සංයුක්ත ඇසුරුම් බෑග්වල මූලික සකස් කිරීමේ ක්රියාවලිය පියවර හතරකට බෙදා ඇත: මුද්රණය, ලැමිෙන්ටින් කිරීම, කමාන්ඩ කිරීම, කම්පනය, කම්පනය, බෑවුම්, බෑග් සෑදීම, ලැමිෙන්ටින් කිරීම සහ බෑග් සෑදීමේ ක්රියාවලීන් දෙක අවසාන නිෂ්පාදනයේ ක්රියාකාරිත්වයට බලපාන ප්රධාන ක්රියාවලීන් වේ.
සංයුක්ත ක්රියාවලිය
නිෂ්පාදන ඇසුරුම්කරණ ක්රියාවලිය, විවිධ උපස්ථරවල නිවැරදි තේරීමකට අමතරව, සංයුක්ත මැලියන් තේරීම ද තීරණාත්මක ය, නිෂ්පාදන, සංයුතිය, පශ්චාත් සැකසුම් තත්වයන්, ගුණාත්මක තේරීම සඳහා ගුණාත්මක අවශ්යතා. වැරදි මැලියම් තෝරන්න, සංයුක්ත සැකසුම් තාක්ෂණය කෙතරම් පරිපූර්ණ වුවත්, අහිතකර ප්රතිවිපාක මෙන්ම සංයුක්ත බලකාය, කාන්දුවීම්, කැඩුණු බෑග් සහ වෙනත් අසාර්ථකත්වය යටතේ බලය අඩු කිරීම සඳහා පශ්චාත් සැකසුම් ද වේ.
සංයුක්ත මැලියමක් ලෙස විවිධ සාධක සලකා බැලීම සඳහා දෛනික රසායනික නම්යශීලී ඇසුරුම්කරණය වැනි තේරීම, පොදුවේ ගත් කල, සංයුක්ත මැලියම් පහත සඳහන් කොන්දේසි සපුරාලිය යුතුය:
විෂ සහිත නොවන
මත්පැන් ඇසුරුම් කිරීමෙන් පසු කිසිදු හානිකර සාරය නොපෙන්වයි.
ආහාර ගබඩාවේ උෂ්ණත්ව අවශ්යතා වලට අදාළ වේ.
හොඳ කාලගුණ ප්රතිරෝධය, කහ පැහැය සහ බිබිලි, අවුල් සහගත හා ප්රමාද නොවීම.
තෙල්, රස, විනාකිරි සහ ඇල්කොහොල් වලට ප්රතිරෝධය.
තීන්ත සඳහා ඉහළ සම්බන්ධතාවයක් ඇති බවට මුද්රණ රටාවේ තීන්තවල ඛාදනයක් නොලැබේ.
ඊට අමතරව, ඛාදනයට ප්රතිරෝධය, අන්තර්ගතයේ, කුළුබඩු, ඇල්කොහොල්, ජලය, මේද අම්ල ආදියෙහි විශාල සංඛ්යාවක් අඩංගු වේ. එහි ප්රති As ලයක් වශයෙන්, මැලියම් මගින් ඉහත ද්රව්ය ඛාදනය වීමට එරෙහි වීමේ හැකියාව තිබිය යුතුය, සෑම විටම ප්රමාණවත් මැලියම් පීල් ශක්තිය පවත්වා ගන්න.
ප්ලාස්ටික් චිත්රපට සංයුක්ත සැකසුම් ක්රම වන්නේ වියළි සංයුක්ත ක්රමය, තෙත් සංයුක්ත ක්රමය, නිස්සාරණය සංයුක්ත ක්රමය, උණුසුම් දිය ඇල්ල සංයුක්ත ක්රමය සහ සම-කැළඹීම් සංයුක්ත ක්රමය සහ තවත් කිහිපයක් සහ තවත් කිහිපයක්.
1, වියළි සංයුක්තකරණය
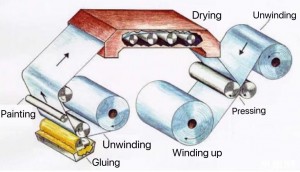
වියළි ලැමිෂන් ක්රමය ප්ලාස්ටික් ඇසුරුම්කරණ ලැමිෙන්ෂන් කිරීමේ වඩාත් පොදු ක්රමයයි. කිරි කැපීමේ යන්ත්ර ෙබ්කිං නාලිකාව (එක් අංශයකින් යුත් මැහුම් හෝ ද්වි-සංරචක කලාපීය ප්රතික්රියාශීලී) ඇතැම් ද්රව්යවල ඇතැම්මල (එක්-සම්මේලන කලාපය, ening න කලාපයක් සහ ගන්ධ කලාපය බැහැර කිරීම) එවිට ද්රාවක වාෂ්ප වී බෙදී යයි උණුසුම් මාධ්ය තත්වය සහ දෙවන උපස්ථරය (ප්ලාස්ටික් චිත්රපටය, කඩදාසි හෝ ඇලුමිනියම් තීරු) සංයුක්ත චිත්රපටයකට බැඳී ඇත.
