The basic preparation process of composite packaging bags is divided into four steps: printing, laminating, slitting, bag making, which the two processes of laminating and bag making are key processes that affect the performance of the final product.
Compounding process
Design product packaging process, in addition to the correct choice of a variety of substrates, the choice of composite adhesives is also critical, according to the use of products, composition, post-processing conditions, quality requirements for quality selection. Choose the wrong adhesive, no matter how perfect the composite processing technology, will also cause adverse consequences, as well as post-processing to reduce the force, under the composite force, leakage, broken bags and other failures.
The choice of daily chemical flexible packaging with adhesives to consider a variety of factors, in general, as a composite adhesive should meet the following conditions:
Non-toxic
No harmful extracts appear after packaging liquids.
Applicable to the temperature requirements of food storage.
good weather resistance, no yellowing and blistering, no chalking and delamination.
resistance to oils, flavors, vinegars and alcohols.
No erosion of printing pattern ink, expected to have a high affinity for ink.
In addition, resistance to erosion, the content contains a large number of spices, alcohols, water, sugar, fatty acids, etc., their properties vary, it is very likely to penetrate through the inner layer of the composite film into the adhesive layer, causing corrosion damage, resulting in the delamination of the packaging bag, damage to failure. As a result, the adhesive must have the ability to resist the erosion of the above substances, always maintain sufficient adhesive peel strength.
Plastic film composite processing methods are dry composite method, wet composite method, extrusion composite method, hot melt composite method and co-extrusion composite method and several other.
1、Dry compounding
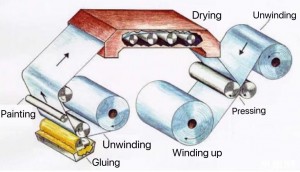
Dry lamination method is the most common method of plastic packaging lamination. Under certain conditions of temperature, tension and speed, the first substrate is uniformly filled with a layer of solvent-based adhesive (one-component hot melt adhesive or two-component reactive adhesive), after the laminating machine baking channel (divided into three areas: evaporation zone, hardening zone and the exclusion of odor zone) so that the solvent evaporates and dries, and then by the hot press rollers, in the hot press state and the second substrate (plastic film, paper or aluminum foil) bonded into a composite film.
Dry lamination can laminate any kind of film, and can replace the ability to synthesize high-performance packaging materials according to the purpose requirements depending on the contents. Therefore, in packaging, especially in the daily chemical packaging has been solved the development.
2、Wet compounding
Wet composite method is a composite substrate (plastic film, aluminum foil) coated with a layer of adhesive on the surface, in the case of adhesive is not dry, through the pressure roller and other materials (paper, cellophane) composite, and then dried after the oven into a composite film.
Wet composite process is simple, with less adhesive, low cost, high composite efficiency, and exclude residual solvent.
Wet composite laminating machine and the working principle used and dry composite method is basically the same, the difference is the first substrate coated with glue, first with the second substrate laminated composite, and then dried by the oven. Simple, less adhesive dosage, compounding speed, composite products do not contain residual solvents, pollution alternative to the environment.
3、Extrusion compounding
Extrusion compounding is the most common method of compounding process, it is the use of thermoplastic resin as raw material, the resin is heated and melted into the mold, by the die mouth instead of sheet curing of the film, immediately after compounding with another kind or two films together, and then cooled and cured. Multi-layer co-extrusion lamination is a variety of different properties of plastic resin through more than to extruder co-extrusion, into the die lamination into the film.
