கலப்பு பேக்கேஜிங் பைகளின் அடிப்படை தயாரிப்பு செயல்முறை நான்கு படிகளாக பிரிக்கப்பட்டுள்ளது: அச்சிடுதல், லேமினேட்டிங், வெட்டுதல், பை தயாரித்தல், இது லேமினேட்டிங் மற்றும் பை தயாரிக்கும் இரண்டு செயல்முறைகள் இறுதி உற்பத்தியின் செயல்திறனை பாதிக்கும் முக்கிய செயல்முறைகள்.
கூட்டு செயல்முறை
தயாரிப்பு தயாரிப்பு பேக்கேஜிங் செயல்முறை, பலவிதமான அடி மூலக்கூறுகளின் சரியான தேர்வுக்கு கூடுதலாக, கலப்பு பசைகளின் தேர்வும் முக்கியமானது, தயாரிப்புகள், கலவை, பிந்தைய செயலாக்க நிலைமைகள், தரத் தேர்வுக்கான தரத் தேவைகள் ஆகியவற்றின் படி. கூட்டு செயலாக்க தொழில்நுட்பம் எவ்வளவு சரியானதாக இருந்தாலும், தவறான பிசின் தேர்வு, மற்றும் கலப்பு சக்தி, கசிவு, உடைந்த பைகள் மற்றும் பிற தோல்விகளின் கீழ், சக்தியைக் குறைக்க பிந்தைய செயலாக்கத்தையும் ஏற்படுத்தும்.
தினசரி வேதியியல் நெகிழ்வான பேக்கேஜிங்கை பசைகள் கொண்ட பல்வேறு காரணிகளைக் கருத்தில் கொள்ள, பொதுவாக, ஒரு கலப்பு பிசின் பின்வரும் நிபந்தனைகளை பூர்த்தி செய்ய வேண்டும்:
நச்சுத்தன்மையற்ற
பேக்கேஜிங் திரவங்களுக்குப் பிறகு தீங்கு விளைவிக்கும் சாறுகள் எதுவும் தோன்றவில்லை.
உணவு சேமிப்பகத்தின் வெப்பநிலை தேவைகளுக்கு பொருந்தும்.
நல்ல வானிலை எதிர்ப்பு, மஞ்சள் மற்றும் கொப்புளங்கள் இல்லை, சுண்ணாம்பு மற்றும் நீக்குதல் இல்லை.
எண்ணெய்கள், சுவைகள், வினிகர் மற்றும் ஆல்கஹால்களுக்கு எதிர்ப்பு.
அச்சிடும் முறை மை அரிப்பு இல்லை, மை மீது அதிக ஈடுபாடு இருக்கும் என்று எதிர்பார்க்கப்படுகிறது.
கூடுதலாக, அரிப்புக்கு எதிர்ப்பு, உள்ளடக்கத்தில் ஏராளமான மசாலாப் பொருட்கள், ஆல்கஹால், நீர், சர்க்கரை, கொழுப்பு அமிலங்கள் போன்றவை உள்ளன, அவற்றின் பண்புகள் வேறுபடுகின்றன, இது கலப்பு படத்தின் உள் அடுக்கு வழியாக பிசின் அடுக்குக்குள் ஊடுருவக்கூடும், இதனால் அரிப்பு சேதத்தை ஏற்படுத்துகிறது, இதன் விளைவாக பேக்கேஜிங் பையை நீக்குகிறது, செயலிழந்தது. இதன் விளைவாக, பிசின் மேற்கண்ட பொருட்களின் அரிப்பை எதிர்க்கும் திறனைக் கொண்டிருக்க வேண்டும், எப்போதும் போதுமான பிசின் தலாம் வலிமையை பராமரிக்க வேண்டும்.
பிளாஸ்டிக் ஃபிலிம் கலப்பு செயலாக்க முறைகள் உலர் கலப்பு முறை, ஈரமான கலப்பு முறை, வெளியேற்ற கலப்பு முறை, சூடான உருகும் கலப்பு முறை மற்றும் இணை வெளியேற்றம் கலப்பு முறை மற்றும் பல.
1 、 உலர் கலவை
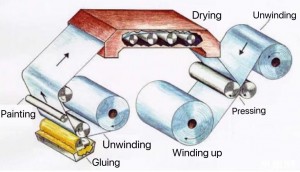
உலர் லேமினேஷன் முறை பிளாஸ்டிக் பேக்கேஜிங் லேமினேஷனின் மிகவும் பொதுவான முறையாகும். வெப்பநிலை, பதற்றம் மற்றும் வேகம் ஆகியவற்றின் சில நிபந்தனைகளின் கீழ், முதல் அடி மூலக்கூறு கரைப்பான் அடிப்படையிலான பிசின் (ஒரு-கூறு சூடான உருகும் பிசின் அல்லது இரண்டு-கூறு எதிர்வினை பிசின்), லேமினேட்டிங் இயந்திர பேக்கிங் சேனலுக்குப் பிறகு (மூன்று பகுதிகளாக பிரிக்கப்பட்டுள்ளது: ஆவியாதல் மண்டலம், ஹாட்ஸிங் மண்டலம் மற்றும் ஓடோர்கள் மற்றும் ட்ரோவென்ட்ஸ் மற்றும் ட்ரோவென்ட்ஸ் மற்றும் ட்ரோவென்ட்ஸ் மற்றும் ட்ரோவார்ஸ் மற்றும் டர்பென்ட்ஸ் மற்றும் ட்ரைஸ்கள் இரண்டாவது அடி மூலக்கூறு (பிளாஸ்டிக் படம், காகிதம் அல்லது அலுமினியத் தகடு) ஒரு கலப்பு படத்தில் பிணைக்கப்பட்டுள்ளது.