වියළි ලැමිෙන්ටරණය ඕනෑම ආකාරයක චිත්රපටයක් ලැමිෙන්ටට් කළ හැකි අතර, අන්තර්ගතය අනුව අරමුණු අනුව ඉහළ කාර්ය සාධන ඇසුරුම් ද්රව්ය සංස්ලේෂණය කිරීමේ හැකියාව ප්රතිස්ථාපනය කළ හැකිය. එබැවින්, ඇසුරුම්කරණයේදී, විශේෂයෙන් දෛනික රසායනික ඇසුරුම්වල සංවර්ධනය විසඳා ඇත.
2,තෙත් සංයුක්තකරණය
තෙත් සංයුක්ත ක්රමය යනු සාම්ප්රදායික උපස්ථරයකි (ප්ලාස්ටික් චිත්රපට, ඇලුමිනියම් තීරු), මැලියම් සම්බන්ධයෙන්, පීඩන රෝලර් සහ වෙනත් ද්රව්ය (කඩදාසි, සෙලෝපේන්) සංයුක්ත වන අතර පසුව සංයුක්ත චිත්රපටයකට උඳුනෙන් පසුව වියළා ගන්න.
තෙත් සංයුක්ත ක්රියාවලිය සරලයි, අඩු මැලියම්, අඩු වියදම්, ඉහළ සංයුක්ත කාර්යක්ෂමතාවයක් සහ අවශේෂ ද්රාවක බැහැර කිරීම.
තෙත් සංයුක්ත ලැමිෙන්ටින් යන්ත්රය සහ භාවිතා කරන හා වියලි සංයුක්ත ක්රමවේදය මූලික වශයෙන් සමාන වන අතර, මැලියම් සමග, පළමුව දෙවන උපස්ථර ලැමිෙන්ටඩ් සංයුක්ත සංයුක්ත සංයුක්තය සමඟ, පසුව උඳුන අසල වියළා ගන්න. සරල, අඩු මැලියම් මාත්රාව, සංයුක්ත වේගය, සංයුක්ත නිෂ්පාදනවල අවශේෂ ද්රාවක, පරිසරයට දූෂණය විකල්පයක් අඩංගු නොවේ.
3, නිස්සාරණය සංයුක්ත කිරීම
නිස්සාරණ සංයෝග යනු සංයුක්ත ක්රියාවලියේ වඩාත් පොදු ක්රමයයි, එය රාව් ද්රව්යයක් ලෙස රව් ද්රව්ය ලෙස රණවිත් මුඛය, දුම්පානය කුටි තුළට, පසුව වෙනත් වර්ගයේ හෝ චිත්රපට දෙකක් එකට එකතු වී සුව කර සුවය ලබා ඇත. බහු ස්ථර සම-නිස්සාරණ ලැමිෙන්ෂන් යනු මිනීරු සම-නිස්සාරණයට වඩා, රූගත කිරීම්වලට වඩා චිත්රපටයට මරණීය දණ්ඩනය, ඩයි මැනේරණයට වඩා වැඩි ප්රමාණයක් ප්ලාස්ටික් දුම්මලවල විවිධාකාරයකි.
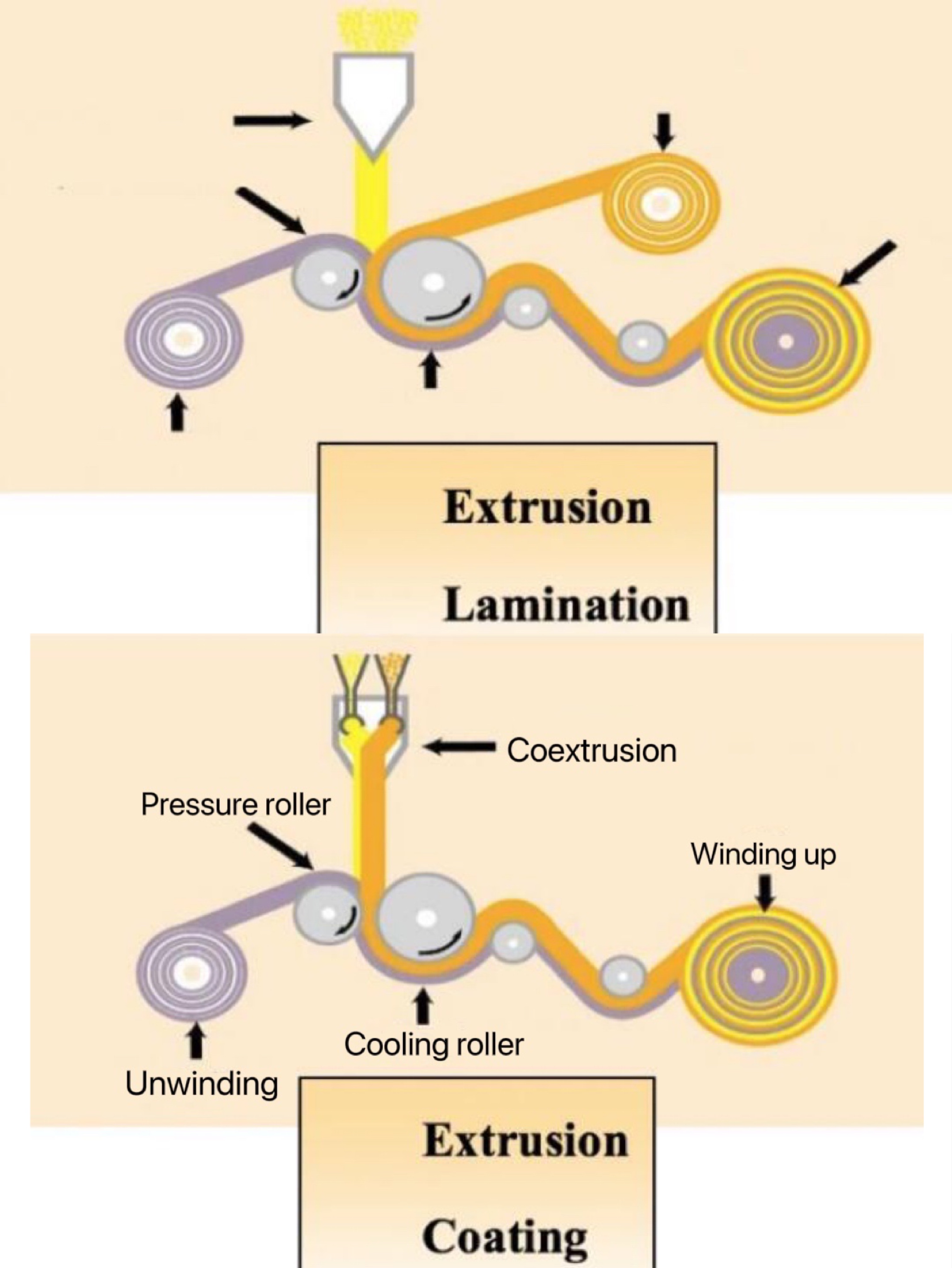
සංයුක්ත ද්රව්ය ගුණාත්මක ගැටළු සහ විසඳුම් වලට ගොදුරු වේ
