ത കുമിളകൾ
1. മോശം സിനിമ, പശയുടെ സാന്ദ്രത മെച്ചപ്പെടുത്തണം, മാറ്റിസ്ഥാപിക്കൽ, മീൻ, കെപിടി ഉപരിതലം, കെപിടി ഉപരിതലം, കുമിളകൾ നിർമ്മിക്കാൻ എളുപ്പമല്ല, പ്രത്യേകിച്ച് ശൈത്യകാലത്ത് കുമിളകൾ ഉത്പാദിപ്പിക്കാൻ എളുപ്പമല്ല. മഷിയിലെ വായു കുമിളകൾ,തകരപ്പാതംനീക്കംചെയ്യാനുള്ള പശയുടെ അളവ് വർദ്ധിപ്പിക്കുന്നതിനുള്ള രീതി ഉപയോഗിക്കുക.
2,മഷി ഉപരിതല ബമ്പി, ബബിൾ, ഫിലിം കോമ്പൗണ്ടിംഗ് താപനിലയും വർദ്ധിക്കാനുള്ള സമ്മർദ്ദവും ആയിരിക്കണം.
3, മഷിയുടെ ഉപരിതലത്തിൽ പശ ചേർക്കുന്നതിന്റെ അളവ് കുറവാണ്, മിനുസമാർന്ന റോളർ മർദ്ദം ഒട്ടിക്കുന്ന സമയവും മിനുസമാർന്ന റോളറുകളുടെ ഉപയോഗവും വർദ്ധിപ്പിക്കും, സംയുക്ത വേഗത കുറയ്ക്കുന്നതിന്, നല്ല നനവ് തിരഞ്ഞെടുക്കുക.
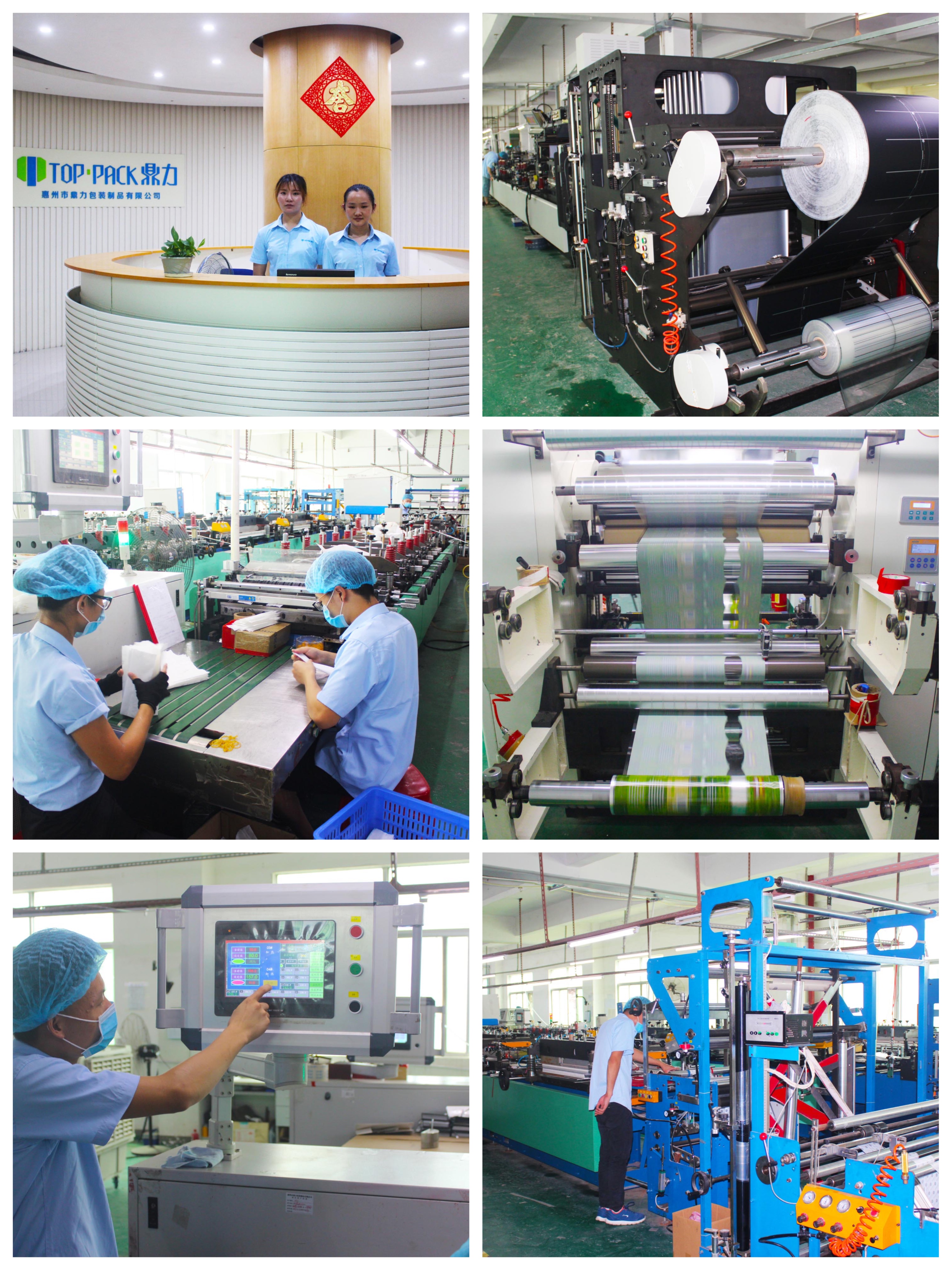