உலர் லேமினேஷன் எந்தவொரு படத்தையும் லேமினேட் செய்யலாம், மேலும் உள்ளடக்கங்களைப் பொறுத்து நோக்கத் தேவைகளுக்கு ஏற்ப உயர் செயல்திறன் கொண்ட பேக்கேஜிங் பொருட்களை ஒருங்கிணைக்கும் திறனை மாற்ற முடியும். எனவே, பேக்கேஜிங்கில், குறிப்பாக தினசரி வேதியியல் பேக்கேஜிங்கில் வளர்ச்சி தீர்க்கப்பட்டுள்ளது.
2、ஈரமான கலவை
ஈரமான கலப்பு முறை என்பது மேற்பரப்பில் பிசின் ஒரு அடுக்குடன் பூசப்பட்ட ஒரு கலப்பு அடி மூலக்கூறு (பிளாஸ்டிக் படம், அலுமினியத் தகடு) ஆகும், பிசின் விஷயத்தில், பிரஷர் ரோலர் மற்றும் பிற பொருட்கள் (காகிதம், செலோபேன்) கலப்பு மூலம் உலரவில்லை, பின்னர் அடுப்புக்குப் பிறகு ஒரு கலப்பு படத்தில் உலர்த்தப்படுகிறது.
ஈரமான கலப்பு செயல்முறை எளிதானது, குறைந்த பிசின், குறைந்த செலவு, அதிக கலப்பு செயல்திறன் மற்றும் மீதமுள்ள கரைப்பான் விலக்குகிறது.
ஈரமான கலப்பு லேமினேட்டிங் இயந்திரம் மற்றும் பயன்படுத்தப்பட்ட வேலை கொள்கை மற்றும் உலர் கலப்பு முறை ஆகியவை அடிப்படையில் ஒரே மாதிரியானவை, வேறுபாடு என்பது பசை பூசப்பட்ட முதல் அடி மூலக்கூறு, முதலில் இரண்டாவது அடி மூலக்கூறு லேமினேட் கலவையுடன், பின்னர் அடுப்பால் உலர்த்தப்படுகிறது. எளிய, குறைந்த பிசின் அளவு, கூட்டு வேகம், கலப்பு தயாரிப்புகளில் எஞ்சியிருக்கும் கரைப்பான்கள் இல்லை, சுற்றுச்சூழலுக்கு மாசு மாற்று.
3 、 எக்ஸ்ட்ரூஷன் கூட்டு
எக்ஸ்ட்ரூஷன் கலவை என்பது கூட்டு செயல்முறையின் மிகவும் பொதுவான முறையாகும், இது தெர்மோபிளாஸ்டிக் பிசினின் மூலப்பொருளாகப் பயன்படுத்தப்படுகிறது, பிசின் சூடாகவும், அச்சுக்குள் உருகவும், படத்தின் தாள் குணப்படுத்துதலுக்குப் பதிலாக இறக்கும் வாயால், மற்றொரு வகை அல்லது இரண்டு படங்களுடன் ஒன்றாக இணைந்தவுடன், பின்னர் குளிர்ச்சியடைந்து குணப்படுத்தப்படுகிறது. மல்டி-லேயர் கோ-எக்ஸ்ட்ரூஷன் லேமினேஷன் என்பது பிளாஸ்டிக் பிசினின் பல்வேறு வகையான பண்புகள் ஆகும், இது எக்ஸ்ட்ரூடர் இணை வெளியேற்றத்தை விட, படத்தில் டை லேமினேஷனுக்கு.