නම්යශීලී ඇසුරුම්කරණය, එහි පොදු අසාර්ථකත්වය, එහි පොදු අසාර්ථකත්වය, එහි පොදු අසාර්ථකත්වය, සංක්රමණය වූ සහ රෝල් කරන ලද දාර, සංක්රමණය සහ රෝල් කරන ලද දාර, සංක්රමණය සහ රෝල් කරන ලද දාර, හැකිලී ගිය දාර, රැළි සහිත දාර, රැළි සහිත දාර, රෝල් කරන ලද නිෂ්පාදන, රැළි සහ රෝල් කරන ලද දාර, රැළි සහිත දාර, රැළි සහිත දාර, සංක්රමණය සහ රෝල් කරන ලද දාර, සංක්රමණය සහ රෝල් කරන ලද දාර, සංක්රමණය සහ රෝල් කරන ලද දාර, සංක්රමණය සහ රෝල් කරන ලද දාර කිරීම, සංචිත නිෂ්පාදන;
1, රැළි සංසිද්ධිය
මෙම සංසිද්ධියේ වියළි සංයුක්ත අසමත් වීමෙහි අසාර්ථකත්වයේ විශාල ප්රතිශතයක් සනාථ කරයි නිමි භාණ්ඩ බෑග් සෑදීමේ ගුණාත්මක භාවයට සෘජුවම බලපායි.
මෙම අසාර්ථකත්වයට ප්රධාන හේතු පහත දැක්වේ.
සංයුක්ත ද්රව්යවල ගුණාත්මකභාවය හෝ මුද්රණයේ ගුණාත්මකභාවය, thickness ණකම, thickness ණකම, චිත්රපට රෝල්ස් අසමසම සුළං ආතතිය හේතුවෙන් එක් කෙළවරකින් එක කෙළවරක ලිහිල් වේ. චිත්රපටයේ පරිමාව විශාල වශයෙන්, යන්ත්රයේ ප්රත්යාස්ථතාවයෙන් වෙන්ව ඇත්නම්, චිත්රපටය ඉහළට හා පහළට හා වම් සහ දකුණු ස්ථානගත කිරීමේ විස්තාරය සාපේක්ෂව විශාල බැවින් එය පැතලි විය නොහැක සංයුක්ත ද්රව්ය PE හෝ CPP වන විට, thickness ණකම අපගමනය 10μm ට වඩා වැඩි නම්, මේ අවස්ථාවේ දී, මෙම අවස්ථාවේදී, සංයුක්ත ද්රව්යයේ ආතතිය උචිත ලෙස වැඩි කළ හැකි අතර, උණුසුම් තද කිරීමේ රෝලර්, නිස්සාරණය සඳහා තිරස් තත්වයක් බවට පත්විය හැකිය. කෙසේ වෙතත්, ආතතිය උචිත විය යුතු බව සැලකිල්ලට ගත යුත්තේ සංයුක්ත ද්රව්ය දිගටි සෑදීම සඳහා අධික ආතතියක් පහසු වන බවයි. සංයුක්ත ද්රව්යවල thickness ණකම පාලනය කිරීම ඉතා විශාල නම්, එය සැබවින්ම භාවිතා කළ නොහැක, සමඟ ගනුදෙනු කළ යුතුය.