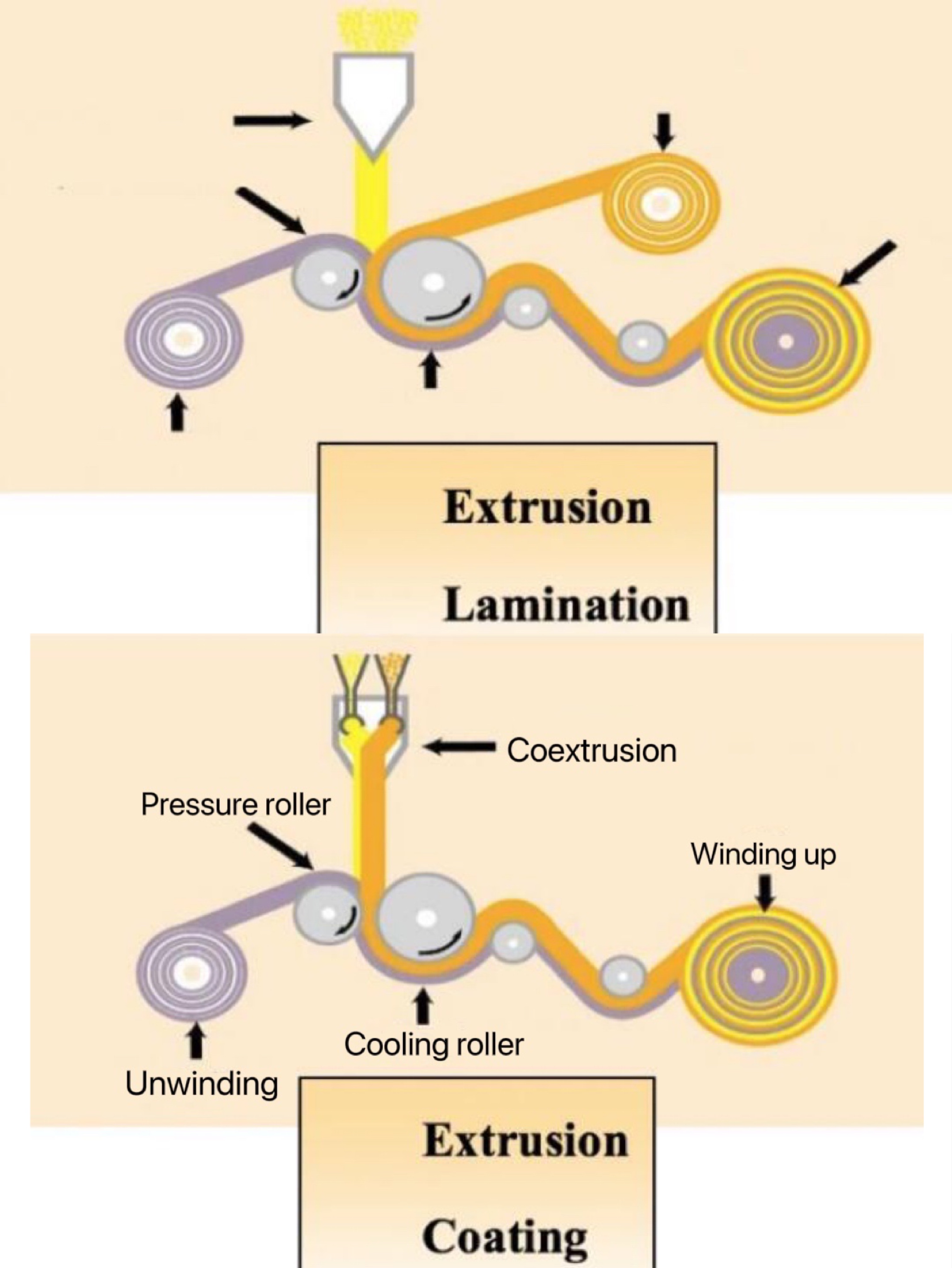
Composite materials are prone to quality problems and solutions
Compounding is an important process in the production and processing of flexible packaging, its common failures are: the production of air bubbles, low fastness to compounding, finished products wrinkled and rolled edges, composite products stretch or shrinkage, etc.. This section will focus on the analysis of wrinkling, rolled edges of the causes and methods of elimination.