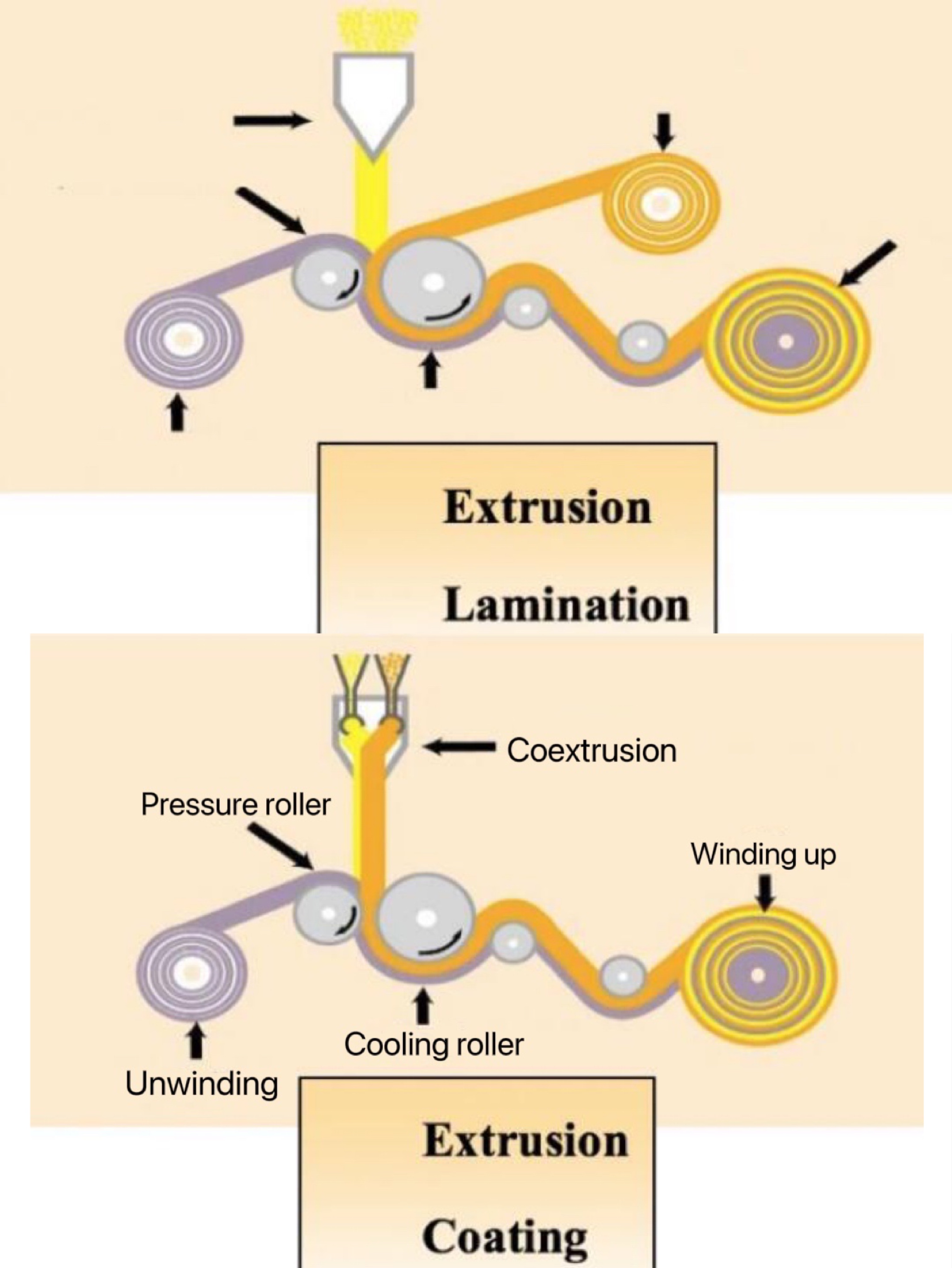
கலப்பு பொருட்கள் தரமான பிரச்சினைகள் மற்றும் தீர்வுகளுக்கு ஆளாகின்றன
நெகிழ்வான பேக்கேஜிங்கின் உற்பத்தி மற்றும் செயலாக்கத்தில் கூட்டு என்பது ஒரு முக்கியமான செயல்முறையாகும், அதன் பொதுவான தோல்விகள்: காற்று குமிழ்கள் உற்பத்தி, கலவைக்கு குறைந்த வேகத்தன்மை, முடிக்கப்பட்ட தயாரிப்புகள் சுருக்கப்பட்ட மற்றும் உருட்டப்பட்ட விளிம்புகள், கலப்பு தயாரிப்புகள் நீட்சி அல்லது சுருக்கம் போன்றவை. இந்த பிரிவு, காரணங்கள் மற்றும் எலிமினேஷனின் முறைகளின் சுருக்கமான, உருட்டப்பட்ட விளிம்புகளின் பகுப்பாய்வில் கவனம் செலுத்தும்.
1 、 சுருக்க நிகழ்வு
இந்த நிகழ்வின் உலர்ந்த கலப்பு தோல்வி தோல்வியின் பெரும் பகுதியை ஆக்கிரமிக்கிறது, முடிக்கப்பட்ட தயாரிப்பு பை தயாரிப்பின் தரத்தை நேரடியாக பாதிக்கிறது.
இந்த தோல்விக்கான முக்கிய காரணங்கள் பின்வருமாறு.
கலப்பு பொருளின் மோசமான தரம் அல்லது அச்சிடும் அடி மூலக்கூறாக, தடிமன் விலகல், திரைப்பட ரோல்ஸ் இரு முனைகளிலும் தளர்வானவை மற்றும் சமநிலையற்ற முறுக்கு பதற்றம் காரணமாக ஒரு முனையில் இறுக்கமாக இருக்கும். படத்தின் தொகுதி பெரிய, இயந்திரத்தில், படம் மேல் மற்றும் கீழ் மற்றும் வலது வேலைவாய்ப்பு வீச்சு ஆகியவற்றிலிருந்து பிரிக்கப்பட்டால், சூடான டிரம் மற்றும் சூடான பத்திரிகை உருளைகளுக்கு இடையில் பொருள் நுழையும் போது, அது சூடான பத்திரிகை உருளைகளுடன் சமமாக இருக்க முடியாது, எனவே அதை தட்டையாக அழுத்த முடியாது, இதன் விளைவாக முடிக்கப்பட்ட கலப்பு சுருக்கங்கள், தயாரிப்பு ஸ்கிராப்பில், உற்பத்தியில் உள்ளன. கலப்பு பொருள் PE அல்லது CPP ஆக இருக்கும்போது, தடிமன் விலகல் 10μm ஐ விட அதிகமாக இருந்தால், அதை சுருக்கவும் எளிதானது, இந்த நேரத்தில், கலப்பு பொருளின் பதற்றத்தை சரியான முறையில் அதிகரிக்க முடியும், மேலும் சூடான அழுத்தும் ரோலர் வெளியேற்றத்திற்கான கிடைமட்ட நிலையாக மாறும். இருப்பினும், பதற்றம் பொருத்தமானதாக இருக்க வேண்டும் என்பதைக் கவனத்தில் கொள்ள வேண்டும், அதிக பதற்றம் கலப்பு பொருளை நீளமாக்குவது எளிதானது, இதன் விளைவாக பை வாய் உள் சாய்வை ஏற்படுத்துகிறது. கலப்பு பொருளின் தடிமன் விலகல் மிகப் பெரியதாக இருந்தால், அதை உண்மையில் பயன்படுத்த முடியாது, கையாளப்பட வேண்டும்.