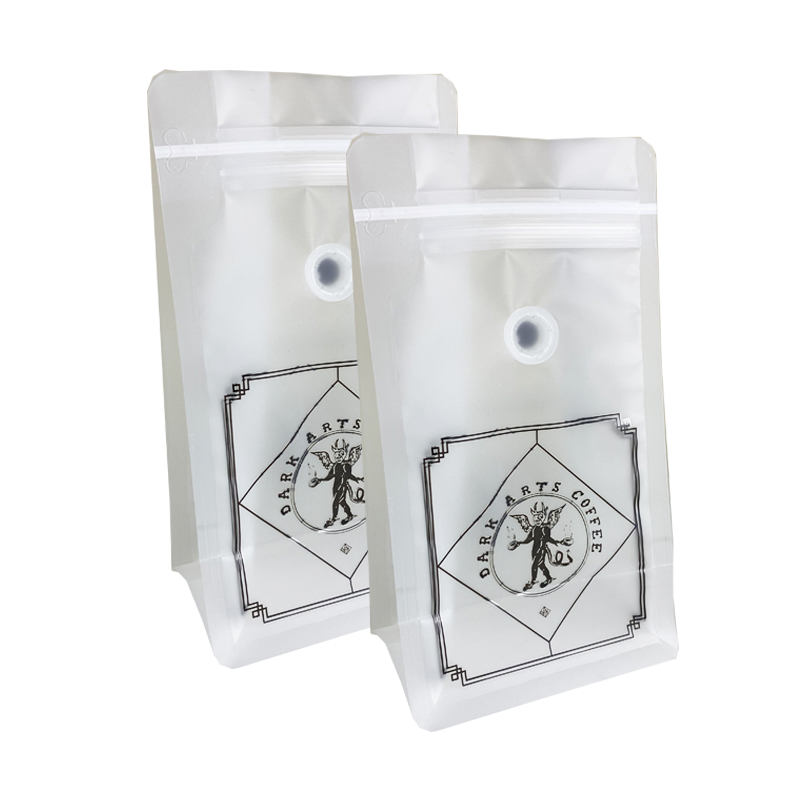
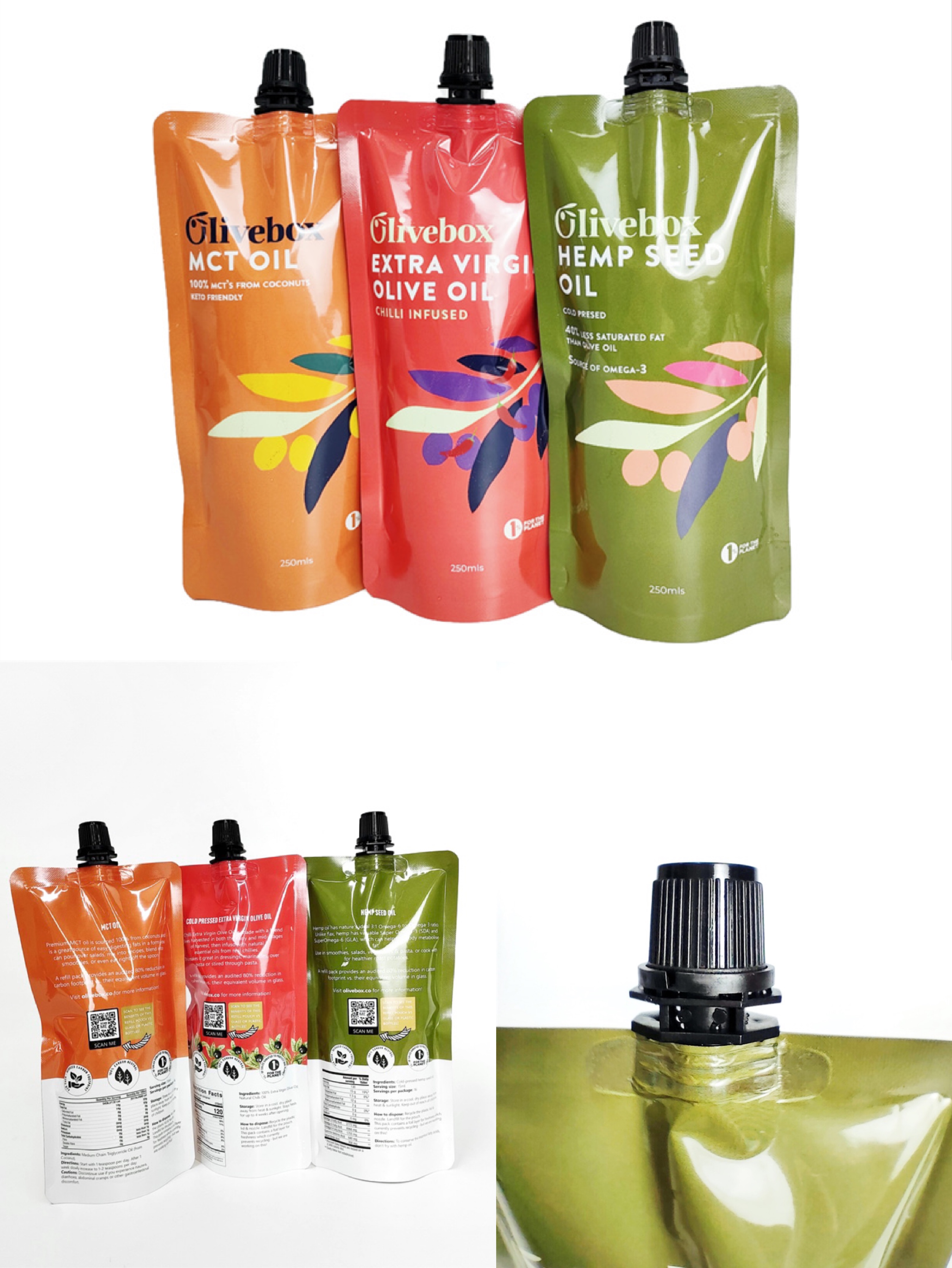
2, සංයුක්ත සුදු ලප
දුර්වල තීන්ත ආවරණ අනුපාතය අනුව සුදු ලප අනුපාතය: තීන්ත අවශෝෂණ අස්ථාවරයෙකු සඳහා, තීන්ත අවශෝෂණ අස්ථාවරත්වය සඳහා, ක්රමයේ වියළීමේ ධාරිතාව වැඩි දියුණු කිරීම සඳහා අස්ථාවර වීම; තවමත් සුදු ලප තිබේ නම්, සාමාන්ය විසඳුම නම් සුදු තීන්තවල සෙන්පයක් පරීක්ෂා කිරීම වැනි සුදු තීන්ත ආවරණය වැඩි කිරීමයි, මන්ද හොඳ තීන්ත ආවරණ අනුපාතය ශක්තිමත් වේ.
අසමාන ලෙස නිපදවන සුදු ලප වෙනුවට මැලියම්: තීන්ත තාලය ආලේප කර ඇති අතර, මැලියම්, මතුපිට ආතතිය සහ ඇලුමිනියම් තීරු ආලෝකය විහිදුවනු ලැබේ පරාවර්තනය, සුදු ලප සෑදීම. ඒකාකාර රබර් රෝලරයක් සහිත ආලේපනය සුමට කිරීම සඳහා විසඳුම භාවිතා කළ හැකිය, නැතහොත් ආදේශන ප්රමාණය වැඩි කරන්න.