4. സിനിമയിലെ അഡിറ്റീവുകൾ (ലൂബ്രിക്കന്റ്, ആന്റിമാറ്റിക് ഏജന്റ്) പശയിൽ തുളച്ചുകയറുന്നു, അതിനാൽ നിങ്ങൾ ഉയർന്ന മോളികീയ ഭാരവും വേഗത്തിലുള്ള ക്യൂണറും തിരഞ്ഞെടുത്ത് 3 മാസത്തിൽ കൂടുതൽ പ്ലെയ്സ്മെന്റ് കാലയളവ് ഉയർത്തിപ്പിടിക്കുക, കാരണം കൊറോണ ചികിത്സ നഷ്ടപ്പെട്ടു.
5,ശൈത്യകാലത്തെ താപനില കുറവാണ്, ഫിലിം, മഷി കൈമാറ്റം എന്നിവ കുറവാണ്, റീസെറ്റ് വിന്യാസ പ്രഭാവം നല്ലതല്ല, അതിനാൽ ഓപ്പറേഷൻ ഒരു നിശ്ചിത താപനില നിലനിർത്തുക.
6,ഉണങ്ങിയ താപനില വളരെ ഉയർന്നതാണ്, പശ രൂപാന്തരീകരണം അല്ലെങ്കിൽ ഉപരിതലത്തിന്റെ പുറംതോട് സംഭവിക്കുന്നു, അകത്ത് പശ വരണ്ടതല്ല, അതിനാൽ പശയുടെ വരണ്ട താപനില ക്രമീകരിക്കണം.
.
8,ഹൈ ചലച്ചിത്ര തടസ്സം കാരണം, കമ്പോസിറ്റ് ഫിലിമിൽ താമസിക്കുന്ന പശാവശക്തിയുള്ള CO2 വാതകം കുമിളയിൽ അച്ചടിച്ചിട്ടില്ല, അതിനാൽ വരണ്ട ശനിയിൽ പശ സംക്ഷിപ്തമായി.
9. ഇങ്ക് ഫില്ലറിനുള്ള ഗ്ലൈക്കോളിക് ആസിഡ് ഒരു നല്ല ലായകമാണ്, മഷിയിൽ റബ്ബർ അലിഞ്ഞുപോകുന്നു.