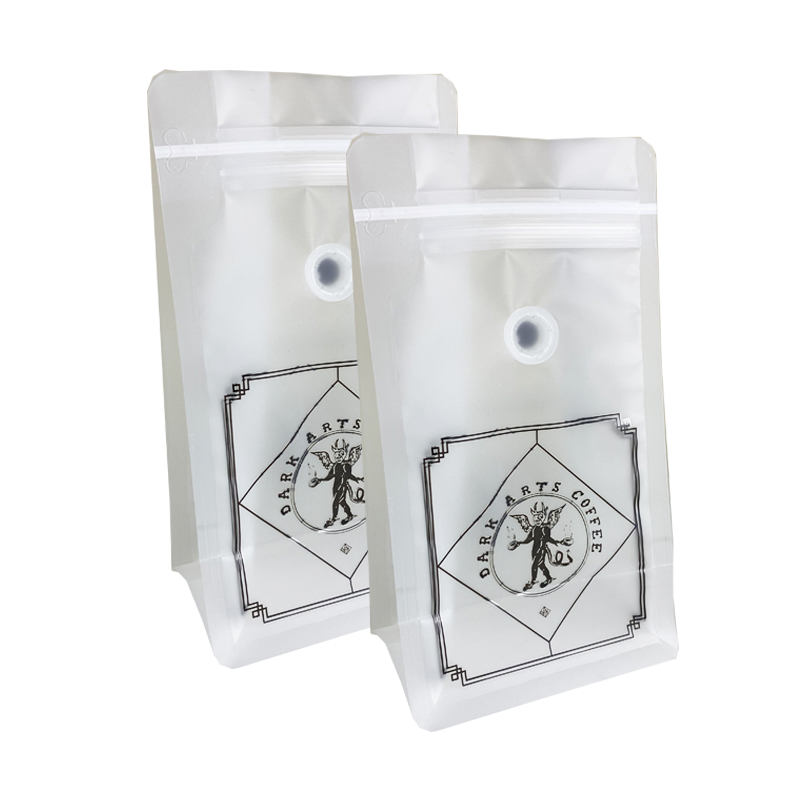
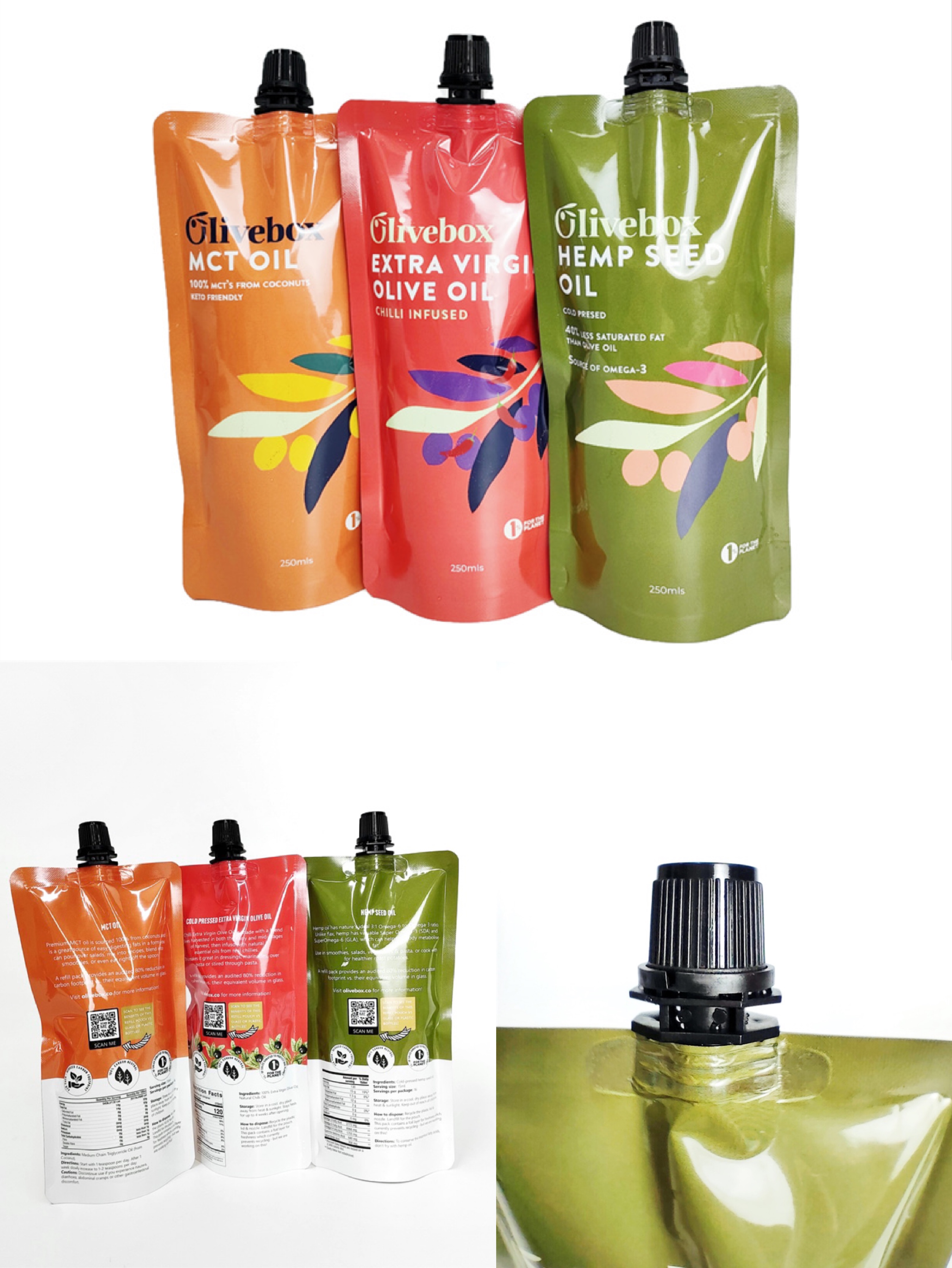
2 、 கலப்பு வெள்ளை புள்ளிகள்
மோசமான மை கவரேஜ் வீதத்தின் விளைவாக வெள்ளை புள்ளிகள்: கலப்பு வெள்ளை மைக்கு, மை உறிஞ்சுதல் ஆவியாகும் ஆனால் வெள்ளை புள்ளிகளால் ஏற்படும் ஆவியாகும் தன்மை இல்லாதபோது, முறையின் உலர்த்தும் திறனை மேம்படுத்த கிடைக்கும்போது; இன்னும் வெள்ளை புள்ளிகள் இருந்தால், வெள்ளை மையின் நேர்த்தியைச் சரிபார்ப்பது போன்ற வெள்ளை மை கவரேஜை மேம்படுத்துவதே பொதுவான தீர்வு, ஏனெனில் நல்ல மை கவரேஜ் வீதத்தின் அரைக்கும் நேர்த்தியானது வலுவானது.
சமமாக உற்பத்தி செய்யப்படும் வெள்ளை புள்ளிகளுக்கு பதிலாக பிசின்: பசை பூசப்பட்ட மை அடுக்கில், மை நுழைவதால் கரைப்பான், மேற்பரப்பு பதற்றம் மற்றும் அடி மூலக்கூறைக் காட்டிலும் சிறியதாக இருக்கும், சமன் செய்வது பசை, பசை மந்தநிலைகள் மற்றும் அலுமினிய-பூசப்பட்ட மேற்பரப்பு அல்லது அலுமினிய பூசப்பட்ட மேற்பரப்பு அல்லது அலுமினிய பூசப்பட்ட மேற்பரப்பு அல்லது அலுமினிய பூசப்பட்ட மேற்பரப்பு போன்றவற்றின் மூலம், குமிழி அல்லது குமிழி