1、Wrinkle phenomenon
In the dry composite failure of this phenomenon occupies a large proportion of the failure directly affects the quality of the finished product bag-making.
The main reasons for this failure are the following.
Poor quality of composite material or printing substrate itself, deviation in thickness, film rolls are loose at both ends and tight at one end due to unbalanced winding tension. If the film volume is separated from the elasticity of the large, on the machine, the film up and down and left and right placement amplitude is also relatively large because when the material enters between the hot drum and the hot press rollers, it can not be level with the hot press rollers, so it can not be squeezed flat, resulting in the finished composite wrinkled, oblique lines, resulting in product scrap. When the composite material is PE or CPP, if the thickness deviation is more than 10μm, it is also easy to wrinkle, at this time, the tension of the composite material can be increased appropriately, and the hot pressing roller can become a horizontal state for extrusion. However, it should be noted that the tension should be appropriate, too much tension is easy to make the composite material elongated, resulting in the bag mouth inward tilt. If the thickness deviation of the composite material is too large, it really can not be used, should be dealt with.
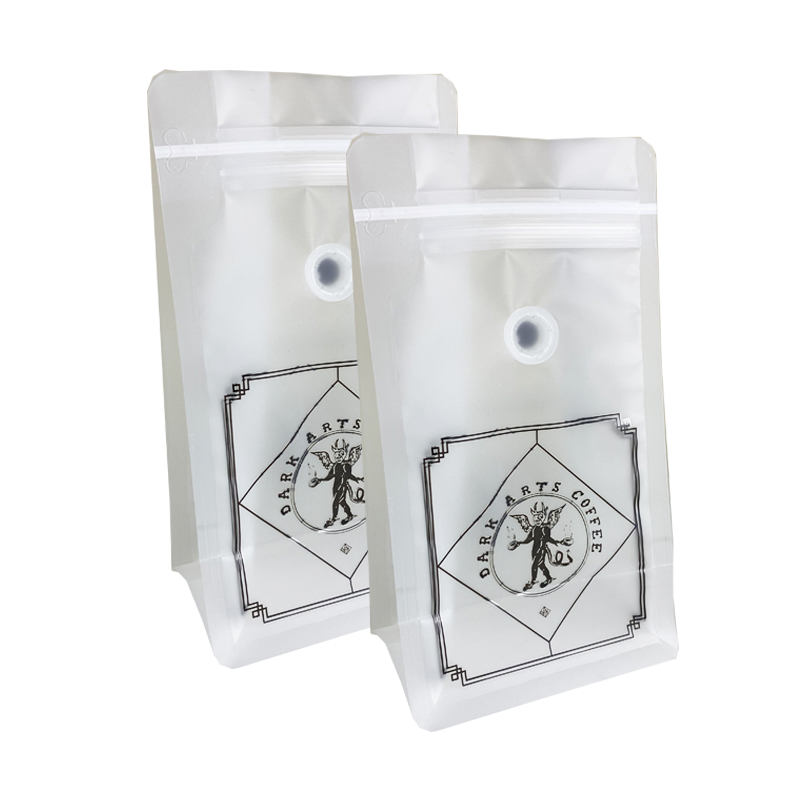
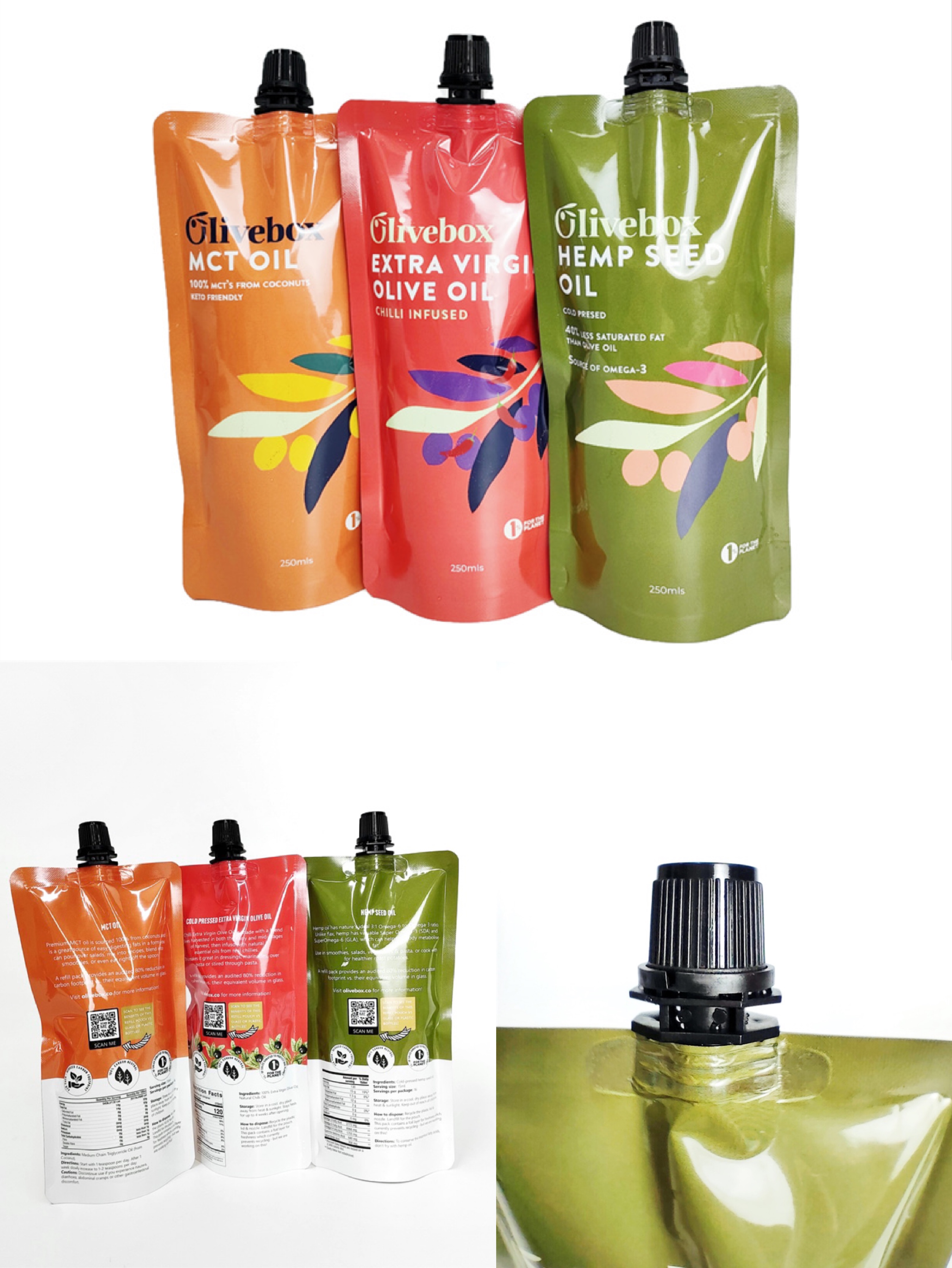
2、Composite white spots
As a result of poor ink coverage rate white spots: for composite white ink, when the ink absorption volatilization but not volatilization caused by white spots, available to improve the drying capacity of the method; if there are still white spots, the general solution is to improve the white ink coverage, such as checking the fineness of white ink, because the grinding fineness of good ink coverage rate is strong.
Adhesive instead of unevenly produced white spots: in the ink layer coated with glue, due to enter the ink will absorb the solvent, surface tension and smaller than the substrate, leveling is necessarily not as good as the light film coated with glue, glue depressions and aluminum-plated surface or aluminum foil is not a close fit, reflecting light through the bubble when encountering the section, will refract or diffuse reflection, the formation of white spots. The solution can be used to smooth out the coating with a uniform rubber roller, or increase the amount of replacement.