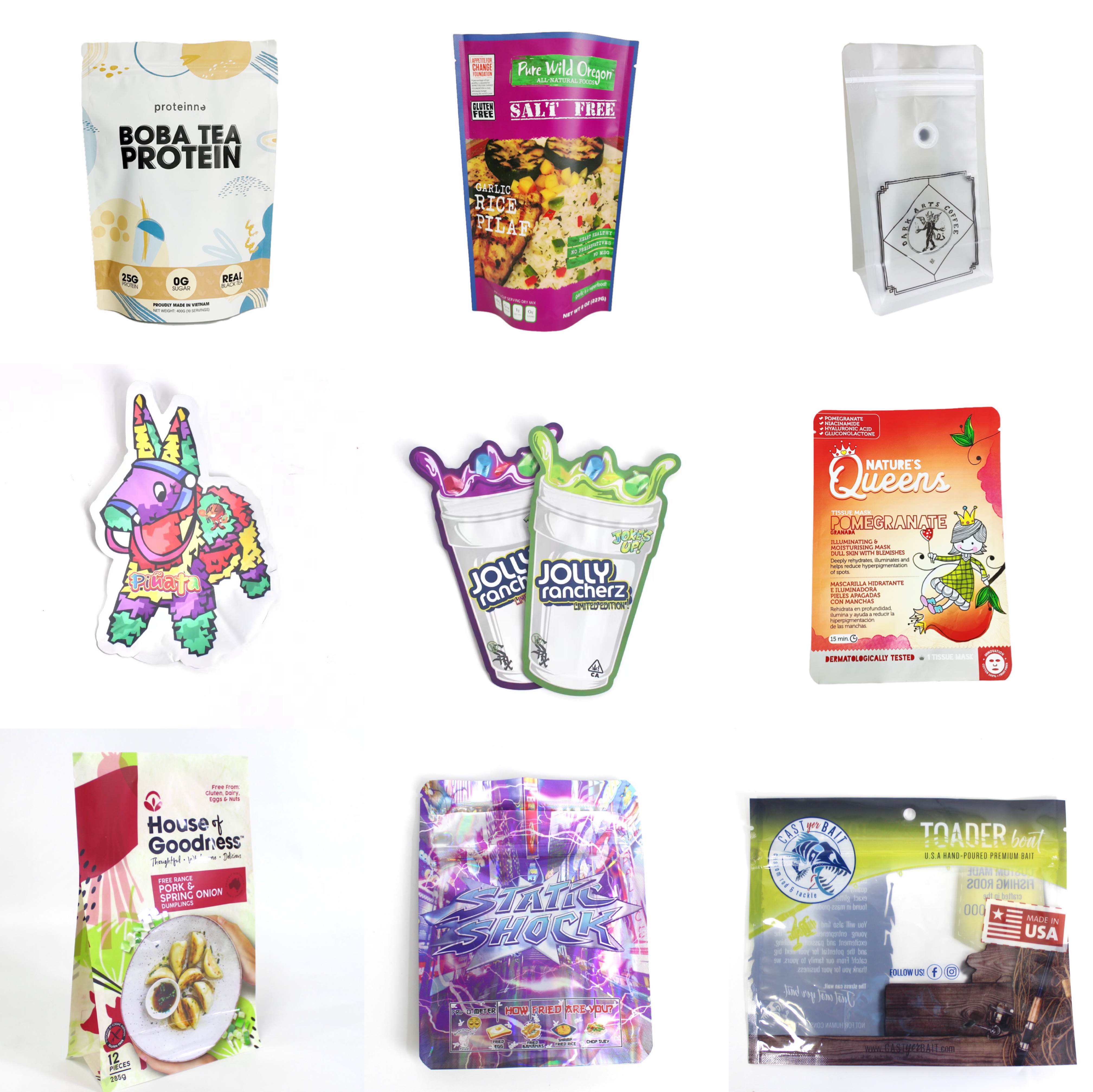
4, മോശം തൊലി ശക്തി
അപൂർണ്ണമായ ക്യൂണിംഗ്, അല്ലെങ്കിൽ പശയുടെ അളവ് വളരെ കുറവാണ്, അല്ലെങ്കിൽ ഉപയോഗിച്ച മഷി വളരെ കുറവാണ്, അല്ലെങ്കിൽ ദൈർഘ്യമില്ലാത്തതിനാൽ കോമ്പോസിറ്റ് ഫിലിമിന്റെ രണ്ട് പാളികൾക്കിടയിൽ ഫോഴ്സ് റിഡക്ഷൻ കുറച്ചു.
കുത്തിവയ്പ്പ് തുക വളരെ ചെറുതാണ്, പശയിൽ കുറവുണ്ടാകുമ്പോൾ, പശ വഷളാകുന്നു സംഭരണത്തിൽ പശയിൽ കലർത്തി, ഉണക്കമുന്തിരി അല്ലെങ്കിൽ മദ്യപിച്ച്, ഇത് അന്തിമ കമ്പോസിറ്റ് പീപ്പിൾ റിഡക്ഷാക്രിലേക്ക് നയിക്കും.