போன்றவற்றின் மூலம் பிரதிபலிக்கும் போது, வெளிச்சம் போன்றவை அல்ல. சீரான ரப்பர் ரோலருடன் பூச்சுகளை மென்மையாக்க அல்லது மாற்றீட்டின் அளவை அதிகரிக்க தீர்வு பயன்படுத்தப்படலாம்.
3 、 கூட்டு குமிழி
கலப்பு குமிழ்கள் பின்வரும் சூழ்நிலைகள் மற்றும் தொடர்புடைய முறைகளில் உருவாக்கப்படுகின்றன.
நிகழ்வில் கலவை குமிழ்கள்
1. மோசமான படம், பிசின் செறிவை மேம்படுத்த வேண்டும் மற்றும் மாற்றீட்டின் அளவு, எம்எஸ்டி, கேபிடி மேற்பரப்பு ஈரமாக்குவது எளிதல்ல, குமிழ்களை உற்பத்தி செய்ய எளிதானது, குறிப்பாக குளிர்காலத்தில். மை மீது காற்று குமிழ்கள்,முடியும்அகற்ற பிசின் அளவை அதிகரிக்கும் முறையைப் பயன்படுத்தவும்.
2、மை மேற்பரப்பு பம்ப் மற்றும் குமிழி, மூட்டு கூட்டு வெப்பநிலை மற்றும் அதிகரிக்க அழுத்தம் ஆகியவற்றை கூட்டு செய்ய வேண்டும்.
3, மை மேற்பரப்பில் பசை சேர்ப்பதன் அளவு குறைவாக உள்ளது, கூட்டு ரோலர் பிரஷர் பேஸ்ட் நேரத்தையும், மென்மையான உருளைகளின் பயன்பாட்டையும் அதிகரிக்க வேண்டும், கூட்டு வேகத்தைக் குறைக்க, நல்ல ஈரப்பத பசை மற்றும் மை சரியான தேர்வு ஆகியவற்றைத் தேர்வுசெய்ய போதுமானதாக இருக்கும்.
