Ⅰ Plastic bag production process commonly used in the three main printing processes
Plastic packaging bags, generally printed on a variety of plastic films, and then combined with the barrier layer and heat seal layer into a composite film, by slitting, bag-making to form packaging products. Among them, printing is the first line of production, but also the most important process, to measure the grade of a packaging product, printing quality is the first. Therefore, understanding and controlling the printing process and quality becomes the key to flexible packaging production.
1.Rotogravure
The printing of plastic film is mainly based on rotogravure printing process, and the plastic film printed by rotogravure has the advantages of high printing quality, thick ink layer, vivid colors, clear and bright patterns, rich picture layers, moderate contrast, realistic image and strong three-dimensional sense. Rotogravure printing requires that the registration error of each color pattern is not more than 0.3mm, and the deviation of the same color density and the deviation of the same color in the same batch are in accordance with the requirements of GB7707-87. Rotogravure printing plate with strong printing resistance, suitable for long-running live pieces. However, rotogravure printing also has shortcomings that cannot be ignored, such as complex pre-press plate making process, high cost, long cycle time, pollution, etc.
Rotogravure printing process has the difference between surface printing and inside printing process.
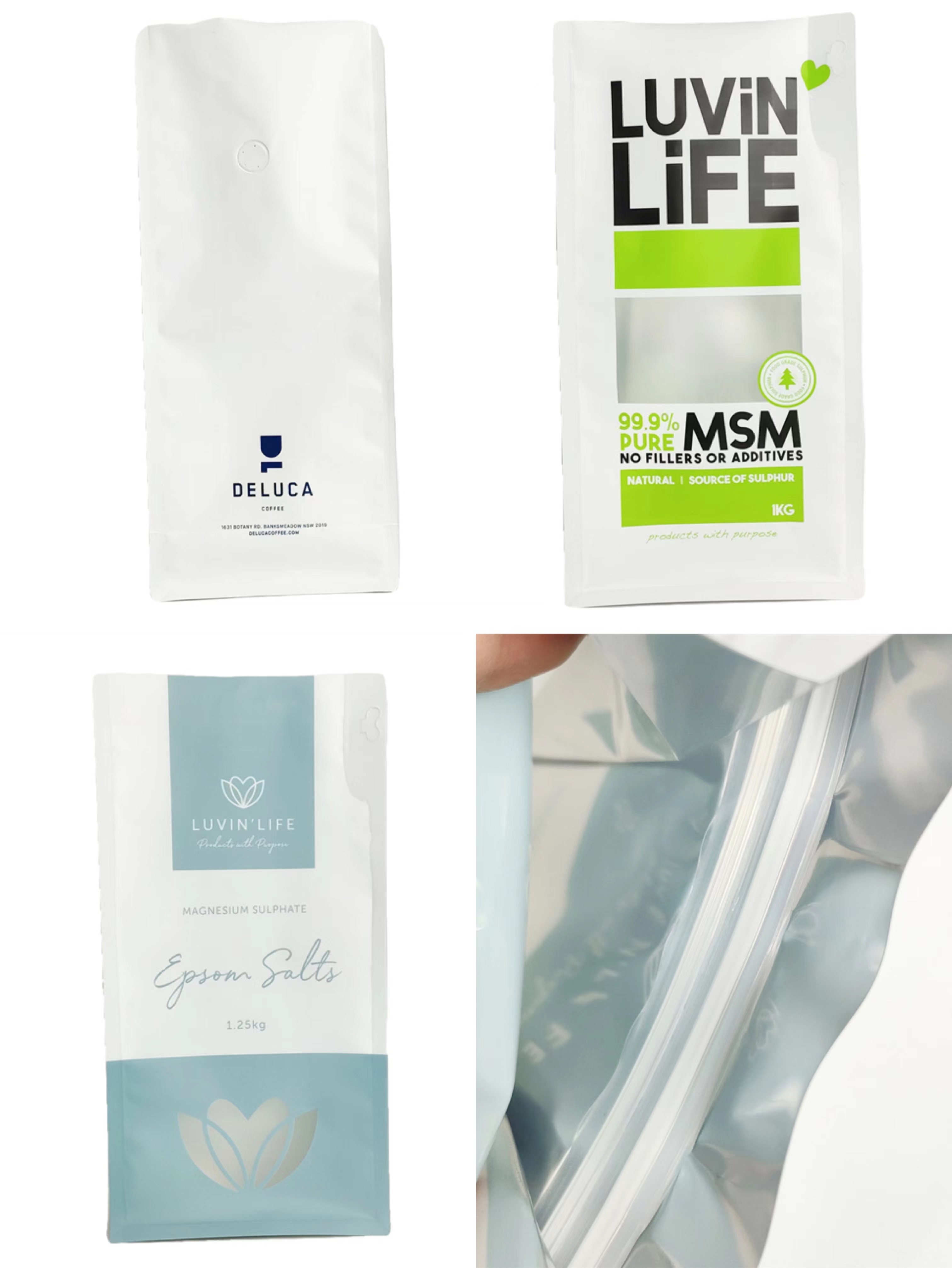
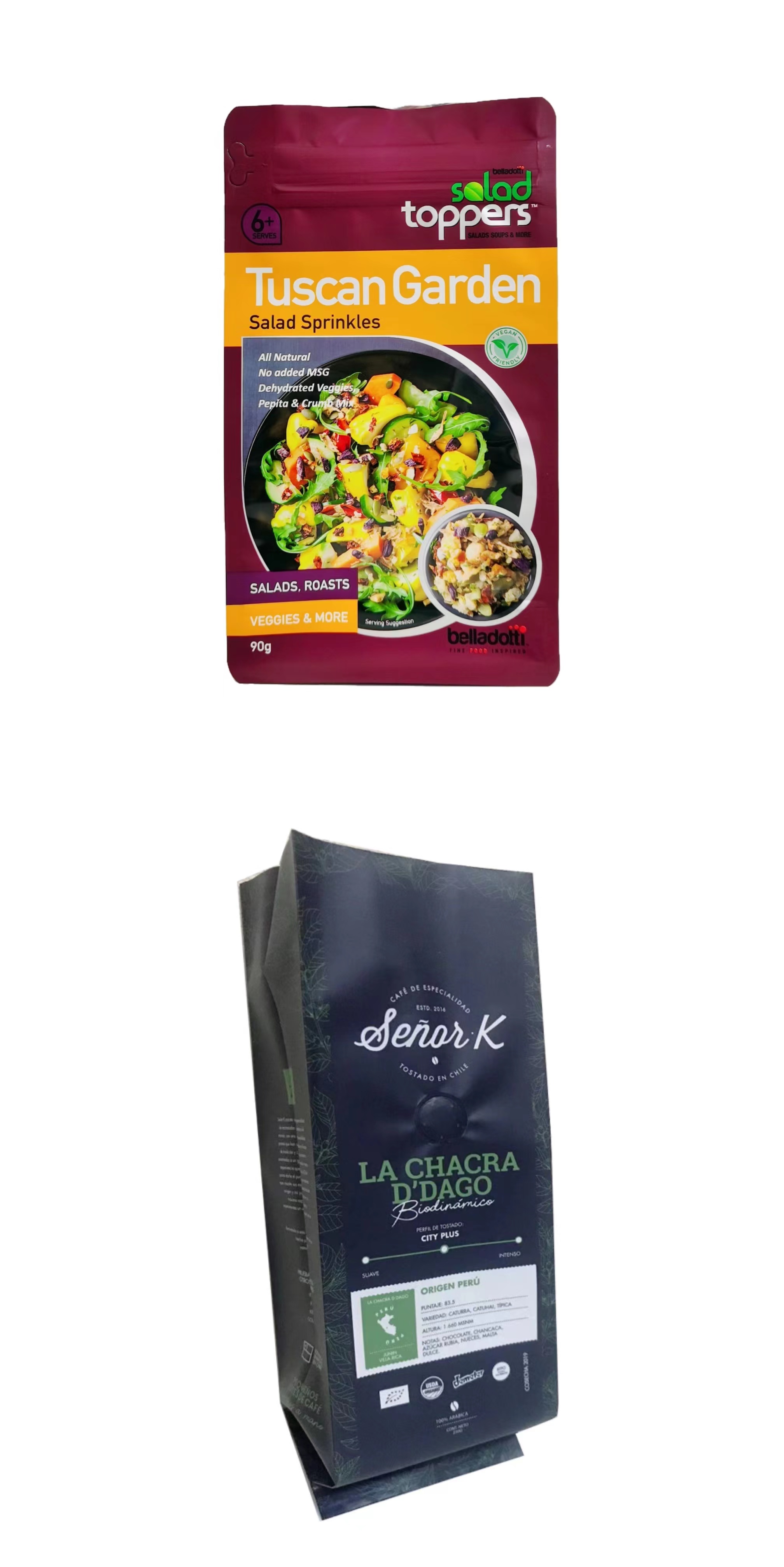
.
1)Surface printing
The so-called surface printing refers to the process of printing on plastic film, after the bag-making and other post-processes, the printed graphics are presented on the surface of the finished product.
The "surface printing" of plastic film is done with white ink as a base color, which is used to set off the printing effect of other colors. The main advantages are as follows. First, plastic white ink has good affinity with PE and PP film, which can improve the adhesion fastness of the printed ink layer. Secondly, the white ink base color is fully reflective, which can make the color of the print more vivid. Again, the printed base color can increase the thickness of the ink layer of the print, making the print more rich in layers and rich in the visual effect of floating and convexity. Therefore, the printing color sequence of the plastic film table printing process is generally determined as follows: white → yellow → magenta → cyan → black.
Surface printing plastic film requires good ink adhesion, and has considerable abrasion resistance, sunlight resistance, frost resistance, temperature resistance. In recent years, some ink manufacturers have developed special high-temperature cooking-resistant surface printing alcohol-soluble ink, wear resistance and sunlight resistance, adhesion and color gloss are very good.
2)Inside printing process
Inside printing process is a special printing method that uses a plate with reverse image graphics and transfers the ink to the inside of the transparent substrate, thus showing the positive image graphics on the front side of the substrate.
In order to get the same visual effect as the "table printing", the printing process printing color sequence should be the opposite of the "table printing", that is, the white ink base color on the last printing, so that from the front of the print, the white ink base color to play a role in setting off the role of the colors. Therefore, the printing process printing color sequence should be: black → blue → magenta → yellow → white.