പശയുടെ ശരിയായ സംഭരണത്തിലേക്ക് ശ്രദ്ധിക്കുക, ഏറ്റവും ദൈർഘ്യമേറിയത് 1 വർഷത്തിൽ കൂടുതൽ (ടിന്നിന് മുദ്രയിടാം); വിദേശ വസ്തുക്കൾ പശ, പ്രത്യേകിച്ച് വെള്ളം, മദ്യം മുതലായവയിൽ നിന്ന് തടയുക, അത് പശ തകരാറിന് കാരണമാകും. പശ കോട്ടിംഗിന്റെ അളവ് മെച്ചപ്പെടുത്തുന്നതിന് ചിത്രം ഉചിതമാണ്; വരണ്ട താപനില വായുവിന്റെ അളവ് മെച്ചപ്പെടുത്തുക, സംയുക്തത്തിന്റെ വേഗത കുറയ്ക്കുക. ഉപരിതല പിരിമുറുക്കം മെച്ചപ്പെടുത്തുന്നതിന് ഫിലിം ഉപരിതലത്തിന്റെ രണ്ടാമത്തെ ചികിത്സ; ഫിലിം കോമ്പൗണ്ടിംഗ് ഉപരിതലത്തിലെ അഡിറ്റീവുകളുടെ ഉപയോഗം കുറയ്ക്കുക. ഈ രീതികളെല്ലാം സംയോജിത സ്പാരിന്റെ പ്രശ്നം മെച്ചപ്പെടുത്താൻ സഹായിക്കും.
5. ഹീറ്റ് മുദ്ര മോശമാണ്
കോമ്പൗണ്ട് ബാഗ് ഹീറ്റ് സീൽ മോശം പ്രകടനവും അതിന്റെ കാരണങ്ങളും അടിസ്ഥാനപരമായി ഇനിപ്പറയുന്ന സാഹചര്യങ്ങളാണ്.
ചൂട് അടയ്ക്കുന്ന ശക്തി ദരിദ്രമാണ്. പ്രതിഭാസത്തിനുള്ള പ്രധാന കാരണങ്ങൾ പൂർണ്ണമായും സുഖം പ്രാപിച്ചിട്ടില്ല അല്ലെങ്കിൽ ചൂട് സീലിംഗ് താപനില വളരെ കുറവാണ്. ക്യൂറിംഗ് പ്രക്രിയയ്ക്ക് ഒപ്റ്റിമൈസ് ചെയ്യുക അല്ലെങ്കിൽ ഉചിതമായി വർദ്ധിപ്പിക്കുക.
ചൂട് സീൽ കവർ ഡെലോണൈനേഷൻ, റിഫ്രാക്റ്റീവ് സൂചിക. ഈ പ്രതിഭാസത്തിന്റെ പ്രധാന കാരണം ബോണ്ടിംഗ് സുഖപ്പെടുത്തിയിട്ടില്ല. ക്യൂറിംഗ് സമയം ക്രമീകരിക്കുക അല്ലെങ്കിൽ ക്യൂറിംഗ് ഏജന്റ് ഉള്ളടക്കത്തിന് ഈ പ്രശ്നം മെച്ചപ്പെടുത്താൻ കഴിയും.
ആന്തരിക ലെയർ ഫിലിമിന്റെ മോശം വ്യവസ്ഥ / മോശം തുറക്കൽ. ഈ പ്രതിഭാസത്തിന്റെ കാരണം വളരെ കുറച്ച് തുറന്ന ഏജന്റാണ്, അതിന്റെ ഫലമായി വളരെയധികം മെറ്റീരിയൽ (മോഡിഫയർ), സ്റ്റിക്കി അല്ലെങ്കിൽ കൊഴുപ്പുള്ള ഫിലിം ഉപരിതലം. ഓപ്പണിംഗ് ഏജന്റിന്റെ അളവ് വർദ്ധിപ്പിക്കുന്നതിലൂടെ ഈ പ്രശ്നം മെച്ചപ്പെടുത്താം, മോഡിഫയറിന്റെ അളവ് ക്രമീകരിച്ച്, ഫിലിം ഉപരിതലത്തിൽ ദ്വിതീയ മലിനീകരണം ഒഴിവാക്കുക.
അവസാനം
നിങ്ങളുടെ വായനയ്ക്ക് നന്ദി, നിങ്ങളുടെ പങ്കാളികളാകാൻ ഞങ്ങൾക്ക് അവസരമുണ്ടെന്ന് ഞങ്ങൾ പ്രതീക്ഷിക്കുന്നു.
നിങ്ങൾക്ക് എന്തെങ്കിലും ചോദ്യമുണ്ടെങ്കിൽ ചോദിക്കാൻ താൽപ്പര്യമുണ്ടെങ്കിൽ, ഞങ്ങളെ അറിയാനും ഞങ്ങളെ ബന്ധപ്പെടാനും അനുവദിക്കുക.
ബന്ധപ്പെടുക:
ഇമെയിൽ വിലാസം :fannie@toppackhk.com
വാട്ട്സ്ആപ്പ്: 0086 134 10678885
പോസ്റ്റ് സമയം: ഏപ്രിൽ -01-2022