3, සංයුක්ත බුබුල
පහත දැක්වෙන තත්වයන් තුළ සංයුක්ත බුබුලු සහ ඊට අනුරූප ක්රමවල ජනනය වේ.
සංසිද්ධියේ ඇති බුබුලු
1. නරක චිත්රපටය, මැලියම් සාන්ද්රණය වැඩි දියුණු කළ යුතු අතර, ආදේශන ප්රමාණය තෙත් කිරීම, විශේෂයෙන් ශීත in තුවේ දී බුබුලු නිපදවීමට පහසුය. තීන්ත මත වාතය බුබුලු,පුළුවන්ඉවත් කිරීමට මැලියම් ප්රමාණය වැඩි කිරීමේ ක්රමය භාවිතා කරන්න.
2,ඇට් මතුපිට ගැටිත්ත හා බුබුල, චිත්රපට සංයුක්ත උෂ්ණත්වය උරාංශ හා වැඩි කිරීමට හේතු වන පීඩනය සංයුක්ත කළ යුතුය.
3, තීන්ත මතුපිටින් මැලියම් එකතු කිරීම අඩු වන අතර, සංයුක්ත රෝලර් පීඩන අලස කාලය වැඩි කළ යුතුය. සුමට රෝලර් භාවිතය, සංයුක්ත වේගය අඩු කිරීම සඳහා, හොඳ තෙත් මැලියම් සහ තීන්තවල නිවැරදි තේරීම තෝරන්න.