3、Compound bubble
Composite bubbles are generated in the following situations and corresponding methods.
Compound bubbles in the phenomenon
1. bad film, should improve the concentration of adhesive and the amount of replacement, MST, KPT surface is not easy to wet, easy to produce bubbles, especially in winter. The air bubbles on the ink, can use the method of increasing the amount of adhesive to remove.
2、The ink surface bump and bubble, should be compounded film compounding temperature and compounding pressure to increase.
3, The amount of adding glue on the surface of the ink is low, should increase the compounding roller pressure paste time and the use of smooth rollers, film preheating sufficient to reduce the compounding speed, choose good wetting glue and the correct choice of ink.
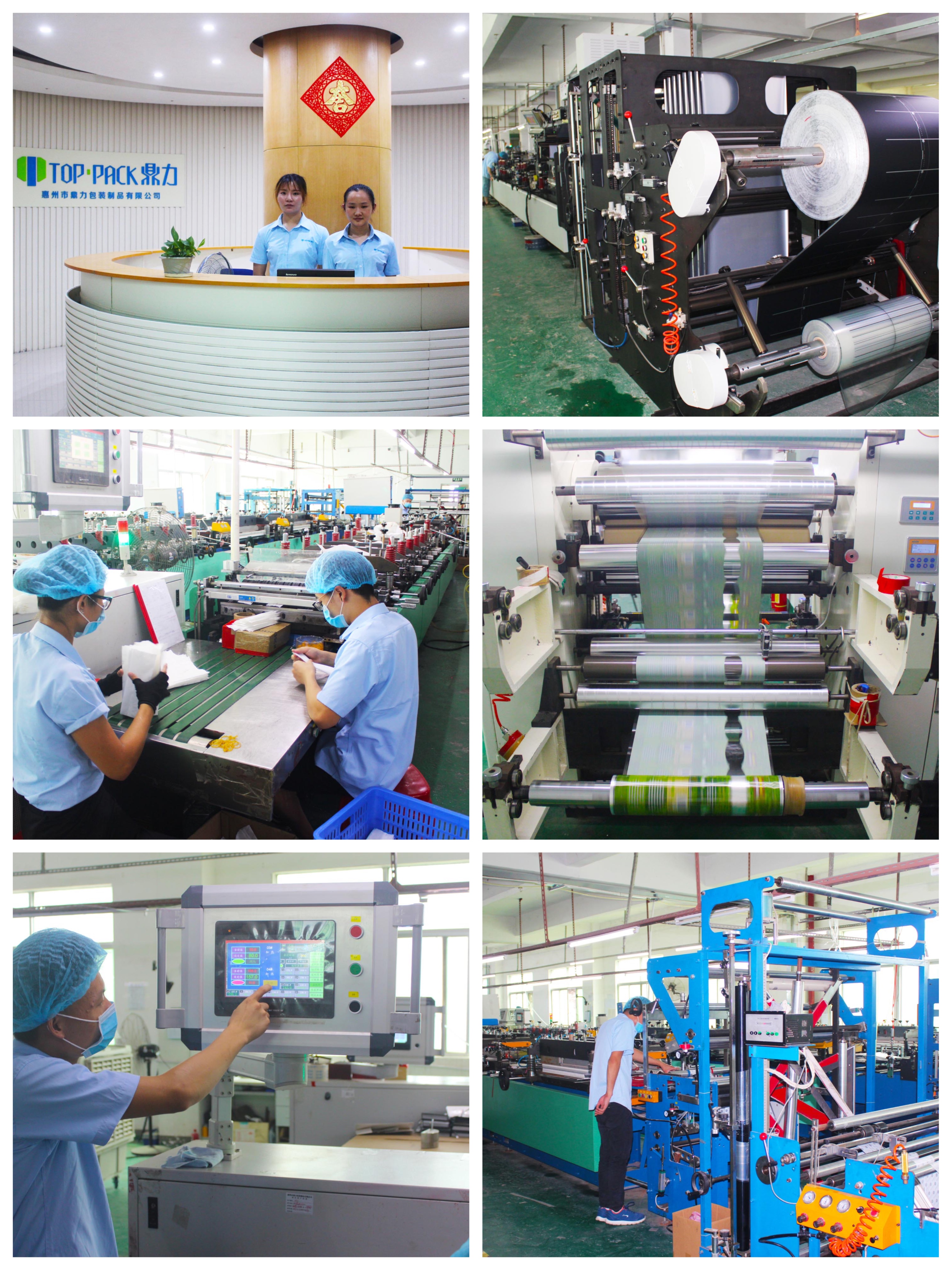
4. The additives (lubricant, antistatic agent) in the film are penetrated by the glue, so you should choose the glue with high molecular weight and fast curing, increase the concentration of glue, raise the oven temperature to fully dry the glue, and not use the film with more than 3 months placement period, because the corona treatment has been lost.