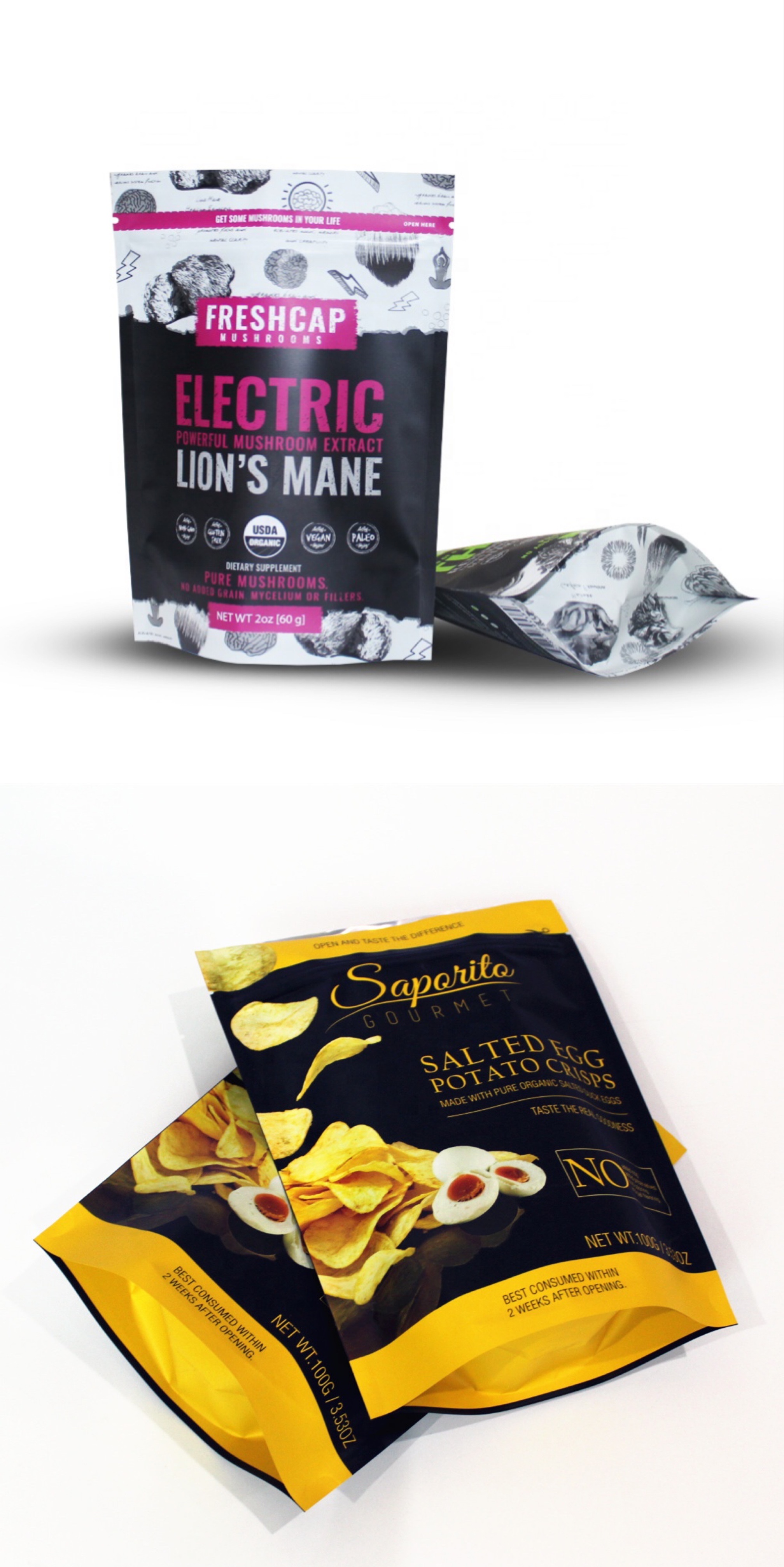
2.Flexography
Flexographic printing mainly uses flexible letterpress plates and fast-drying letterpress ink. Its equipment is simple, low cost, light quality of the plate, low pressure when printing, small loss of plate and machinery, low noise and high speed when printing. The flexo plate has short plate change time, high work efficiency, soft and flexible flexo plate, good ink transfer performance, wide adaptability of printing materials, and lower cost than rotogravure printing for printing small quantities of products. However, flexo printing requires higher ink and plate material, so the printing quality is slightly inferior to the rotogravure process.
3.Screen Printing
When printing, the ink is transferred to the substrate through the mesh of the graphic part by the squeezing of the squeegee, forming the same graphic as the original.
Screen printing products rich ink layer, bright color, full color, strong coverage, a wide range of ink varieties, adaptability, printing pressure is small, easy to operate, simple and easy plate making process, low investment in equipment, so low cost, good economic efficiency, a wide range of substrate materials.
Packaging is no less important than advertising in promoting the overall image of goods, it has many effects such as beautifying goods, protecting goods, and facilitating the circulation of goods. Printing plays a very important position in the process of making packaging bags.