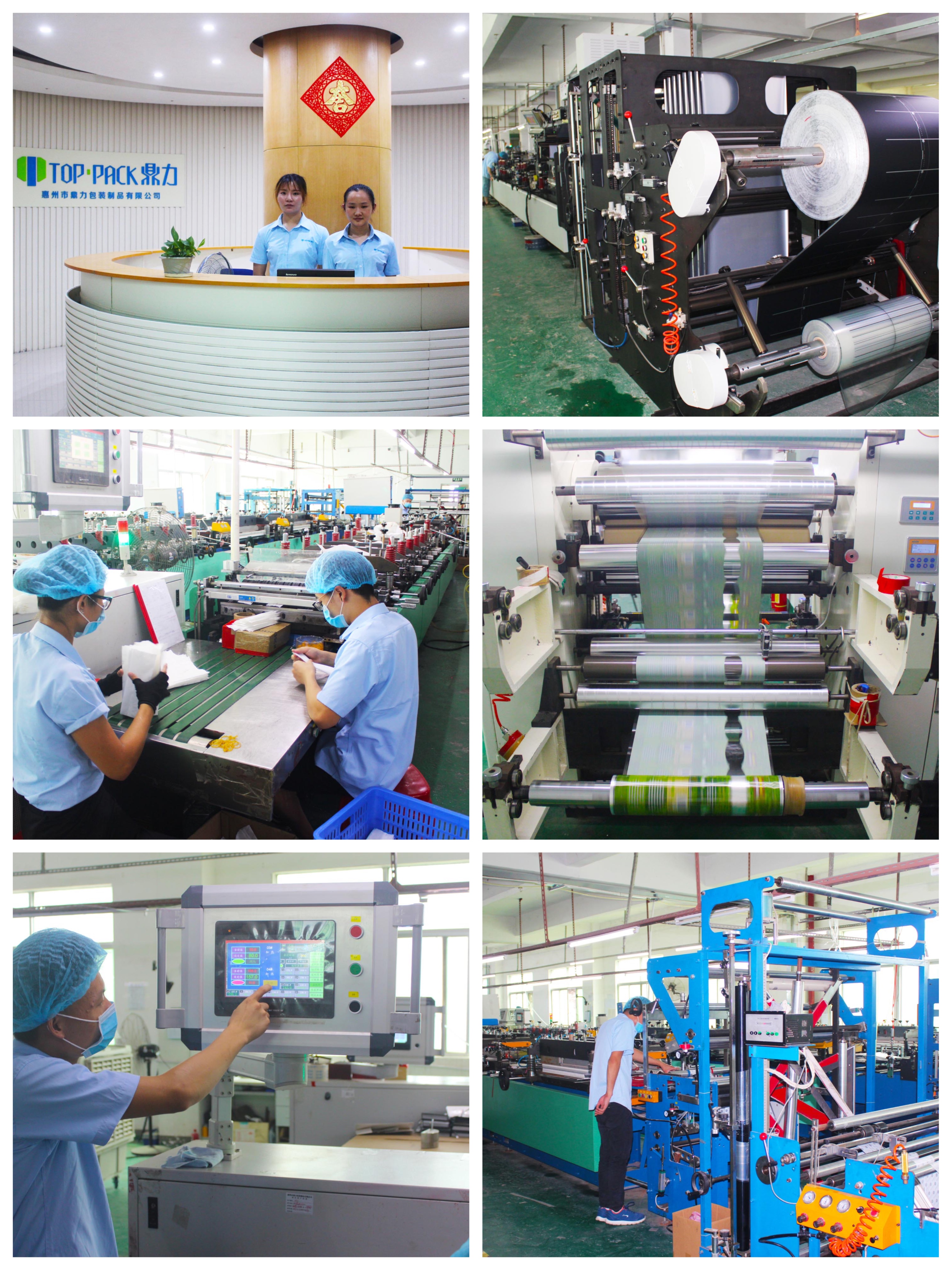
4. චිත්රපටයේ ආකලන (ලිහිසි (ලිහිසි තෙල්, ප්රති-දෘෂ්ටාසවල) මැලියම් සාන්ද්රණය, මැලියම් සාන්ද්රණය, මැලියම් සාන්ද්රණය, කොරෝනා ප්රතිකාර නැති වී ඇති බැවින්, මාස 3 කට වඩා වැඩි කාලයක් ගත කරන්න.
5,ශීත in තුවේ දී ඇති උෂ්ණත්වය අඩු, චිත්රපටයට සහ තීන්ත හුවමාරුවට ඒකාබද්ධ කිරීම, පෙළගැස්වීමේ බලපෑම නැවත සැකසීම හොඳ නැත, එබැවින් මෙහෙයුම් ස්ථානය යම් උෂ්ණත්වයක් පවත්වා ගෙන යයි.
6,වියළීම වැඩියි, මැලියම් හෝ මතුපිට සමේ කබොල පැහැර ගැනීම හෝ පෘෂ් ත්වයේ වියළී නැත, එබැවින් මැලියම් වල වියළන උෂ්ණත්වය සකස් කළ යුතුය.