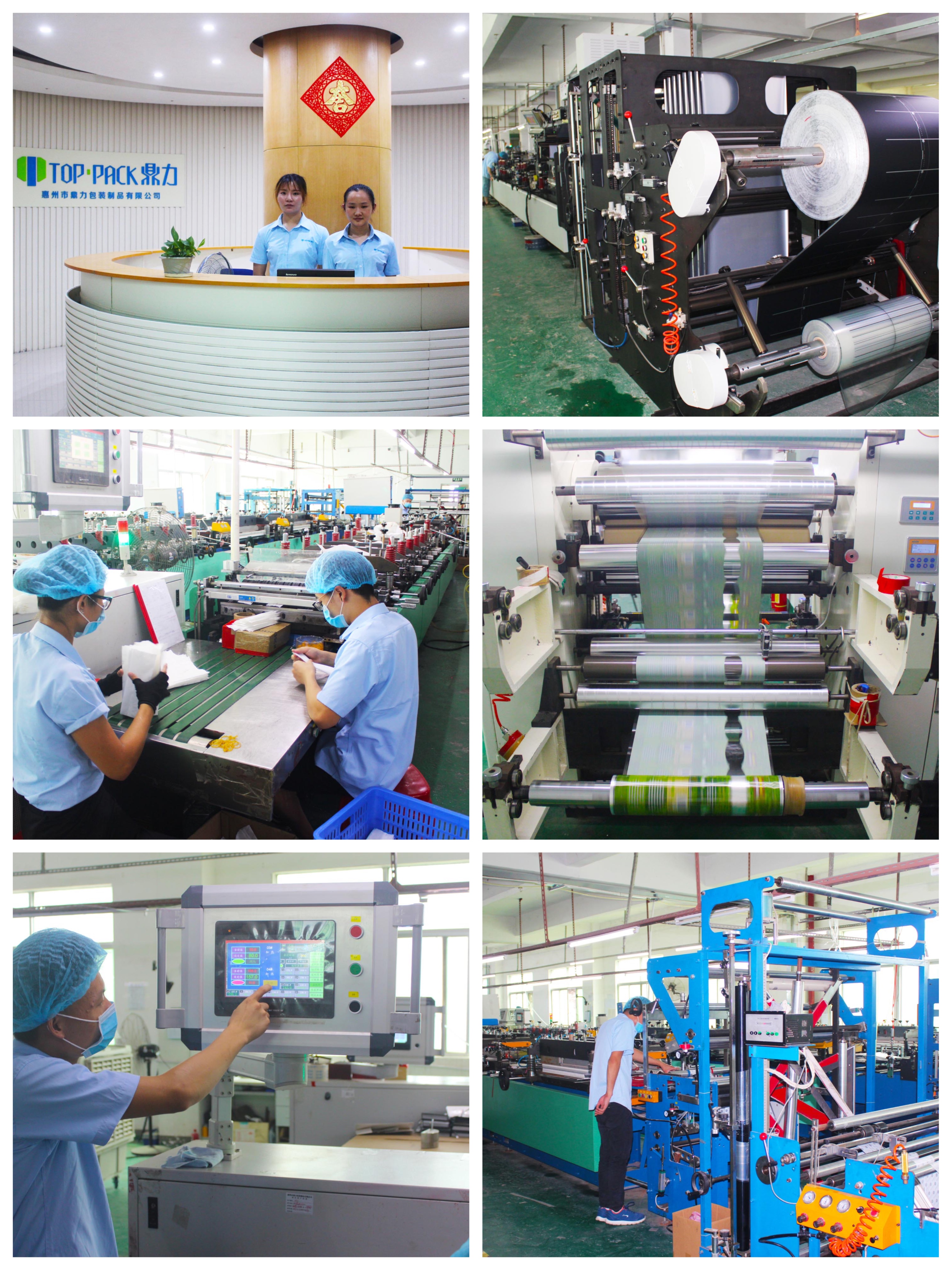
4. படத்தில் உள்ள சேர்க்கைகள் (மசகு எண்ணெய், ஆண்டிஸ்டேடிக் முகவர்) பசை மூலம் ஊடுருவுகின்றன, எனவே நீங்கள் அதிக மூலக்கூறு எடை மற்றும் வேகமான குணப்படுத்துதலுடன் பசை தேர்வு செய்ய வேண்டும், பசை செறிவை அதிகரிக்க வேண்டும், அடுப்பு வெப்பநிலையை பசை முழுமையாக உலர வைக்க வேண்டும், மேலும் 3 மாதங்களுக்கு மேல் வேலை வாய்ப்பு காலத்துடன் படத்தைப் பயன்படுத்தக்கூடாது, ஏனெனில் கொரோனா சிகிச்சை இழந்துவிட்டது.
5、குளிர்காலத்தில் வெப்பநிலை குறைவாக உள்ளது, படம் மற்றும் மை பரிமாற்றத்துடன் இணைத்தல், சீரமைப்பு விளைவு மீட்டமைத்தல் நன்றாக இல்லை, எனவே செயல்பாட்டு இடம் ஒரு குறிப்பிட்ட வெப்பநிலையை வைத்திருக்கிறது.
6、உலர்த்தும் வெப்பநிலை மிக அதிகமாக உள்ளது, பிசின் கொப்புளம் அல்லது மேற்பரப்பு தோலின் மேலோடு ஏற்படுகிறது, மற்றும் உள்ளே உலரவில்லை, எனவே பிசின் உலர்த்தும் வெப்பநிலையை சரிசெய்ய வேண்டும்.