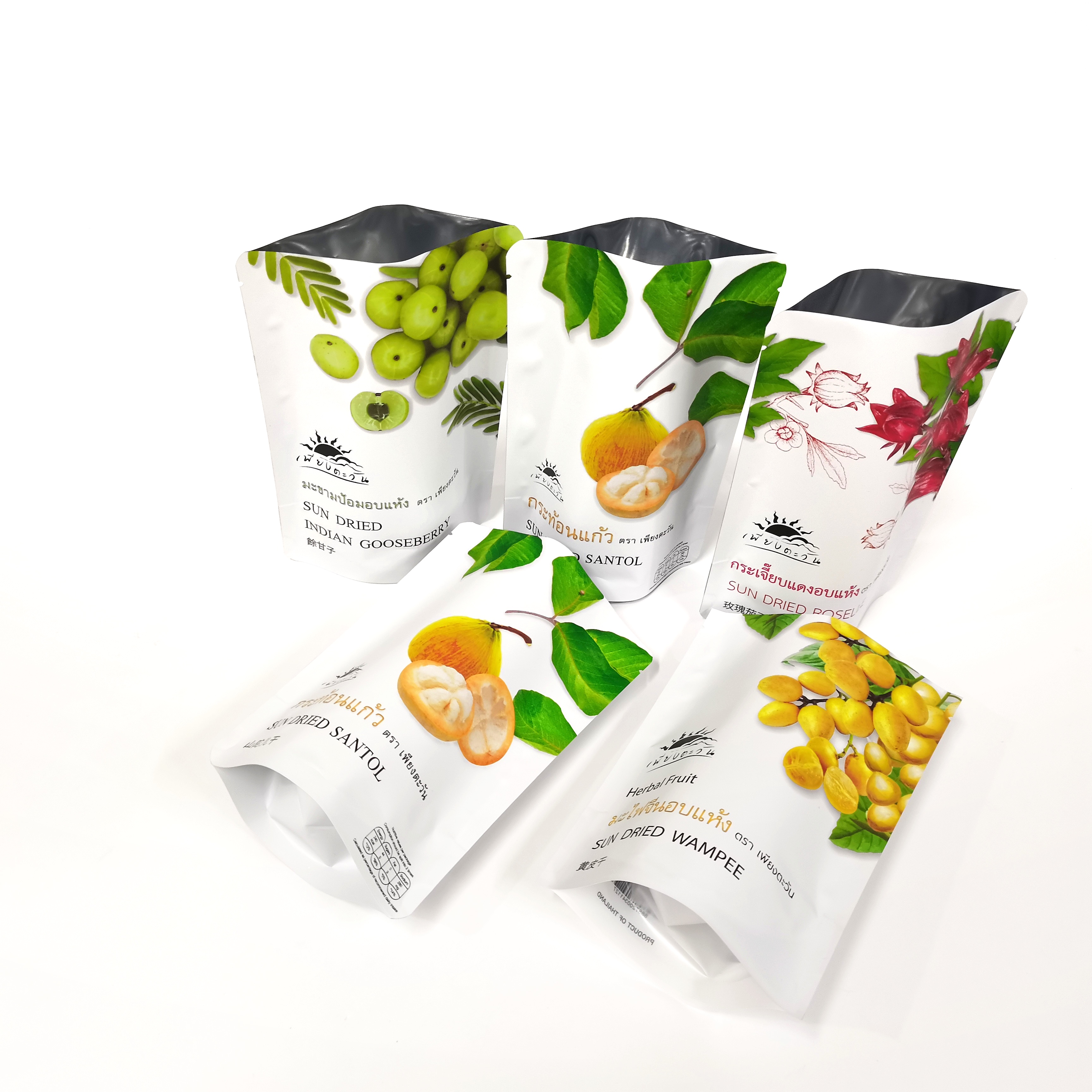
Ⅱ Process flow of plastic packaging bag color printing factory
Plastic packaging bag manufacturers custom plastic packaging bags, the general process is this, first by the design company to design your bags, and then to the plate making factory plate making, plate making is completed and arrived after the plastic packaging bag printing plant, before the real production process of plastic packaging bags, then, plastic packaging bags color printing plant process is how? Today we will learn about it, so that you can more accurately grasp the production of their products.