7. සංයුක්ත රෝලර් චිත්රපටය අතර වාතය ඇතුල් වන අතර සංයුක්ත රෝලර්වල උෂ්ණත්වය වැඩි කළ යුතු අතර සංයුක්ත කෝණය දිරාපත් විය යුතුය.
8,ඉහළ චිත්රපට බාධකයක් නිසා, බුබුලෙන් මුද්රණය නොකෙරේ, සංයුක්ත චිත්රපටයේ මැලියම් චිත්රපටයේ මැලියම් සුවපහසුව විසින් නිපදවන CO2 වායුව සුව කිරීමේ නියෝජිතයාගේ ප්රමාණය වැඩි දියුණු කළ යුතුය.
9. රබර් වල ඇති ග්ලයිකෝලික් අම්ලය තීන්ත පිරවූයේ හොඳ ද්රාවකය, රබර් තීන්ත විසුරුවා හැරේ, රබර් වලට ජලය විනිවිද යාම වළක්වා ගත යුතු අතර තීන්ත විසුරුවා හැරීම අඩු කිරීම සඳහා රබර් වල වියළන උෂ්ණත්වය රබර් වල වියළන උෂ්ණත්වය වැඩි දියුණු කළ යුතුය.
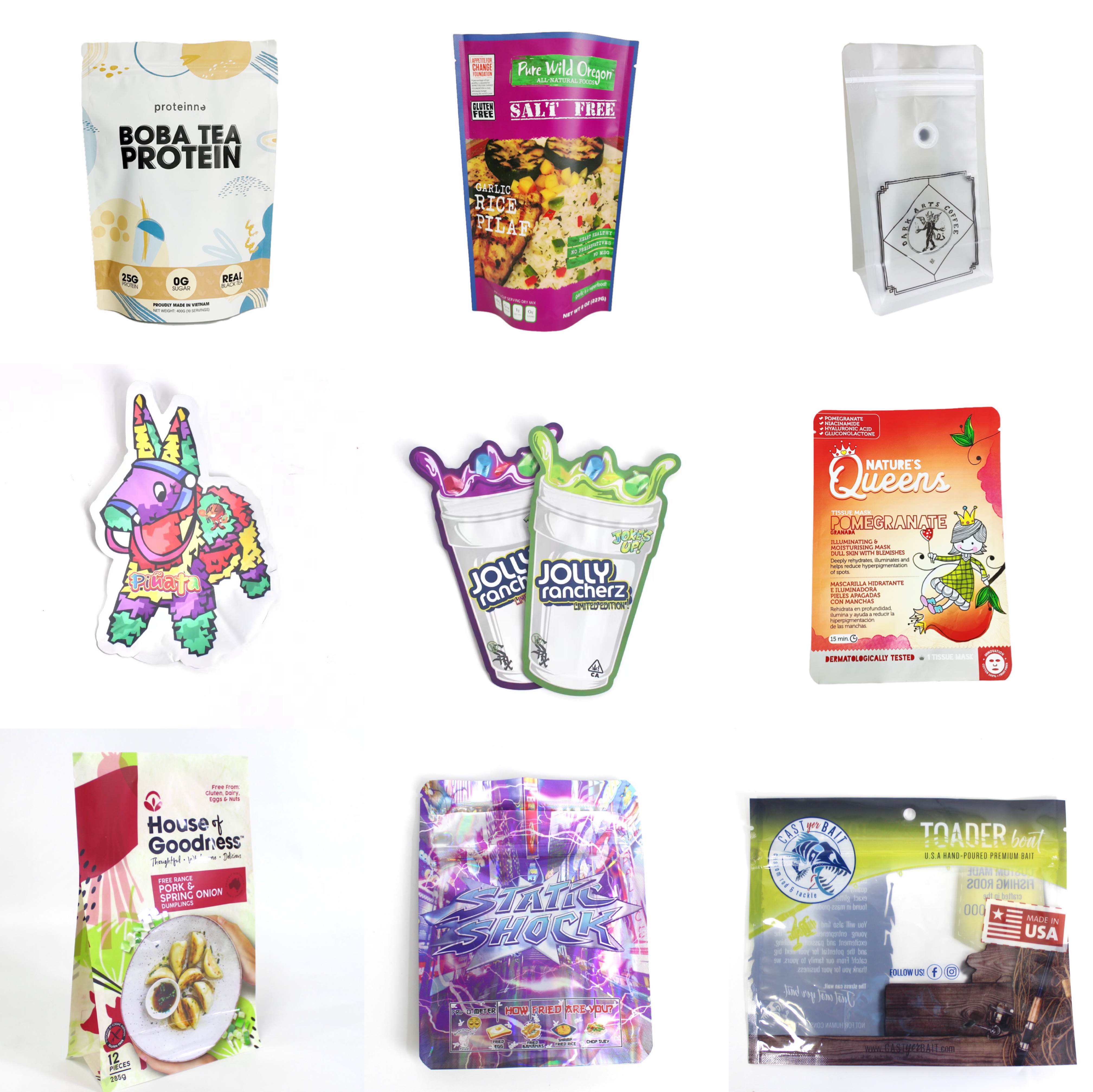
4, දුප්පත් පීල් ශක්තිය
පීල් ශක්තිය දුප්පත්, අසම්පූර්ණ සුව කිරීම නිසා, නැතහොත් මැලියම් ප්රමාණය ඉතා අඩු හෝ මැලියම් ප්රමාණය හෝ කල් දැමීමේ ප්රමාණය අඩු වුවද, දිග නොමැතිකම හේතුවෙන් සංයුක්ත චිත්රපට ස්ථර දෙක අතරට නොගැලපේ.