5、The temperature in winter is low, the jointing to the film and ink transfer, reset alignment effect is not good, so the operation place keep a certain temperature.
6、The drying temperature is too high, the blistering of the adhesive or the crusting of the surface skin occurs, and the inside is not dry, so the drying temperature of the adhesive should be adjusted.
7. The air is entrained between the composite rollers film, the temperature of the composite rollers should be increased and the composite angle should be decomposed (the film is thick and easy to produce bubbles when it is hard).
8、Because of the high film barrier, the CO2 gas produced by the adhesive curing, residual in the composite film, not printed at the bubble, should improve the amount of curing agent, so that the adhesive curing in dry.
9. The glycolic acid in the rubber is a good solvent for the ink filler, the rubber dissolves the ink, and there are only bubbles on the ink, which should avoid water penetration into the rubber and improve the drying temperature of the rubber to reduce the dissolution of the ink.
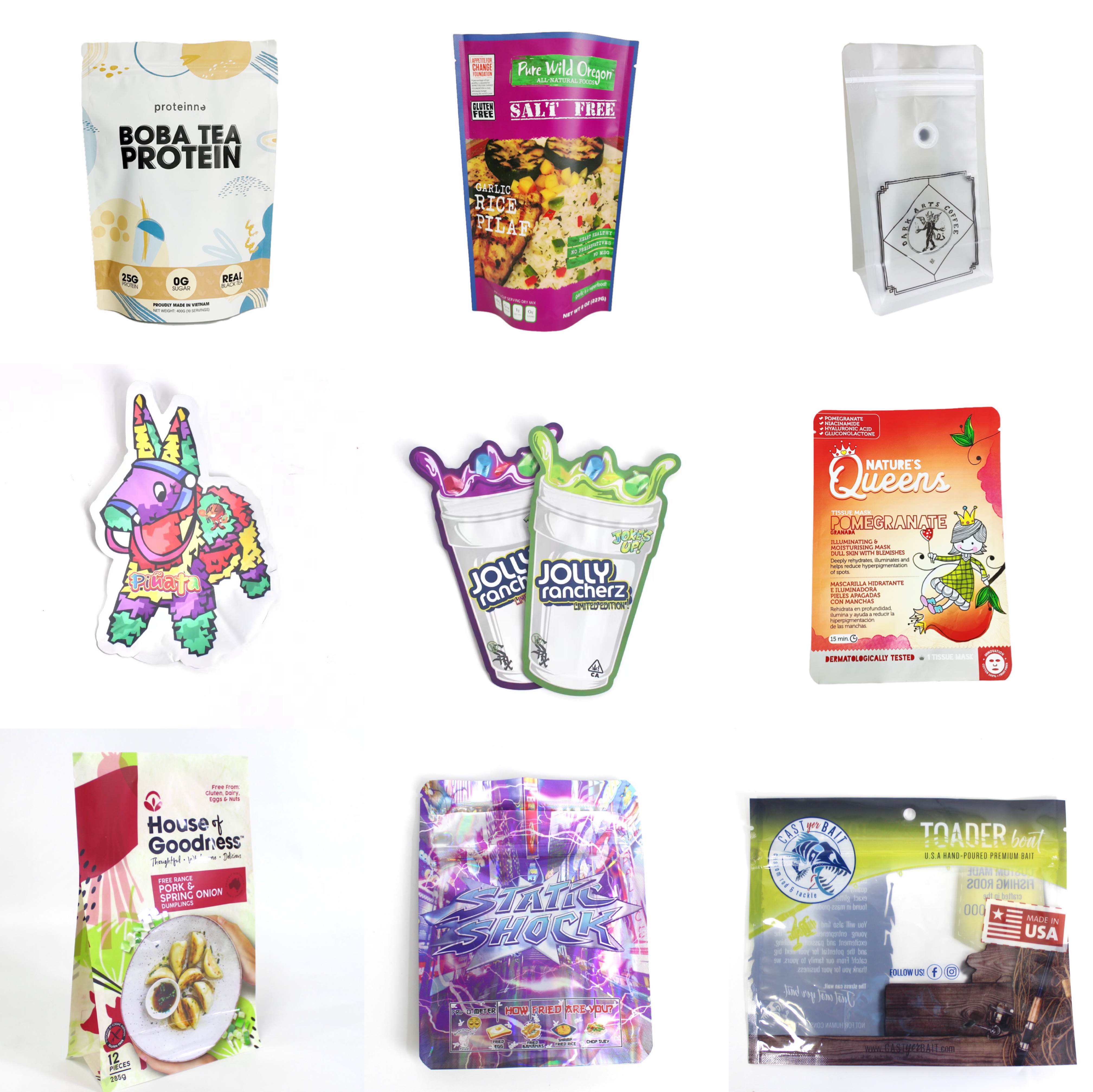
4、Poor peel strength
Peel strength is poor, is due to incomplete curing, or the amount of glue is too little, or the ink used and adhesive does not match the situation, although the curing has been completed, but between the two layers of composite film due to the lack of length has reduced force reduction.
The injection amount of glue is too small, the ratio of adhesive is reduced, the glue is deteriorated in the storage, water and alcohol are mixed in the glue, the auxiliaries in the film are precipitated, the drying or maturation process is not in place, etc., which will lead to the final composite peel strength reduction factors.