I.Printing.
And printing-related issues need to pay attention to is that you need to communicate in advance with the plastic packaging bag manufacturer what grade of ink used in printing, you are advised to use the best environmentally friendly certified ink, this ink printing out of plastic packaging bags with little smell, safer.
If it is transparent plastic packaging bags, you do not need to print this step, you can directly start the following process.
II.Composite
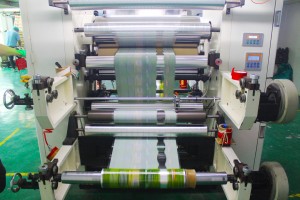
Plastic packaging bags are usually made of two or three layers of raw material film lamination, the printing layer is a layer of glossy film or matte film, and then let the printed film and other different grades of different materials of packaging film laminated together. Compounded packaging bag film also needs to ripening, that is, by adjusting the appropriate time and temperature, so that the compounded packaging film dry.
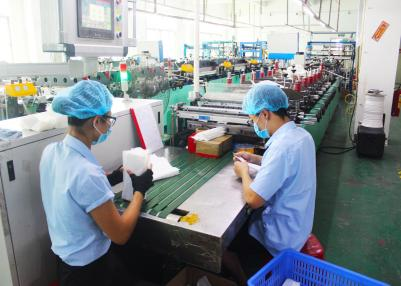
III.Inspection
At the end of the printing machine there is a special screen to check whether there are errors on the roll of film being printed, and after printing a part of the color film on the machine, a part of the sample is often torn off from the film to be checked by the color master, and at the same time handed over to the customer to check whether it is the right version, whether the color is accurate, whether there are errors not found before, etc., and then continue printing after the customer signs.
Need to raise is that, due to the monitor or print errors, sometimes the real printed color will be different from the design, but at the beginning of the printing work, if the customer is not satisfied with the printed color, at this time can also be adjusted, which is the plastic packaging bag manufacturers generally require customers to see the factory before the best way to start printing color, sign the sample reason.
IV.Pouch making
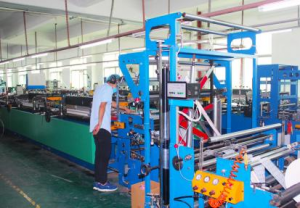
Different bag types of plastic packaging bag making different ways, three side seal, four side seal, stand-up pouches, flat bottom bags and so on a variety of plastic packaging bag bag type, is in the bag-making link to reflect. Bag making is in accordance with the size and bag type of plastic packaging bags, the printed bag roll film cutting, gluing into a complete plastic packaging bags. If you customize the plastic packaging bag roll film directly on the automatic packaging machine, then there is no bag making this link, you use the roll film and then complete the bag making and packaging, sealing and a series of work.
V.Packing & Shipping
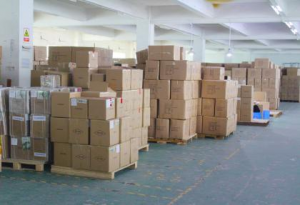
Plastic packaging bag manufacturers will be produced in accordance with a certain number of plastic packaging bags packed and sent to customers, in general, plastic packaging bag manufacturers have the nearest delivery service, but if you need to take the logistics delivery, then the packing time to consider the strength of the packing material to avoid damage to the goods.
Ending
There are all we want to share the knowledge in plastic bags, we hope this passage will help you. We are looking forward to have a cooperation with you all. Thank you for your reading.
Post time: Apr-09-2022