මැලියම්වල එන්නත් ප්රමාණය ඉතා කුඩා බැවින් මැලියම් අනුපාතය අඩු වී ඇති අතර, මැලියම් තුළ මැලියම් පිරිහී යයි, වියළීම, වියළීම හෝ මේල් ශක්තිය අඩුකිරීමේ සාධක වේ.
මැලියම් නිසි ලෙස ගබඩා කිරීම කෙරෙහි අවධානය යොමු කරන්න, දිගම, වසර 1 කට වඩා වැඩි නොවේ (ටින් මුද්රා තැබිය හැකිය); මැලියම් අසමත් වීමට හේතු විය හැකි විදේශීය ද්රව්ය මැලියම්, විශේෂයෙන් ජලය, මත්පැන් ආදිය තුළට ඇතුළු වීම වළක්වයි. මැලියම් ආලේපනය වැඩිදියුණු කිරීම සඳහා සුදුසු චිත්රපටය; වියළීම උෂ්ණත්ව වායු පරිමාව වැඩි දියුණු කරන්න, සංයුක්ත වේගය අඩු කරන්න. මතුපිට ආතතිය වැඩි දියුණු කිරීම සඳහා චිත්රපට මතුපිට දෙවන ප්රතිකාර කිරීම; සංයුක්ත පෘෂ් on ය තුළ ආකලන භාවිතා කිරීම අඩු කරන්න. සාම්ප්රංශයේ දුප්පත් පීල් ශක්තිය පිළිබඳ ගැටළුව වැඩිදියුණු කිරීමට මේ සියලු ක්රම අපට උපකාරී වේ.
5. තාප මුද්රාව නරකයි
සංයුක්ත බෑග් තාප මුද්රාව නරක කාර්ය සාධනය සහ එහි හේතු මූලික වශයෙන් පහත සඳහන් තත්වයන් වේ.
තාප මුද්රා තැබීමේ ශක්තිය දුර්වලයි. සංසිද්ධිය සඳහා ප්රධාන හේතු සම්පුර්ණයෙන්ම සුව වී හෝ තාප මුද්රා දැමීමේ උෂ්ණත්වය ඉතා අඩුය. සුව කිරීමේ ක්රියාවලිය ප්රශස්ත කිරීම හෝ මුද්රා තැබීමේ පිහි උෂ්ණත්වය උචිත ලෙස වැඩි කිරීම ගැටළුව වැඩි දියුණු කළ හැකිය.
රත් මුද්රා ආවරණ ප්රමාණ සහ වර්තන දර්ශකය. මෙම සංසිද්ධියට ප්රධාන හේතුව වන්නේ බන්ධනය සුවපත් නොවේ. සුව කිරීමේ කාලය සකස් කරන්න හෝ සුව කිරීමේ නියෝජිත අන්තර්ගතයට මෙම ගැටළුව වැඩි දියුණු කළ හැකිය.
දුර්වල ස්ථර පටලයේ දුර්වල විවෘතභාවය / විවෘතව සිටීම. මෙම සංසිද්ධිය සඳහා හේතුව විවෘත ආරම්භක කාරකයක් වන අතර එහි ප්රති ulted ලයක් ලෙස අධික ද්රව්යමය (විකරණකාරකය) සහ ඇලෙන සුළු හෝ ආලේපිත චිත්රපට මතුපිට. ආරම්භක නියෝජිතයාගේ ප්රමාණය වැඩි කිරීමෙන් මෙම ගැටළුව වැඩිදියුණු කළ හැකි අතර, විකරණකාරකයේ ප්රමාණය වෙනස් කරමින්, චිත්රපට මතුපිටින් ද්විතියික අපවිත්ර වීම වළක්වා ගත හැකිය.
අවසානය
ඔබගේ කියවීමට ස්තූතියි, ඔබේ හවුල්කරුවන් වීමට අපට අවස්ථාවක් ලැබෙනු ඇතැයි අපි බලාපොරොත්තු වෙමු.
ඔබට කිසියම් ප්රශ්නයක් ඇත්නම්, කරුණාකර අපට දැනුම් දීමට සහ සම්බන්ධ වීමට කරුණාකර නිදහස් වන්න.
අමතන්න:
ඊතැපැල් ලිපිනය :fannie@toppackhk.com
WhatsApp: 0086 134 1067885
පශ්චාත් කාලය: අප්රේල් -01-2022