Pay attention to the proper storage of glue, the longest is not more than 1 year (tin can sealed); prevent foreign substances from entering the glue, especially water, alcohol, etc., which can cause glue failure. Film appropriate to improve the amount of glue coating; improve the drying temperature air volume, reduce the speed of compounding. The second treatment of the film surface to improve the surface tension; reduce the use of additives in the film compounding surface. All these methods can help us to improve the problem of poor peel strength of composite.
5. Heat seal bad
Compound bag heat seal bad performance and its causes are basically the following situations.
Heat sealing strength is poor. The main reasons for the phenomenon are not completely cured or heat sealing temperature is too low. Optimize the curing process or appropriately increase the sealing knife temperature can improve the problem.
Heat seal cover delamination and refractive index. The main cause of this phenomenon is the bonding is not cured. Adjust the curing time or adjust the curing agent content can improve this problem.
Poor openness / poor openness of the inner layer film. The cause of this phenomenon is too little opening agent, resulting in too much material (modifier) and sticky or greasy film surface. This problem can be improved by increasing the amount of opening agent, adjusting the amount of modifier, and avoiding secondary contamination on the film surface.
The End
Thank you for your reading,we hope that we have a opportunity to be your partners.
If you have any question want to ask, please feel free to let us know and contact us.
Contact:
E-mail Address : fannie@toppackhk.com
Whatsapp : 0086 134 10678885
Post time: Apr-01-2022