7. கலப்பு உருளைகள் படத்திற்கு இடையில் காற்று நுழைகிறது, கலப்பு உருளைகளின் வெப்பநிலை அதிகரிக்கப்பட வேண்டும் மற்றும் கலப்பு கோணத்தை சிதைக்க வேண்டும் (படம் தடிமனாக இருக்கும் மற்றும் கடினமாக இருக்கும்போது குமிழ்களை உற்பத்தி செய்வது எளிது).
8、அதிக திரைப்படத் தடையின் காரணமாக, பிசின் குணப்படுத்துதலால் தயாரிக்கப்படும் CO2 வாயு, கலப்பு படத்தில் எஞ்சியிருக்கும், குமிழியில் அச்சிடப்படவில்லை, குணப்படுத்தும் முகவரின் அளவை மேம்படுத்த வேண்டும், இதனால் பிசின் குணப்படுத்துதல் உலர்ந்தது.
9. ரப்பரில் உள்ள கிளைகோலிக் அமிலம் மை நிரப்பிக்கு ஒரு நல்ல கரைப்பான், ரப்பர் மை கரைக்கிறது, மேலும் மை மீது குமிழ்கள் மட்டுமே உள்ளன, அவை ரப்பரில் நீர் ஊடுருவலைத் தவிர்க்க வேண்டும் மற்றும் மை கலைக்கப்படுவதைக் குறைக்க ரப்பரின் உலர்த்தும் வெப்பநிலையை மேம்படுத்த வேண்டும்.
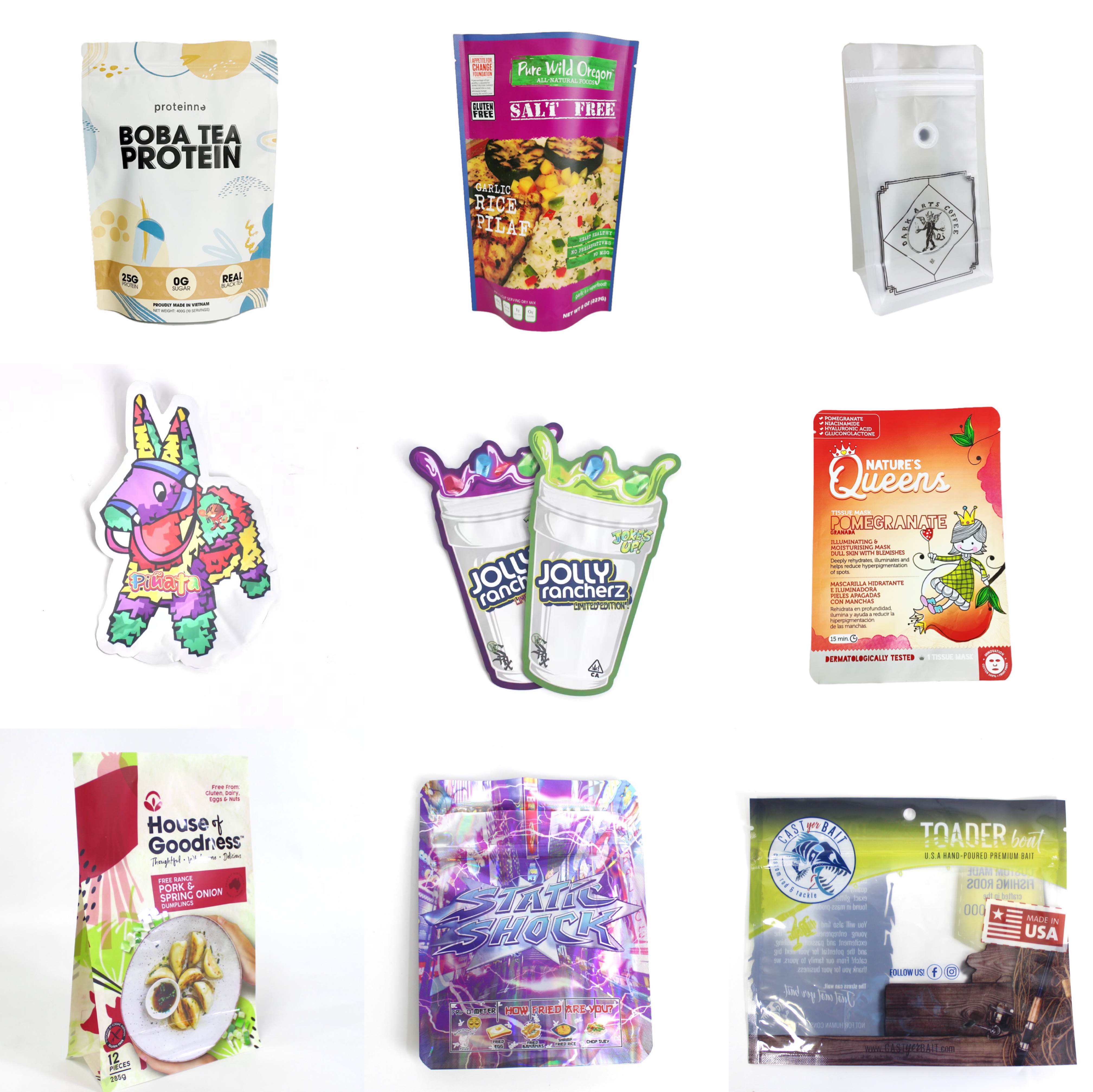
4 、 மோசமான தலாம் வலிமை
பீல் வலிமை மோசமாக உள்ளது, முழுமையற்ற குணப்படுத்துதல் காரணமாகும், அல்லது பசை அளவு மிகக் குறைவு, அல்லது பயன்படுத்தப்படும் மை மற்றும் பிசின் நிலைமையுடன் பொருந்தவில்லை, இருப்பினும் குணப்படுத்துதல் முடிந்தது, ஆனால் நீளம் இல்லாததால் கலப்பு படத்தின் இரண்டு அடுக்குகளுக்கு இடையில் சக்தி குறைப்பைக் குறைத்துள்ளது.
பசை ஊசி அளவு மிகவும் சிறியது, பிசின் விகிதம் குறைக்கப்படுகிறது, பசை சேமிப்பில் மோசமடைகிறது, நீர் மற்றும் ஆல்கஹால் பசை கலக்கப்படுகின்றன, படத்தில் உள்ள துணை நிறுவனங்கள் துரிதப்படுத்தப்படுகின்றன, உலர்த்தும் அல்லது முதிர்வு செயல்முறை இடம் இல்லை, முதலியன, இது இறுதி கலவையான தலாம் வலிமை குறைப்பு காரணிகளுக்கு வழிவகுக்கும்.
பசை சரியான சேமிப்பிற்கு கவனம் செலுத்துங்கள், மிக நீளமானது 1 வருடத்திற்கு மேல் இல்லை (TIN CAN CANDED); வெளிநாட்டு பொருட்கள் பசை, குறிப்பாக நீர், ஆல்கஹால் போன்றவற்றில் நுழைவதைத் தடுக்கவும், அவை பசை தோல்வியை ஏற்படுத்தும். பசை பூச்சுகளின் அளவை மேம்படுத்த பொருத்தமான படம்; உலர்த்தும் வெப்பநிலை காற்றின் அளவை மேம்படுத்தவும், கூட்டு வேகத்தைக் குறைக்கவும். மேற்பரப்பு பதற்றத்தை மேம்படுத்த திரைப்பட மேற்பரப்பின் இரண்டாவது சிகிச்சை; பட கூட்டு மேற்பரப்பில் சேர்க்கைகளின் பயன்பாட்டைக் குறைக்கவும். இந்த முறைகள் அனைத்தும் கலவையின் மோசமான பீல் வலிமையின் சிக்கலை மேம்படுத்த எங்களுக்கு உதவும்.
5. வெப்ப முத்திரை கெட்டது
கூட்டு பை வெப்ப முத்திரை மோசமான செயல்திறன் மற்றும் அதன் காரணங்கள் அடிப்படையில் பின்வரும் சூழ்நிலைகள்.
வெப்ப சீல் வலிமை மோசமாக உள்ளது. நிகழ்விற்கான முக்கிய காரணங்கள் முழுமையாக குணப்படுத்தப்படவில்லை அல்லது வெப்ப சீல் வெப்பநிலை மிகக் குறைவு. குணப்படுத்தும் செயல்முறையை மேம்படுத்தவும் அல்லது சீல் கத்தி வெப்பநிலையை சரியான முறையில் அதிகரிக்கவும் சிக்கலை மேம்படுத்தலாம்.
வெப்ப முத்திரை கவர் டெலமினேஷன் மற்றும் ஒளிவிலகல் குறியீடு. இந்த நிகழ்வின் முக்கிய காரணம் பிணைப்பு குணப்படுத்தப்படவில்லை. குணப்படுத்தும் நேரத்தை சரிசெய்யவும் அல்லது குணப்படுத்தும் முகவர் உள்ளடக்கத்தை சரிசெய்யவும் இந்த சிக்கலை மேம்படுத்தலாம்.
உள் அடுக்கு படத்தின் மோசமான திறந்த தன்மை / மோசமான திறந்த தன்மை. இந்த நிகழ்வின் காரணம் மிகக் குறைந்த தொடக்க முகவர், இதன் விளைவாக அதிகப்படியான பொருள் (மாற்றியமைப்பாளர்) மற்றும் ஒட்டும் அல்லது க்ரீஸ் திரைப்பட மேற்பரப்பு. தொடக்க முகவரின் அளவை அதிகரிப்பதன் மூலமும், மாற்றியமைப்பின் அளவை சரிசெய்வதன் மூலமும், பட மேற்பரப்பில் இரண்டாம் நிலை மாசுபாட்டைத் தவிர்ப்பதன் மூலமும் இந்த சிக்கலை மேம்படுத்தலாம்.
முடிவு
உங்கள் வாசிப்புக்கு நன்றி, உங்கள் கூட்டாளர்களாக இருப்பதற்கான வாய்ப்பு எங்களுக்கு உள்ளது என்று நம்புகிறோம்.
உங்களிடம் ஏதேனும் கேள்வி கேட்க விரும்பினால், தயவுசெய்து எங்களுக்குத் தெரியப்படுத்தவும், எங்களை தொடர்பு கொள்ளவும் தயங்கவும்.
தொடர்பு:
மின்னஞ்சல் முகவரி:fannie@toppackhk.com
வாட்ஸ்அப்: 0086 134 10678885
இடுகை நேரம்: ஏபிஆர் -01-2022